Understanding Industrial Sand Casting A Comprehensive Overview
Industrial sand casting, a prevalent manufacturing process dating back thousands of years, plays a crucial role in producing complex metal parts for various industries. The method involves pouring molten metal into a sand mold, where it solidifies into the desired shape. This article delves into the fundamental aspects of industrial sand casting, its advantages, applications, and some challenges faced in the process.
The Sand Casting Process
The sand casting process begins with the preparation of a mold made from a sand mixture, often combined with clay and water. The mixture’s properties enable the mold to retain shape and withstand the high temperatures of molten metal. The first step involves creating a pattern, typically from durable materials such as wood, metal, or plastic, which defines the shape of the finished product.
Once the pattern is prepared, it is placed in a mold box and covered with the sand mixture. This mixture is compacted around the pattern to form a mold. After the pattern is removed, the sand mold consists of two halves the cope (top) and the drag (bottom). Pouring holes, or gates, are also created to allow molten metal to flow into the mold cavities.
The next stage is pouring the molten metal, which can be derived from various sources, including aluminum, iron, and steel, into the prepared mold. This step requires precise temperature control to ensure quality and integrity. Once cooled and solidified, the mold is broken apart, and the cast part is retrieved. Finally, any imperfections are removed, and the finished product is subjected to quality controls to ensure it meets the required specifications.
Advantages of Sand Casting
Industrial sand casting offers numerous benefits that contribute to its widespread use. One of the primary advantages is its versatility. The process can be used to create intricate shapes and large parts that may be challenging to produce using other methods. Additionally, sand casting is suitable for a wide range of metals, making it adaptable for various applications.
Cost-effectiveness is another significant benefit. The equipment needed is relatively inexpensive compared to other casting methods, and the materials used in sand casting, such as sand and clay, are readily available. Furthermore, the ability to produce both small and large batches makes sand casting a suitable option for everything from prototype development to high-volume production.
industrial sand casting
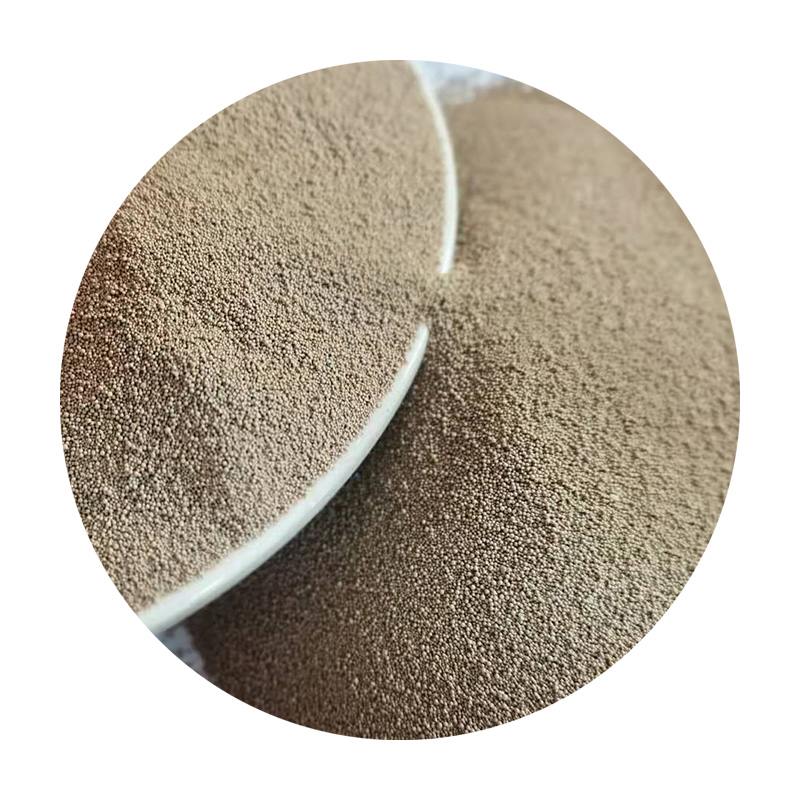
Moreover, sand casting allows for minimal waste generation, as excess sand can often be recycled and reused, reducing the environmental impact of the operation.
Applications of Sand Casting
Industrial sand casting is utilized in various sectors, including automotive, aerospace, construction, and electronics. In the automotive industry, it is commonly used to manufacture engine blocks, transmission cases, and other critical components. Aerospace applications often involve complex parts such as turbine casings and structural elements that benefit from the intricate detailing achievable through sand casting.
In the construction industry, sand casting plays a vital role in creating large, durable components like bridge supports and machinery parts. The electronics sector also leverages this method to produce housing for various devices.
Challenges in Sand Casting
Despite its advantages, sand casting is not without challenges. The process can be time-consuming, especially when creating complex molds. Additionally, achieving high precision can be tricky, and factors such as sand quality and temperature variations during pouring can affect the final product’s integrity.
Furthermore, while the process allows for recycling sand, managing sand waste and maintaining environmentally friendly practices remain critical concerns.
Conclusion
Industrial sand casting is a robust and adaptable manufacturing technique with a rich history and a wide range of applications. Its ability to produce complex shapes, coupled with cost-effectiveness and recyclable materials, makes it an essential part of modern manufacturing. However, addressing challenges associated with precision and environmental impact will be crucial for its continued success and relevance in the evolving industrial landscape.
Post time:டிசம்பர் . 11, 2024 03:34
Next:Understanding the Basics and Process of Sand Casting in Metalworking Techniques