Understanding Foundry Sand Types A Key Element in Metal Casting
Sand casting is one of the oldest and most widely used manufacturing processes in the metalworking industry. The quality of a cast product largely depends on the type of sand used in the molding process. Foundry sand is a crucial component, influencing the outcome of casting procedures, and today we will explore the various types of foundry sand and their characteristics.
1. Silica Sand
Silica sand is the most commonly used foundry sand due to its availability and excellent properties. Composed mainly of silicon dioxide (SiO2), silica sand can withstand high temperatures, making it ideal for casting ferrous and non-ferrous metals. It has good flowability, allowing for detailed mold-making, and provides a smooth surface finish to the castings. There are two types of silica sand used green sand and resin-bonded sand. Green sand is a mixture of silica sand, clay, and water, whereas resin-bonded sand employs a resin binder that gives stronger molds but has a different set of properties.
2. Green Sand
Green sand is a traditional molding sand composed of silica sand, clay, and a small amount of water. The clay serves as a binder that holds the sand grains together, allowing it to retain moisture. This type of sand is particularly favored for its reusability and cost-effectiveness. It facilitates the creation of complex shapes and delivers good surface quality. However, because of the water content, it can lead to casting defects if not controlled properly.
foundry sand types
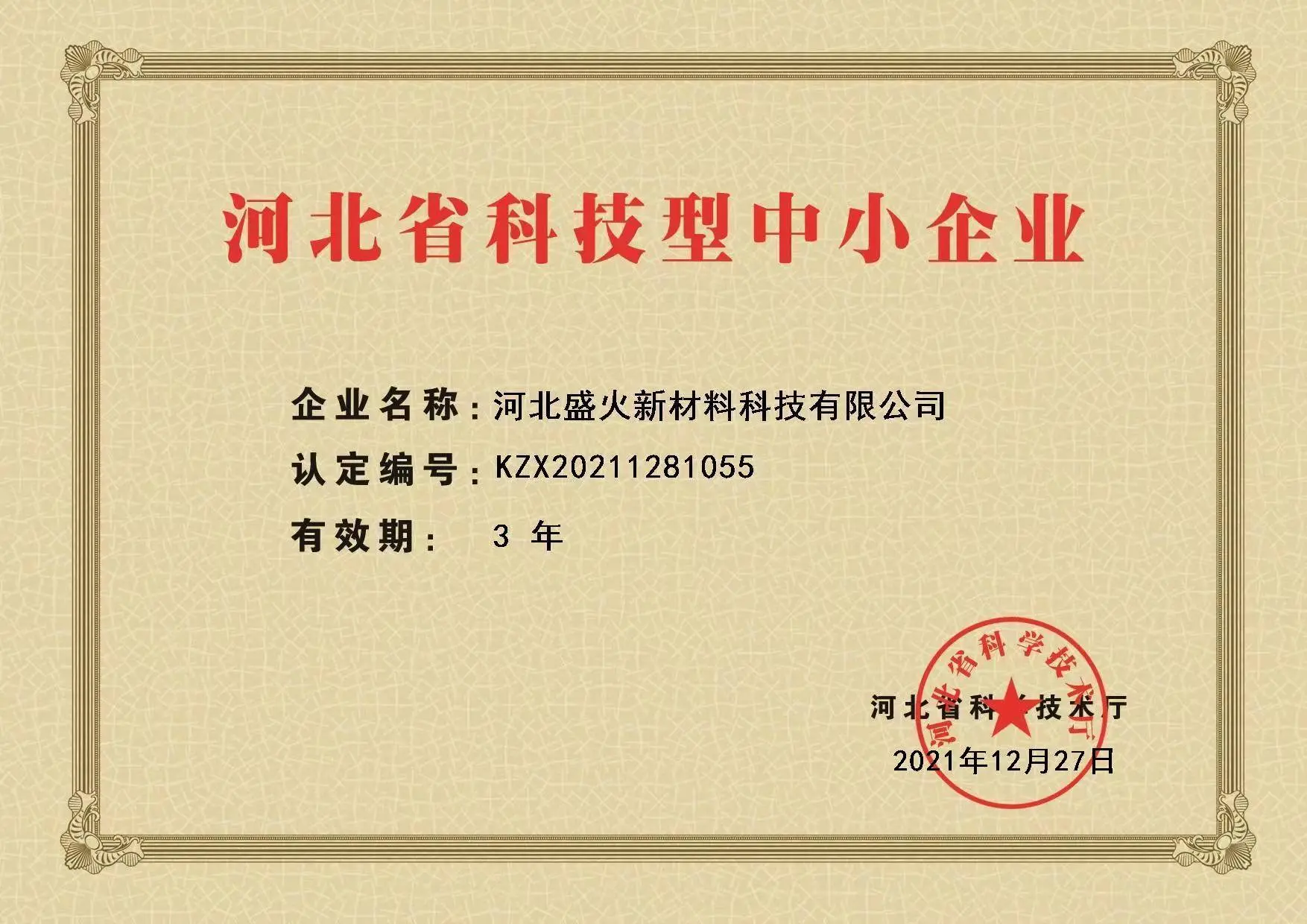
Resin-bonded sand is an advanced molding sand that uses synthetic resins as a binder. This type of sand offers high strength and superior mold integrity compared to traditional green sand. The key advantage of using resin-bonded sand is its ability to create finer details and achieve better surface finishes. This sand is typically utilized in applications that require more precision and less porosity, such as the aerospace and automotive industries. However, the cost of resin bonding is generally higher, making it less attractive for large-scale productions.
4. Clay-Based Sand
Another important type of foundry sand is clay-based sand. Usually found in the molding process, it consists of a combination of silica sand and clay. Its plasticity and ability to retain shape make it beneficial for producing intricate and detailed molds. The amount and type of clay used can greatly influence the properties of the final mold, including its strength and thermal stability. While effective, its use is becoming less common than resin-bonded options due to advancements in molding technology.
5. Chromite Sand
Chromite sand, made from chromium oxide, is another specialized foundry sand used primarily in the casting of steel and iron. It has a high melting point and excellent thermal stability, making it ideal for high-temperature applications. Chromite sand provides good dimensional stability and reduces core cracking during casting. However, its cost can be prohibitive, limiting its use to specialized applications where performance justifies the expense.
Conclusion
In summary, the type of foundry sand selected plays a pivotal role in shaping the casting process and the quality of the final product. From traditional silica and green sands to modern resin-bonded and specialized chromite sands, each sand type offers unique advantages and is chosen based on the specific requirements of the casting application. As technology continues to evolve, understanding these sand types will remain essential for foundry professionals striving for efficiency and precision in metal casting. With the right choice of foundry sand, manufacturers can achieve optimal results, reducing defects and enhancing the overall quality of castings.
Post time:அக் . 18, 2024 09:05
Next:simply sands ceramics