Lost Foam Sand Casting An Innovative Approach to Metal Casting
Lost foam sand casting is an advanced manufacturing process that combines the advantages of traditional sand casting and foam pattern technology. This technique innovatively addresses some of the limitations associated with conventional casting methods, providing manufacturers with enhanced precision, cost-effectiveness, and flexibility.
At its core, lost foam sand casting involves creating a foam pattern that is an exact replica of the desired final product. This pattern is typically made from polystyrene foam, which is lightweight yet capable of withstanding the rigors of the casting process. The foam pattern is coated with a thin layer of a refractory material to enable it to withstand molten metal temperatures.
The process begins by placing the foam pattern into a flask and surrounding it with dry sand, which is then compacted to create a mold. Once the mold is prepared, molten metal is poured directly into it. As the metal fills the cavity, the heat from the molten material causes the foam pattern to vaporize, leaving behind a perfect impression of the original shape. This characteristic gives the method its name—lost foam, as the pattern is lost during the casting process.
lost foam sand casting
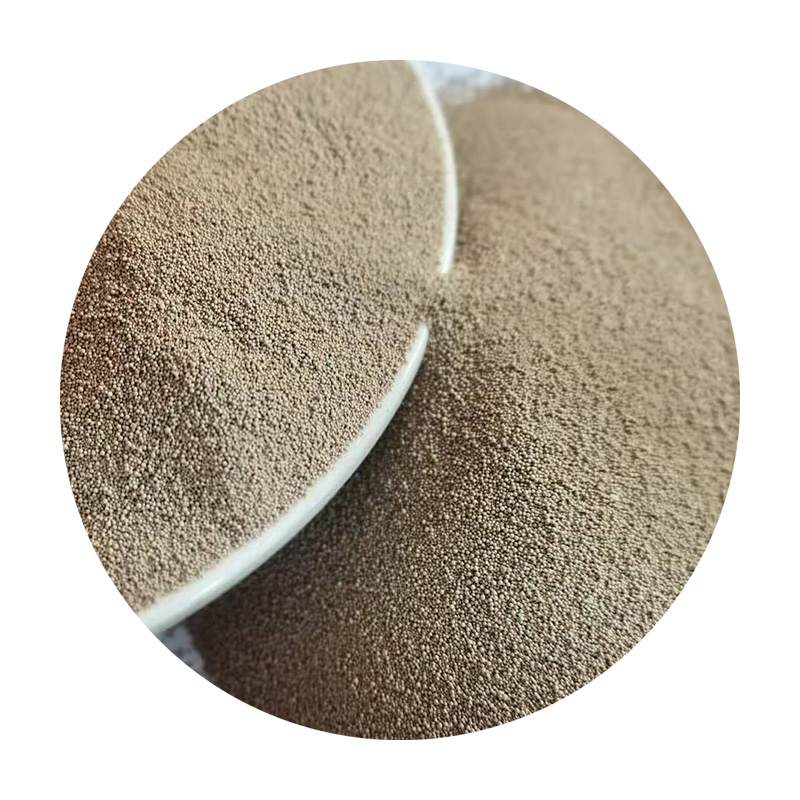
One of the key benefits of lost foam sand casting is the ability to produce complex shapes with intricate details. Because the foam pattern can be easily molded, manufacturers are able to create components that would otherwise be challenging or impossible to achieve using traditional methods. This flexibility opens up new possibilities for a wide range of applications, from automotive parts to intricate artistic pieces.
Additionally, lost foam sand casting significantly reduces machining times and material waste. Since the foam pattern can be fabricated with a high degree of accuracy, the resulting castings often require minimal finishing work, leading to lower production costs. This efficiency is particularly advantageous in industries where large volumes of parts are needed on a regular basis.
Moreover, this method is environmentally friendly compared to other casting techniques. The use of polystyrene foam, which can be recycled or reused, minimizes the waste typically generated during manufacturing. Furthermore, the process generates fewer emissions and reduces the overall energy consumption associated with traditional melting and casting operations.
In conclusion, lost foam sand casting represents a significant advancement in the field of metal casting. Its ability to produce complex shapes with high precision, combined with the benefits of cost-effectiveness and reduced environmental impact, makes it an attractive option for manufacturers looking to innovate and improve their production processes. As technology continues to evolve, the adoption of lost foam sand casting is expected to grow, paving the way for new applications and advancements in manufacturing.
Post time:ஆக . 31, 2024 01:53
Next:Comprehensive Guide to Sand Casting Sand Types