Lost Foam Casting A Modern Approach to Metal Casting
Lost foam casting (LFC) is an advanced metal casting process that offers numerous advantages over traditional methods. It integrates features from both investment casting and traditional sand casting, resulting in a highly efficient and cost-effective technique. As industries continually seek innovative ways to improve production quality and reduce costs, lost foam casting has emerged as a viable solution in various sectors, including automotive, aerospace, and art casting.
The Process of Lost Foam Casting
The lost foam casting process begins with a foam pattern, typically made of expanded polystyrene (EPS), which is crafted to match the exact specifications of the final product. This foam pattern is coated with a fine layer of refractory material, often silica sand mixed with a binding agent. Once the coating is applied, the foam pattern is heated, causing it to melt away and leave a cavity in the shape of the desired casting.
The next step involves pouring molten metal into this cavity. The foam pattern evaporates almost instantly upon contact with the molten metal, creating a vacuum that allows the molten material to fill the cavity completely. This unique aspect of lost foam casting not only minimizes the potential for defects but also allows for intricate designs and complex shapes that would be challenging to achieve using conventional casting methods.
Advantages of Lost Foam Casting
One of the primary benefits of lost foam casting is its ability to produce high-quality castings with exceptional surface finishes
. Since the foam pattern provides a near-net shape, the need for extensive machining and finishing processes is significantly reduced, leading to both time and cost savings. Furthermore, the elimination of sand cores in many cases simplifies the overall process and minimizes the risk of defects related to core strength and alignment.lost foam casting
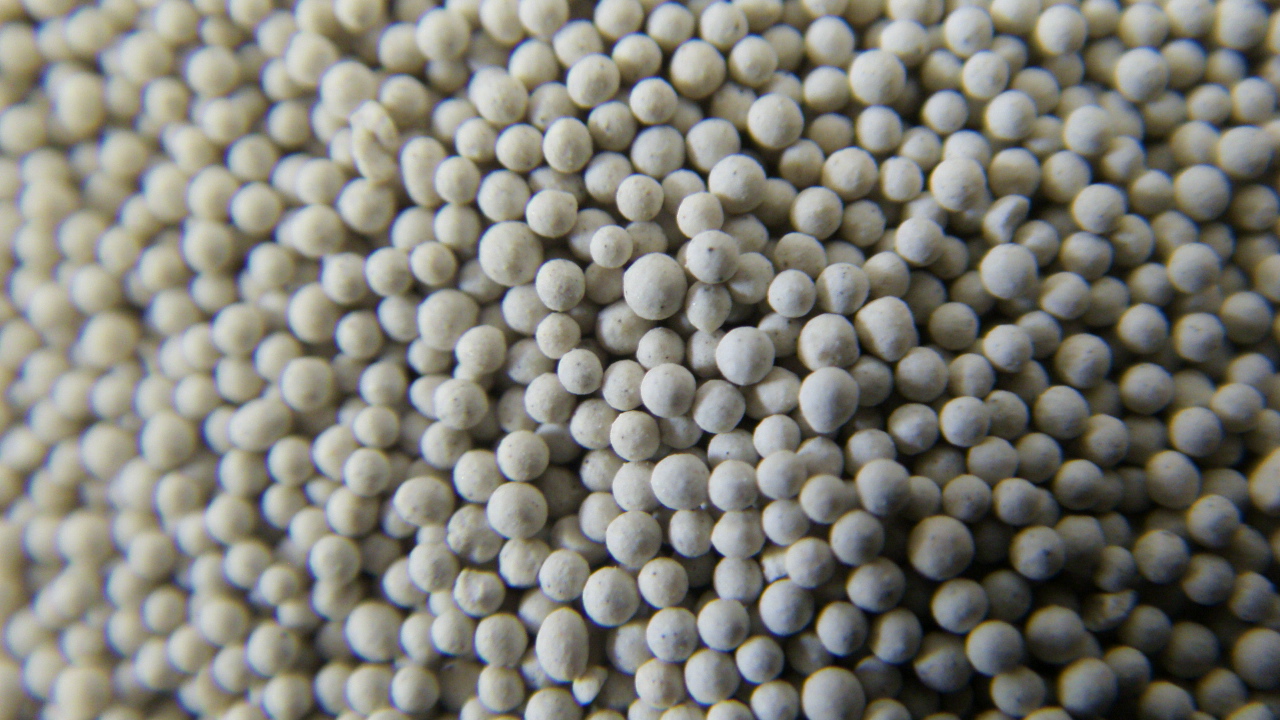
Additionally, lost foam casting can accommodate a variety of metals, including aluminum, iron, and various alloys. This versatility makes it an attractive option for different industries, particularly in producing lightweight components for automotive and aerospace applications. The casting process also lends itself to recycling materials, contributing to sustainable manufacturing practices.
Challenges and Considerations
While lost foam casting presents numerous advantages, it is not without its challenges. The initial setup costs for equipment and pattern creation can be higher than traditional methods. Furthermore, controlling the temperature and timing during the pouring process is critical to avoid defects such as misruns, cold shuts, and porosity. With careful attention to these factors, manufacturers can yield high-quality components that meet the stringent demands of modern engineering.
Another consideration is the skill level required for operators and engineers overseeing the process. Training is essential to ensure that all elements of the casting process, from pattern making to pouring and finishing, are performed correctly. This expertise significantly contributes to the success and reliability of the lost foam casting process.
Conclusion
Lost foam casting represents a significant advancement in the field of metal casting, providing manufacturers with a method to create complex, high-quality parts more efficiently and cost-effectively. With its ability to produce intricate designs while reducing waste and machining time, lost foam casting is an attractive option for a range of applications. As industries continue to evolve and adapt to new technologies, lost foam casting will likely play an essential role in shaping the future of manufacturing. By addressing the challenges and leveraging the advantages of this innovative technique, businesses can meet the growing demands for precision and efficiency in metal casting.
Post time:அக் . 15, 2024 00:14
Next:china sand casting