Understanding Foundry Sand Specifications
Foundry sand plays a crucial role in the metal casting process, serving as a mold material that helps shape and support molten metal as it solidifies. The effectiveness and efficiency of this process rely heavily on the specifications of foundry sand, which includes its composition, physical properties, and performance characteristics. In this article, we will explore the key specifications of foundry sand and their importance in achieving high-quality castings.
Composition of Foundry Sand
Foundry sand is primarily composed of silica (SiO2), which is abundant and inexpensive. The most commonly used type of foundry sand is silicate sand, known for its excellent thermal properties and ability to withstand high temperatures without breaking down. While silica is the main component, additives like clay, water, and various bonding agents can be included to enhance certain characteristics of the sand.
In most applications, the composition of foundry sand must comply with relevant industry standards. For example, the American Foundry Society (AFS) provides detailed guidelines on the acceptable levels of impurities, grain size, and other critical factors that ensure the sand meets performance criteria for specific casting processes.
Physical Properties
The physical properties of foundry sand are vital in determining its usability. Key properties include grain size, shape, distribution, and permeability.
1. Grain Size and Distribution The grain size of foundry sand has a direct impact on mold strength and surface finish of the castings. A finer grain size typically provides a smoother surface but may require more binder material, while coarser grains enhance strength but can lead to rough surfaces. The ideal grain size often falls between 0.2 mm to 0.7 mm, depending on the specific type of casting being produced.
2. Grain Shape The shape of the sand grains can affect flowability and packing density. Angular and sub-angular grains interlock better, providing increased strength, while round grains flow easily, which aids in mold filling but may compromise strength.
foundry sand specifications
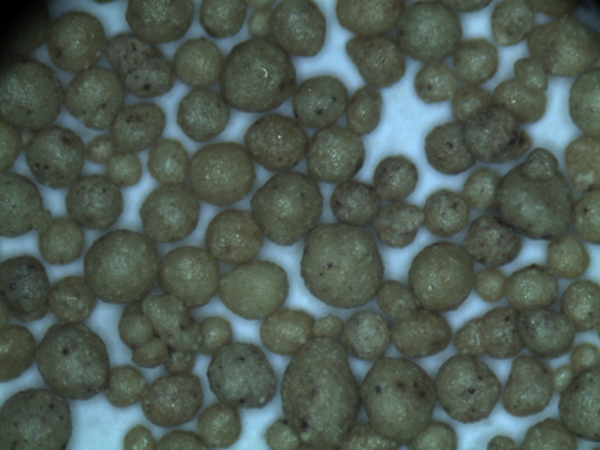
3. Permeability Permeability relates to the ability of gas to pass through the sand mold. Adequate permeability is essential to prevent gas entrapment during the pouring of molten metal, which can lead to defects in the casting. Foundry sands typically need a permeability range of 50 to 200 AFS units for efficient performance.
Performance Characteristics
In addition to composition and physical properties, the performance characteristics of foundry sand are critical to the casting process. These characteristics include
1. Reusability Foundry sand is often reused multiple times in casting processes. The sand must maintain its properties and performance over several cycles. Therefore, its durability and resistance to degradation are essential for cost-effectiveness.
2. Moisture Content The moisture level in foundry sand is another important parameter. Proper moisture content enhances the cohesion of the sand mixture and helps achieve the desired mold strength and finish. Too much or too little moisture can lead to casting defects.
3. Thermal Stability Foundry sand must withstand the high temperatures associated with molten metal without experiencing significant thermal expansion or degradation. The ability to retain structural integrity under thermal stress is vital to the quality of the resultant casting.
Conclusion
Understanding foundry sand specifications is essential for ensuring optimal performance in the metal casting process. Foundry sand should have a precise composition, favorable physical properties, and robust performance characteristics to achieve high-quality castings consistently. Various standards and guidelines, such as those set by the American Foundry Society, aim to ensure that foundry sand meets these essential criteria.
By carefully selecting and managing foundry sand according to its specifications, foundries can improve casting quality, reduce defects, and enhance overall productivity. As the metalworking industry continues to evolve, ongoing research and development in foundry sand technology will play a significant role in achieving even greater efficiencies and innovations in metal casting practices. Understanding these specifications is not only about following standards but also about pushing the boundaries of manufacturing excellence.
Post time:டிசம்பர் . 05, 2024 01:53
Next:Understanding the Process and Techniques of Sand Casting in Metalworking