Why Is Sand Casting Used?
Sand casting, one of the oldest and most versatile methods of metal casting, has been a cornerstone of manufacturing for centuries. This technique involves creating a mold from sand mixed with a bonding agent to shape molten metal into a desired object. The popularity and continued use of sand casting can be attributed to several key factors, making it the method of choice for various applications across different industries.
Cost-Effectiveness
One of the primary reasons sand casting is widely used is its cost-effectiveness. The materials required for sand casting are relatively inexpensive. Sand, which is the primary material, is abundant and can be reused multiple times. The bonding agents mixed with the sand, such as clay, also contribute to low production costs. In contrast to other casting processes that may require high-grade metals or more sophisticated equipment, sand casting offers a budget-friendly alternative for producing complex shapes.
Versatility in Design
Sand casting allows for a high degree of versatility in design. The sand molds can be created in virtually any shape and size, accommodating a wide range of products, from small intricate parts to large heavy components. This flexibility is especially beneficial for industries that require custom parts or prototypes. The ability to modify the mold design easily allows manufacturers to make quick adjustments, which is invaluable when developing new products or when needing to meet specific client requirements.
Ability to Handle Large Parts
Another advantage of sand casting is its capability to handle large parts. Industries such as automotive, marine, and construction frequently require large components, such as engine blocks or large structural parts. Sand casting can produce these large components without compromising on the quality of the casting. The process enables the creation of substantial metal parts in one piece, which often simplifies the assembly process and enhances the structural integrity of the product.
why is sand casting used
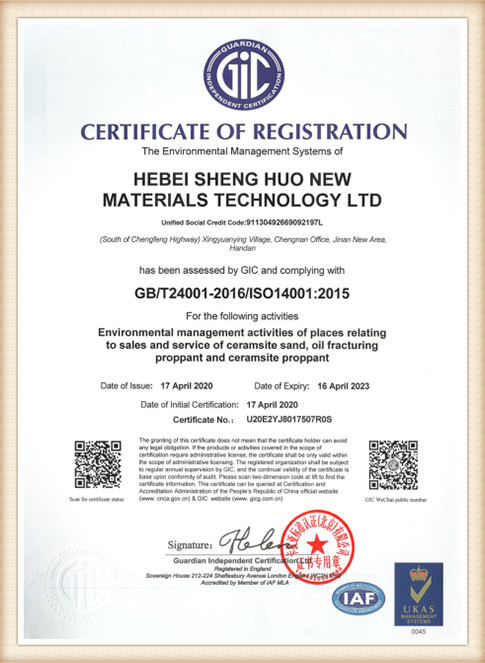
Excellent Surface Finish and Detail
While sand casting might not always offer the finest surface finish compared to other casting methods like die casting, advancements in techniques and materials have significantly improved the surface quality. With proper mold preparation and post-casting processes, high levels of detail and acceptable surface finishes can be achieved. The use of modern sand types and binder systems can also enhance the surface finish, making it suitable for applications where aesthetics are essential.
High Temperature Resistance
Metal casting requires materials capable of withstanding high temperatures, and sand casting excels in this area. The sand used in the casting process can resist high temperatures without degrading, making it suitable for various metals including aluminum, bronze, and iron. This characteristic enables manufacturers to use sand casting for applications that involve extreme heat and mechanical stress, adding to the method's appeal.
Environmental Benefits
In an era where sustainability and environmental responsibility are increasingly prioritized, sand casting presents several advantages. The materials used, primarily sand, are typically non-toxic and can often be recycled. The reusability of sand reduces waste and minimizes the need for new materials, aligning with eco-friendly practices. Additionally, the lower energy requirements of the sand casting process compared to other forms of metal casting decrease its overall carbon footprint.
Conclusion
In summary, sand casting remains a popular choice in the metal manufacturing industry for numerous compelling reasons. Its cost-effectiveness, versatility, ability to handle large parts, and efficiency in producing complex shapes make it an attractive option for many applications. Sand casting also benefits from excellent temperature resistance and environmental sustainability, addressing modern concerns about efficiency and ecological impact. As technology continues to advance, the sand casting process is likely to evolve further, maintaining its relevance and dominance in the manufacturing world. Whether for large-scale production or custom components, sand casting stands out as a reliable and efficient method for crafting quality metal products.
Post time:Oktoba . 22, 2024 06:02
Next:materials used in sand casting