Coated Sand Casting An Innovative Approach to Metal Casting
Coated sand casting is a sophisticated method in the foundry industry that enhances the traditional sand casting process. It integrates the use of a coating material with sand to improve the properties of molds and cores, leading to superior cast quality and efficiency. This article delves into the intricacies of coated sand casting, its advantages, applications, and future potential.
The Basics of Sand Casting
Sand casting is one of the oldest and most widely used metal casting processes. It involves creating a mold by packing sand around a pattern, which is then removed to create a cavity in the shape of the desired object. Liquid metal is poured into this cavity, solidifying to form the final product. While effective, traditional sand casting can lead to challenges like surface roughness, mold collapse, and variable dimensional accuracy.
Introduction to Coated Sand
Coated sand casting addresses many of these issues by using sand particles that are coated with a thin layer of resin or other binding materials. The coating improves the resilience of the sand, enhancing the mold's integrity and surface quality. The most common coating materials include phenolic resin, furan resin, and a variety of thermosetting plastics that provide better adhesion and thermal resistance.
Advantages of Coated Sand Casting
1. Improved Surface Finish One of the primary benefits of coated sand is the significant improvement in surface finish. The smooth coating allows the metal to flow more uniformly, thereby reducing defects and surface irregularities.
2. Enhanced Strength The coated sand molds exhibit greater strength and stability, allowing for intricate designs and thinner walls in cast components. This strength reduces the likelihood of mold breakage during metal pouring and cooling.
3. Better Dimensional Accuracy Coated sand casting helps achieve tighter tolerances, facilitating the production of parts that require exact specifications. This feature is particularly beneficial in industries where precision is paramount, such as aerospace and automotive manufacturing.
coated sand casting
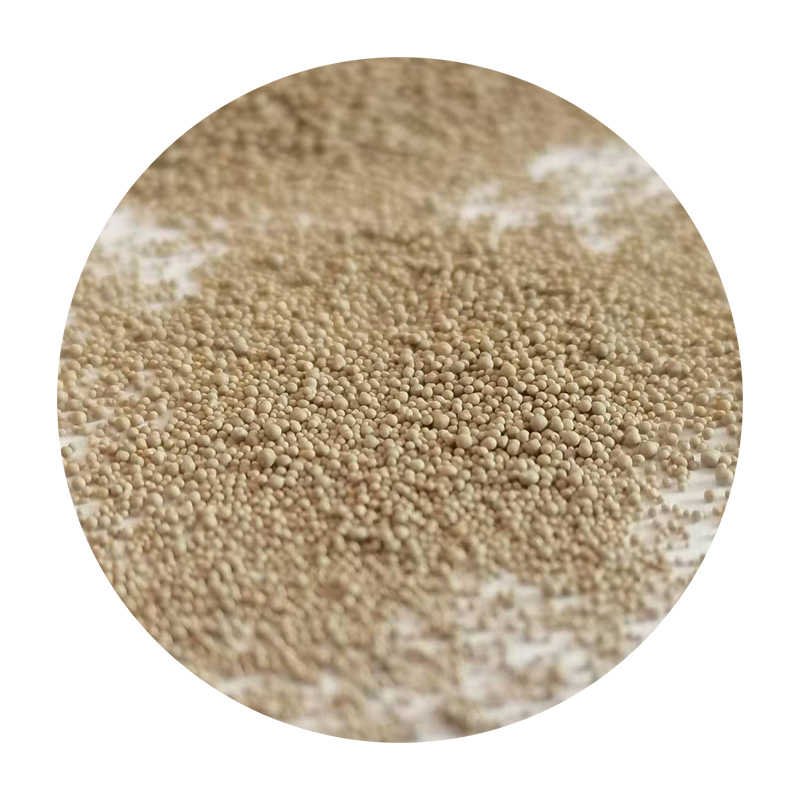
4. Reduced Casting Defects The use of coated sand minimizes issues like sand adherence and metal penetration, resulting in fewer casting defects. This leads to a higher yield of usable parts and less waste.
5. Environmental Benefits Coated sand can be reused multiple times, making it an environmentally friendly option compared to traditional sand casting. The reduction in waste and energy consumption aligns with sustainability goals in manufacturing.
Applications of Coated Sand Casting
Coated sand casting is utilized across various sectors due to its versatility. It is widely employed in the automotive industry for producing engine blocks, cylinder heads, and transmission cases. Additionally, it is used in the manufacturing of machinery components, marine parts, and even artistic sculptures. The method is suitable for both ferrous and non-ferrous metals, including aluminum, steel, and copper alloys.
Challenges and Considerations
Despite its numerous advantages, coated sand casting is not without challenges. The initial cost of coated sand materials can be higher than traditional sand, and the process may require specialized equipment and training. Furthermore, the choice of coating and sand type must be optimized for each specific application, necessitating thorough research and development.
The Future of Coated Sand Casting
As industries continue to evolve, coated sand casting is likely to gain more traction. With advancements in materials science and technology, the development of new resin systems and sand compositions may further enhance the process. Innovations in additive manufacturing can also complement coated sand techniques, allowing for new design possibilities and efficiencies.
In conclusion, coated sand casting represents a significant advancement in the field of metal casting. Its ability to produce high-quality, precise components more sustainably positions it as a preferred choice in various manufacturing sectors. As the industry embraces technological innovation, the future of coated sand casting looks promising, with potential for greater efficiency, quality, and environmental responsibility.
Post time:நவ் . 20, 2024 00:04
Next:الرملي الراتنج الصب