Sand casting is a widely used manufacturing process for producing complex metal parts. This technique involves pouring molten metal into a mold formed by sand, making the type of sand used critical to the success of the casting process. The characteristics of the sand directly influence the quality of the casting, the surface finish, and the overall dimensional accuracy of the final product.
The most common type of sand used in sand casting is silica sand. Silica, composed primarily of silicon dioxide (SiO2), is abundant, inexpensive, and possesses a high melting point, making it suitable for mold making. The grain size of the silica sand can vary, typically ranging from fine to coarse. Finer sands tend to provide better detail in the castings due to their ability to capture intricate details of the mold design, while coarser sands can produce stronger molds that are better suited for large castings.
In addition to silica sand, other types of sand and additives are also used to enhance the properties of the sand mold. For instance, olivine sand, which is composed of magnesium iron silicate, is known for its high thermal stability and resistance to thermal shock. This makes olivine sand an excellent choice for high-temperature applications, leading to a longer lifespan and better performance of molds.
Another important additive is bentonite clay, which is often mixed with the sand to improve its binding properties. Bentonite helps the sand grains stick together, providing the mold with greater strength and durability, which is essential during the pouring of the molten metal. The addition of water activates the bentonite clay, creating a pliable mixture that can hold the shape of the mold under pressure.
what type of sand is used in sand casting
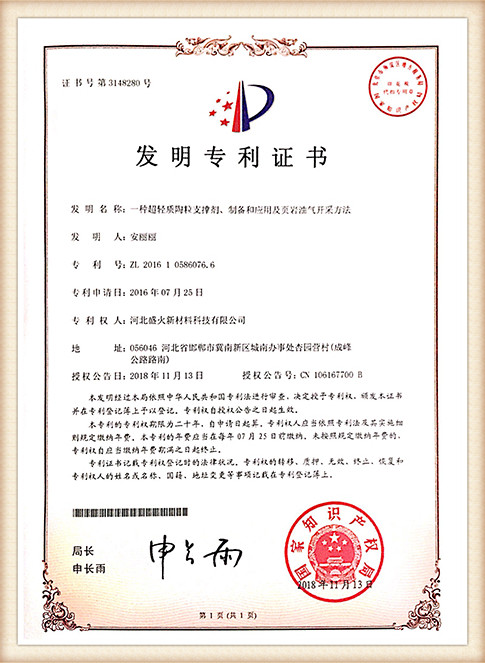
Moreover, to enhance the surface finish of the castings, phenolic resins or other synthetic binders can be used instead of traditional clay-bonded sands. These synthetic sands often lead to smoother surface finishes and are particularly advantageous in applications where surface quality is a priority.
The characteristics of the chosen sand can also affect the cooling rate of the metal. Sands with high thermal conductivity allow for faster cooling, which can alter the microstructure of the cast metal, affecting its strength and hardness. This factor is particularly critical in applications where specific mechanical properties are required.
In summary, the type of sand used in sand casting plays an integral role in determining the quality and properties of the final product. Silica sand, while being the most common choice, may be supplemented with various additives such as bentonite clay or synthetic resins to improve mold performance and casting quality. Understanding the nuances of different sands and their properties is essential for manufacturers aiming to optimize their casting processes and produce high-quality metal components.
Post time:Novemba . 24, 2024 17:25
Next:Innovative Applications and Examples of Sand Casting in Various Industries