Lost Foam Casting An Innovative Approach in Manufacturing
Lost foam casting is a cutting-edge manufacturing process that combines the principles of traditional metal casting and modern technology. This technique has gained popularity due to its ability to produce complex shapes with precise dimensions and excellent surface finishes, all while minimizing waste.
The lost foam casting process begins with the creation of a foam pattern, typically made from polystyrene. This pattern is an exact replica of the desired final product. The foam is then coated with a refractory material, which serves as a shell during the casting process. This shell is typically made of a mixture of sand and a bonding agent, which ensures that it can withstand the heat of molten metal.
Once the foam pattern is coated and allowed to cure, it is placed in a flask and surrounded by more sand. The next step involves the pouring of molten metal into the flask. As the metal fills the cavity, it comes into contact with the foam pattern, causing it to evaporate. This is where the term lost foam originates, as the foam is lost in the casting process, leaving behind a void that perfectly mimics its shape.
This method boasts several advantages over traditional casting techniques. Firstly, lost foam casting allows for the production of highly intricate geometries that would be challenging, if not impossible, to achieve with conventional methods. Because the foam can be produced in complex shapes and sizes, manufacturers have greater design flexibility.
lost foam casting
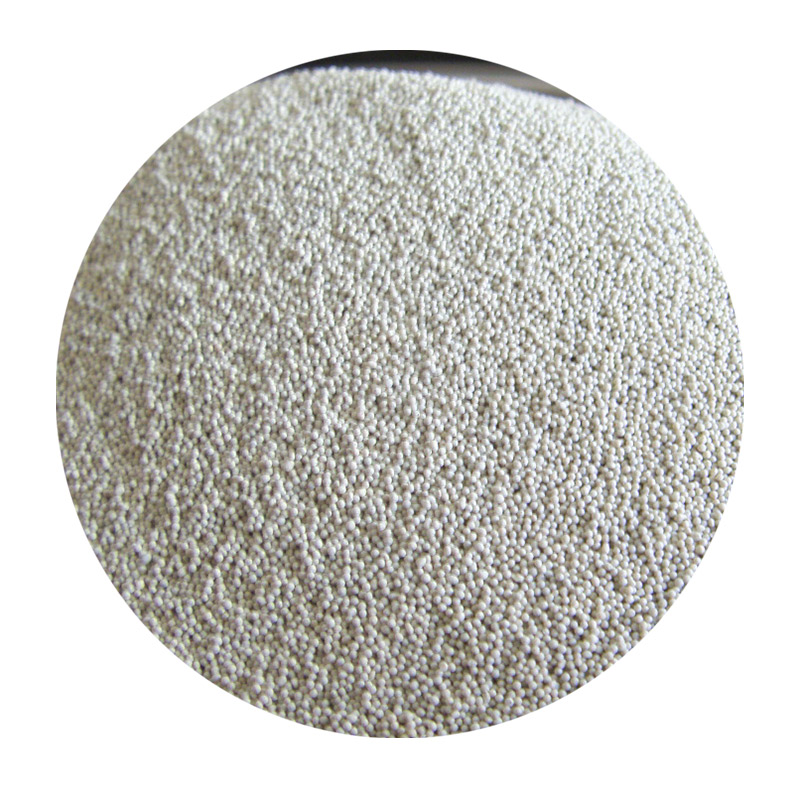
Secondly, the process is highly efficient in terms of material usage. Traditional casting often requires additional machining to reach the desired dimensions, leading to waste. In contrast, lost foam casting typically produces parts that are closer to the final specifications, thus reducing the amount of material that must be removed. This not only saves resources but also contributes to cost-effectiveness in manufacturing.
Furthermore, the lost foam process can accommodate a wide range of metals, including aluminum, iron, and steel. This versatility makes it suitable for various industries, such as automotive, aerospace, and machinery manufacturing. The ability to cast complex shapes in different materials enhances its appeal across sectors.
Safety is another significant advantage of lost foam casting. Since the foam is lost during the process, there are fewer concerns regarding handling and disposing of the pattern material. The use of expanded polystyrene also has a lower environmental impact compared to conventional wax patterns used in similar casting techniques.
Despite its many benefits, lost foam casting is not without challenges. The initial investment in equipment and technology can be significant, which may deter smaller manufacturers. Additionally, controlling the process parameters is crucial to ensure high-quality casts, requiring skilled operators.
In conclusion, lost foam casting stands out as a revolutionary process in the field of manufacturing. Its ability to create complex shapes with minimal waste and superior finish makes it a preferred choice for many industries. As technology advances and the demand for precision engineering continues to grow, lost foam casting is likely to become an increasingly integral part of the manufacturing landscape, offering both innovation and efficiency.
Post time:நவ் . 03, 2024 14:09
Next:sand casting benefits