Understanding the Costs of Sand Casting A Comprehensive Analysis
Sand casting is one of the oldest and most versatile manufacturing processes in the metalworking industry. It involves creating a sand mold into which molten metal is poured to create a desired shape. While it offers numerous advantages, including high versatility and low cost for short production runs, it's essential to understand the various factors that influence the overall cost of sand casting.
1. Material Costs
The primary costs in sand casting revolve around the materials used. The key components include the casting metal, sand, and molding materials. The type of metal chosen for casting—whether it's aluminum, iron, or bronze—can significantly affect the price. For instance, aluminum tends to be less expensive and is lighter than iron, making it a popular choice for various applications. The quality of the sand also impacts costs; high silica content sand is preferable but can be more expensive.
2. Mold Design
The design of the mold is a crucial aspect of sand casting that can greatly influence cost. A complex mold with intricate details requires more initial investment in terms of design and production time. Simpler designs, while reducing costs, may not always meet the specifications required for certain applications. Additionally, molds that are reusable can offer cost savings in a production environment, as they can be used multiple times before needing replacement.
3. Labor Costs
Labor costs are another significant factor in sand casting. Skilled labor is often required to prepare molds and manage the pouring process. Additionally, the complexity of the casting operation will dictate the amount of time and expertise needed. In regions where labor costs are high, such as developed countries, these expenses can have a substantial impact on the overall cost of sand casting operations. Companies might consider relocating or outsourcing to countries with lower labor costs; however, this can introduce challenges related to quality control and logistics.
sand casting cost
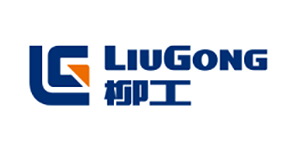
4. Equipment and Maintenance
The initial investment in equipment for sand casting can be substantial. This includes furnaces for melting metal, sand mixers, and other specialized machinery. Ongoing maintenance is also a significant cost factor, as regular upkeep is necessary to ensure efficient operations and avoid downtime. Organizations must factor in these equipment costs when determining the total cost of sand casting.
5. Production Volume
Sand casting is particularly cost-effective for small to medium production runs, as the initial setup costs are low compared to other methods, such as die casting. However, if production volume increases significantly, economies of scale can be achieved, making it possible to reduce the cost per unit further. Conversely, for very small runs, the cost per item may become prohibitive, prompting businesses to consider alternative methodologies.
6. Additional Costs
Other costs associated with sand casting include shipping, handling, and any post-casting processes like machining, finishing, or coating. These additional costs can affect the overall price significantly, especially if the casted parts require further modification before they can be put into use.
Conclusion
In conclusion, while sand casting offers a relatively low-cost solution for many manufacturing needs, understanding the various factors that influence its cost is crucial for businesses looking to optimize their operations. From material choice and mold design to labor and equipment costs, each element plays a vital role in determining the overall price of a sand casting project. By carefully considering each of these factors, manufacturers can make informed decisions that enhance their cost efficiency and productivity. As industries continue to evolve, staying abreast of technological advancements and cost management strategies in sand casting will be vital in maintaining competitiveness in the field.
Post time:நவ் . 10, 2024 15:32
Next:Exploring the Techniques and Advantages of Sand Casting in Modern Manufacturing