Lost Foam Casting A Comprehensive Overview
Lost Foam Casting (LFC) is an advanced metal casting process that has gained popularity due to its ability to produce complex shapes and high-quality finishes. The technique is particularly favored in industries such as automotive, aerospace, and heavy machinery, where precise and intricate components are essential for performance and safety.
The Process Explained
The lost foam casting process begins with the creation of a foam pattern, typically made from expanded polystyrene (EPS). This foam pattern is an exact replica of the final metal part and is manufactured using techniques such as molding and cutting. Once the pattern is complete, it is coated with a refractory material, which serves as a mold material during the casting process.
After coating, the pattern is placed in a flask and surrounded with dry sand. What sets LFC apart from traditional casting methods is the way the foam pattern is handled. When molten metal is poured into the sand mold, the intense heat causes the foam to vaporize, leaving behind a cavity that mirrors the shape of the original foam piece. This results in a seamless and precise mold without the need for complex cores or additional tooling.
Advantages of Lost Foam Casting
One of the primary advantages of lost foam casting is its ability to produce intricate designs with a high degree of accuracy. The foam patterns allow for complex geometries and fine details that would be challenging to achieve using conventional molding techniques. Additionally, since the foam vaporizes during the pouring process, there are no drafts or parting lines typically associated with other casting methods, leading to a superior surface finish.
Another significant benefit is the reduction in the amount of machining required after casting. The LFC process often produces parts that are very close to the final dimensions, which means less material waste and lower production costs. Furthermore, the method is adaptable, allowing manufacturers to easily switch between different designs without investing heavily in new tooling.
lost foam casting
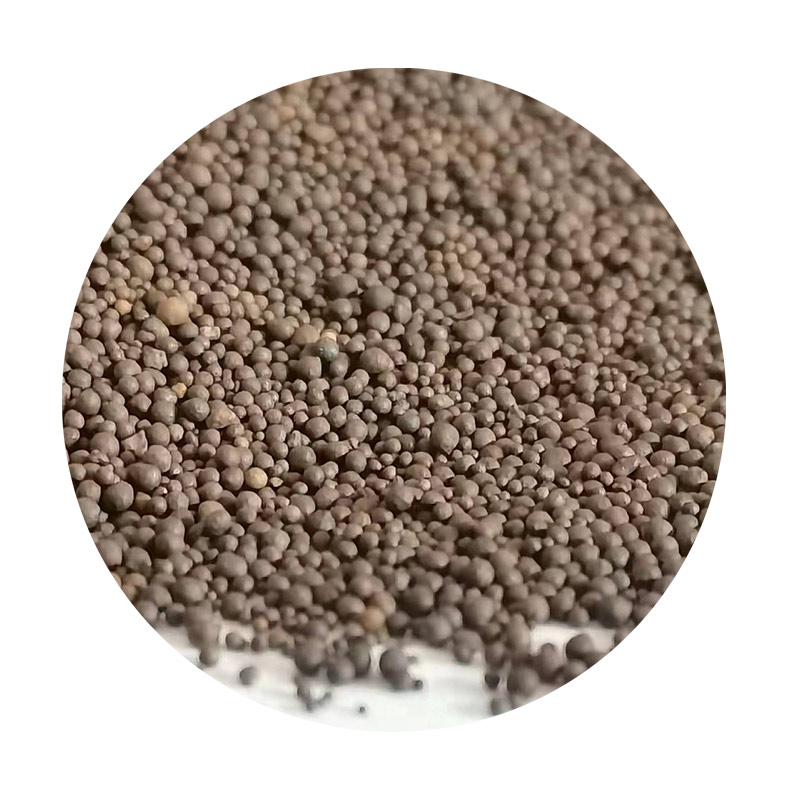
Applications
Lost foam casting is widely used in various industries due to its flexibility. In the automotive sector, it is employed to create engine blocks, transmission cases, and other components that require durability and precision. The aerospace industry also benefits from LFC, using it to produce lightweight and complex parts that meet stringent safety standards.
Moreover, the energy sector utilizes lost foam casting for components like turbine housings and valves that require intricate geometries capable of withstanding high pressures and temperatures. The versatility of LFC makes it suitable for both large-scale production runs and low-volume, high-precision parts.
Environmental and Economic Considerations
In recent years, there has been a growing emphasis on sustainability in manufacturing practices. LFC offers some environmental advantages over traditional casting processes. The use of foam patterns reduces the material waste typically generated during machining, and the process itself often demands less energy due to shorter cycle times and lower levels of thermal stress on equipment.
Economically, with the ability to produce high-quality parts quickly and efficiently, companies can significantly reduce their operational costs. The flexibility of LFC allows businesses to respond rapidly to changes in market demand, making it a viable option for both custom part production and large-scale manufacturing.
Conclusion
Lost foam casting is a sophisticated and efficient method of producing high-quality metal components with intricate details. Its unique capabilities and advantages over traditional casting methods have made it an essential technique in various industries. As technology advances and manufacturers continue to seek sustainable solutions, lost foam casting is likely to remain a pivotal part of the modern metal casting landscape. Whether for automotive parts, aerospace applications, or energy sector components, the future of LFC looks promising, defined by innovation and efficiency.
Post time:நவ் . 12, 2024 01:23
Next:buy sand casting