Lost Foam Casting Method An Overview
Lost foam casting is an innovative and efficient manufacturing technique that is increasingly gaining popularity in various industries, including automotive, aerospace, and art foundries. This process allows for the creation of complex metal parts with high precision and minimal waste. By understanding the lost foam casting method, manufacturers can optimize production, reduce costs, and expand their design capabilities.
The basic principle of lost foam casting involves the use of a foam pattern made typically from polystyrene. In contrast to traditional sand casting, where a solid mold is created, the lost foam method utilizes the foam pattern itself as the mold. The pattern is coated with a refractory material, often a mixture of sand and a bonding agent, which helps to maintain its shape during the casting process. Once the foam patterns are coated and prepared, they are assembled into a cluster or tree, shaped according to the final part requirements.
The process begins with creating a foam pattern that accurately represents the part to be cast. This pattern can be easily produced through techniques such as CNC machining or 3D printing. The use of foam is advantageous as it is lightweight, cost-effective, and capable of producing intricate designs with excellent surface finishes. After the patterns are made, they are then coated with a thin layer of refractory material. This coating serves two primary functions it provides a refractory barrier that can withstand the molten metal's temperature and allows for a precise replication of the pattern's surface details.
Once coated, the foam patterns are assembled into a larger structure if multiple patterns are required for a single casting session. This assembly is then placed in a casting flask, and the molten metal is poured over the foam patterns. As the molten metal flows into the mold cavity, it simultaneously vaporizes the foam, which escapes as gas. This unique feature of lost foam casting allows the resulting metal part to be created in the exact shape of the foam pattern without the need for a traditional mold, thus eliminating many of the issues associated with mold construction and modification.
lost foam casting method
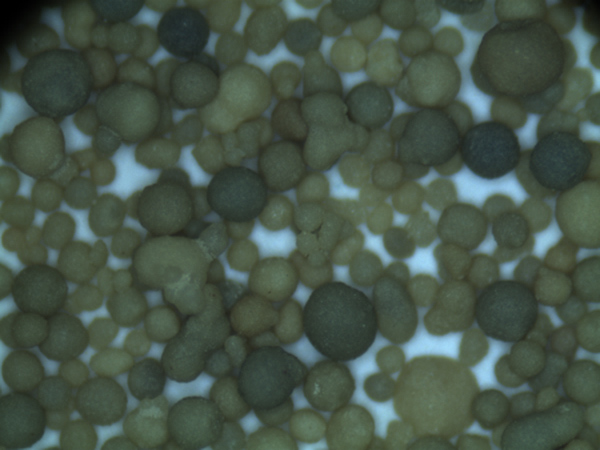
One of the primary advantages of the lost foam casting method is its ability to produce complex geometries that would be difficult or impossible to achieve with traditional methods. The elimination of the mold simplifies the design process, allowing engineers and designers greater freedom in their creative endeavors. Additionally, the process generates minimal waste since the foam is completely consumed during casting, translating to lower material costs and reduced environmental impact.
Moreover, the lost foam casting process has notable advantages in terms of time efficiency. Traditional casting methods often require separate processes for mold making, which can be time-consuming and resource-intensive. In contrast, the lost foam method streamlines production by consolidating steps and reducing the lead time associated with creating molds.
However, there are also challenges associated with the lost foam casting process. Controlling the properties of the resulting cast parts can be more complex, as factors like foam density, coating thickness, and pouring temperature can significantly influence the final product. To address these issues, operators need to maintain careful control over the casting parameters and invest in quality assurance protocols to minimize defects.
In conclusion, the lost foam casting method stands out as a modern casting technique that provides numerous benefits in terms of design flexibility, efficiency, and sustainability. Its ability to produce intricate and accurate metal components makes it an attractive option for various industries looking to innovate and optimize their production processes. With advancements in materials and technologies, the lost foam casting process is expected to evolve further, paving the way for even more complex applications and broader acceptance in manufacturing practices. As industries strive for higher productivity and lower costs, the lost foam method is likely to remain a vital tool in the pursuit of superior casting solutions.
Post time:நவ் . 10, 2024 09:45
Next:Resin Mixed with Sand for Enhanced Durability and Versatility in Various Applications