The Rise of 3D Sand Printing in Casting Applications
In recent years, 3D sand printing has emerged as a revolutionary technology in the field of casting, fundamentally changing the way components are produced across various industries. This innovative approach allows for the creation of intricate mold designs that traditional casting methods struggle to achieve. As the demand for customization, complexity, and efficiency in manufacturing continues to rise, 3D sand printing stands out as a groundbreaking solution.
3D sand printing technology involves the use of a digital design file to create a mold layer by layer from sand. The process begins with a computer-aided design (CAD) model, which is then transformed into a printable file. A specialized printer selectively binds sand grains using a binding agent, building up the mold in a series of layers. This method not only accelerates the prototyping phase but also minimizes the time taken to produce final products.
The Rise of 3D Sand Printing in Casting Applications
Another major benefit of this technology is the reduction of material waste. Traditional casting methods often involve excess material that must be machined away, leading to increased costs and environmental impact. In contrast, 3D sand printing uses only the amount of sand necessary for the mold, resulting in a more sustainable manufacturing process. This is particularly important in an era where many industries are striving to reduce their environmental footprints.
3d sand printing casting
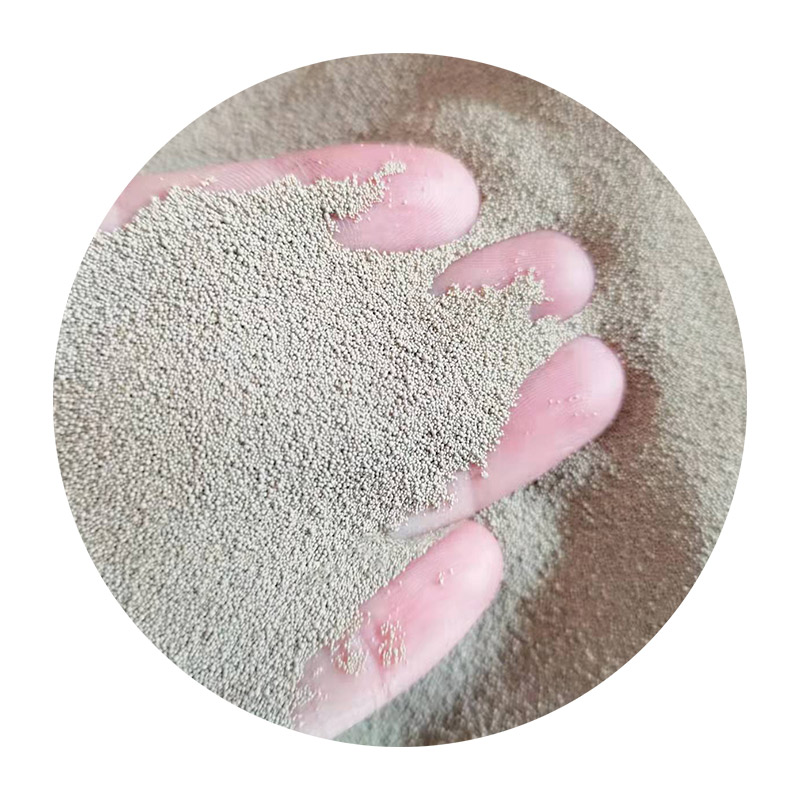
The applications of 3D sand printing extend beyond prototyping and mold creation. The technology is increasingly being adopted for low-volume production runs and even for the production of unique, one-off parts. Industries such as art, architecture, and jewelry design are beginning to explore the aesthetic possibilities offered by 3D sand printing, leading to a fusion of technology and creativity. This versatility has the potential to revolutionize the way artisans and designers produce their work, blending craftsmanship with modern manufacturing techniques.
Moreover, 3D sand printing can significantly shorten lead times, enabling faster delivery of parts to customers. In industries where time-to-market is crucial, this rapid production capability can provide companies with a significant competitive edge. The ability to quickly adapt designs and produce molds based on customer feedback also fosters a more agile manufacturing environment.
Despite its advantages, there are challenges that the technology must overcome. For instance, the initial investment in 3D sand printing equipment can be high. Additionally, the ongoing development of material science is necessary to enhance the properties of printed molds, especially for high-temperature applications. As research continues and technology advances, these hurdles are expected to diminish.
In conclusion, 3D sand printing has opened new avenues for casting processes across various industries. Its ability to produce complex designs, reduce material waste, and facilitate rapid prototyping makes it a game-changing technology in manufacturing. As the industry continues to evolve, the integration of 3D sand printing into casting applications will likely drive innovation, create new possibilities for customization, and enhance overall efficiency in production. With its broad spectrum of applications and advantages, 3D sand printing is set to play a pivotal role in the future of manufacturing.
Post time:டிசம்பர் . 07, 2024 16:34
Next:sand casting technology