Facing Sand in Foundry A Critical Component in Metal Casting
In the realm of metal casting, the importance of mold materials cannot be overstated. Among these, facing sand plays a pivotal role. This specialized type of sand is crucial in producing high-quality castings, influencing surface finish, and ensuring the integrity of the final product. Understanding the characteristics, applications, and advantages of facing sand is essential for anyone involved in foundry operations.
What is Facing Sand?
Facing sand is a specific type of sand used in the outer layer of the mold that directly interacts with the molten metal. Unlike the core sand, which is used for the internal structure of the mold, facing sand is designed to provide a smooth surface finish to the casting and to withstand the intense temperatures of molten metal during the pouring process. Typically, facing sand is made from fine grains of silica or other materials that can absorb heat and maintain structural integrity under high temperatures.
Properties of Facing Sand
Facing sand must possess several key properties to function effectively. First and foremost, it must have a high resistance to thermal shock. When molten metal is poured into a mold, temperatures can soar to over 1,500°C (2,732°F). If the sand cannot withstand these conditions, it may degrade, leading to defects in the casting.
Additionally, facing sand should exhibit good refractoriness, allowing it to maintain its shape and not melt or deform under heat. The sand should also have excellent cohesion and permeability. Cohesion ensures that the sand particles stick together, preventing erosion during the pouring of molten metal. Permeability, on the other hand, allows gases to escape from the mold during casting, reducing the risk of defects such as blowholes.
Applications of Facing Sand
facing sand in foundry
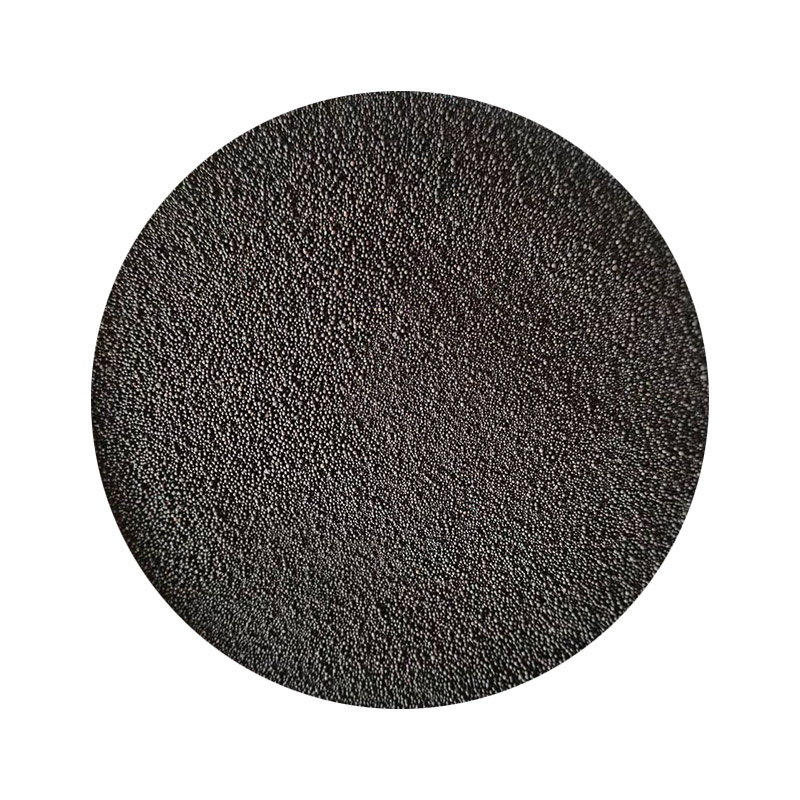
In foundry operations, facing sand is applied in various casting methods, including sand casting, investment casting, and shell molding. In sand casting, the mold is often made of two halves, and the facing sand is placed on the mold surface to provide the desired finish. Investment casting, which involves creating a pattern coated in a ceramic shell, also utilizes facing sand for its outer layer to ensure fine details and smooth surfaces.
Moreover, different alloys may require specific types of facing sand to optimize the casting process. For instance, cast iron, aluminum, and copper alloys all have different thermal properties and rates of expansion; thus, the appropriate facing sand can enhance the casting's overall quality.
Advantages of Using Facing Sand
One of the major advantages of using facing sand is the enhanced surface quality it provides. Smooth surfaces on castings lead to better aesthetic appeal and reduce the need for extensive finishing processes. This can significantly decrease production costs and time.
Additionally, effective use of facing sand can minimize defects such as casting porosity and inclusions, which can compromise the integrity of the final product. By selecting the appropriate type of facing sand, foundries can improve yield rates and reduce the amount of scrap material produced.
Conclusion
In conclusion, facing sand is a crucial element in the foundry process that directly impacts the quality and efficiency of metal casting operations. By understanding its properties, applications, and advantages, foundries can optimize their casting processes, resulting in superior products with reduced costs. As technology advances and the demands for high-quality castings increase, the role of facing sand will continue to be integral in achieving excellence in metal casting.
Post time:டிசம்பர் . 20, 2024 21:16
Next:resin coated sand specification