Foundry Sand Composition Key Elements and Their Significance
Foundry sand is a critical material used in metal casting processes, where molten metal is poured into molds made from sand. The composition of foundry sand plays a vital role in determining the quality and performance of the final cast product. Understanding the elements that constitute foundry sand and their respective contributions is essential for optimizing casting processes, improving product quality, and reducing manufacturing costs.
Primary Components of Foundry Sand
The primary component of foundry sand is silica (SiO2), which typically constitutes about 90-95% of the composition. Silica is favored for several reasons it has a high melting point, excellent thermal stability, and good resistance to thermal shock. This makes silica sand suitable for molding and core-making applications in various metal casting processes, including iron, aluminum, and steel castings.
In addition to silica, foundry sand may contain other components that enhance its properties. For example, clay is often added to improve the binding capabilities of the sand. Clay acts as a binder that helps retain the sand's structure during the molding process. A common type of clay used in foundry applications is bentonite, which provides excellent cohesion and plasticity, enabling the creation of detailed molds. Typically, clay content in foundry sand ranges from 3% to 10%.
Another important addition to the composition of foundry sand is water, which is used to activate the clay's binding properties. The moisture content of molding sand can vary significantly, but an optimal range is usually between 3% and 5%. The proper moisture level is essential for achieving the desired strength and flexibility of the mold.
Additives and Their Functions
foundry sand composition
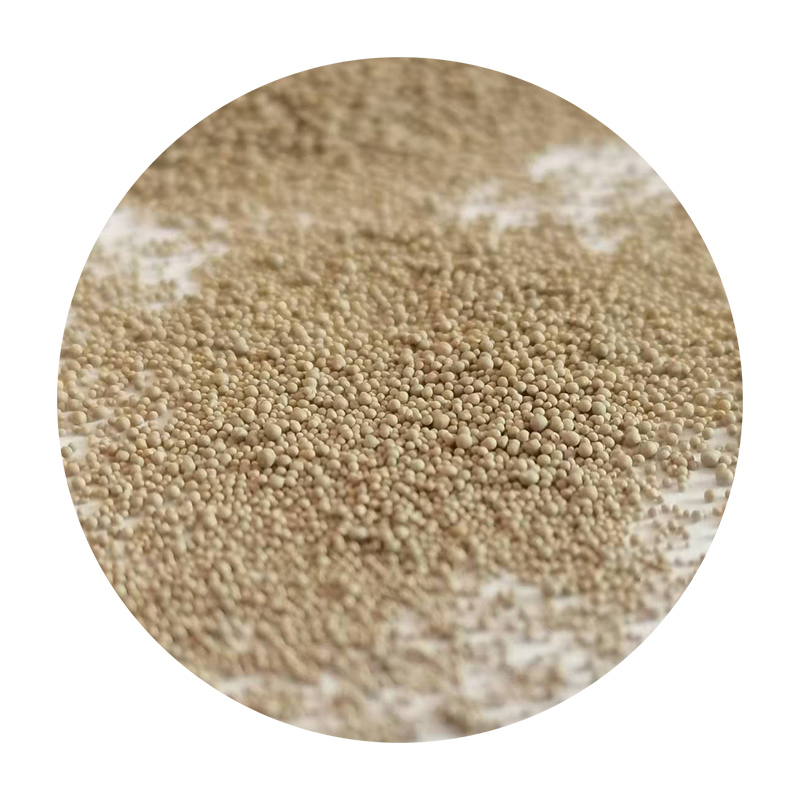
To further enhance the properties of foundry sand, various additives can be incorporated into the mixture. These might include organic materials, chemical hardeners, or special coatings. For instance, coal dust or other carbonaceous materials may be added to improve surface finish and reduce the oxidation of molten metal. Moreover, phenolic resins can be applied as binders to create chemically bonded sand molds, which can withstand higher pouring temperatures and reduce gas defects.
In some cases, foundry sands are coated with synthetic materials or resins to enhance specific characteristics such as thermal resistance, reduce moisture absorption, and improve mold release properties. These coatings play a crucial role in achieving superior surface finishes on cast products.
Environmental Considerations
As the foundry industry faces increasing scrutiny regarding environmental sustainability, the composition of foundry sand is also noteworthy from an ecological perspective. Traditional foundry sand is sourced from natural silica deposits, which raises concerns over resource depletion and habitat disruption. To mitigate these impacts, many foundries are turning to recycled foundry sand, which comes from previously used molds and cores. This not only reduces waste but also lowers material costs.
However, the recycling process requires careful management to ensure that the recycled sand maintains the necessary quality and performance characteristics. The chemical composition of recycled sand can differ from new sand, which necessitates adjustments in formulation and process parameters.
Conclusion
Understanding the composition of foundry sand—its primary ingredients, additives, and environmental implications—is essential for improving casting quality and operational efficiency. By optimizing the mixture of silica, clay, and moisture, along with strategic use of additives, foundries can enhance the performance of their molds and cores. Moreover, with a growing focus on sustainability, the industry is adapting by exploring recycled sand options, reducing waste, and conserving natural resources. The evolving landscape of foundry sand composition illustrates the balancing act between quality, performance, and environmental responsibility in modern metal casting practices.
Post time:நவ் . 27, 2024 20:44
Next:Exploring the Benefits and Techniques of Precision Sand Casting in Manufacturing Processes