Steps in Sand Casting A Comprehensive Guide
Sand casting, a widely used manufacturing process, plays a pivotal role in producing metal parts from various materials. This technique offers significant advantages, such as cost-effectiveness and versatility in material selection, which makes it a popular choice across multiple industries. Understanding the steps involved in sand casting is essential for anyone looking to master this process.
1. Pattern Making
The first step in the sand casting process is creating a pattern. The pattern serves as a replica of the final product and is usually manufactured from materials like wood, metal, or plastic. Accuracy in the pattern is crucial, as it determines the dimensions of the final cast. Patterns can be made in various types, including solid, split, and match-plate patterns, depending on the complexity of the design.
It’s also important to incorporate allowances during pattern making, such as shrinkage allowance, machining allowance, and draft allowance, to ensure that the cast product meets the required specifications.
2
. Mold PreparationOnce the pattern is ready, the next step is preparing the mold. This involves creating a cavity in a mixture of sand, clay, and water, which replicates the shape of the pattern. The sand is compacted around the pattern to ensure that it retains its shape. There are two primary types of molds green sand molds (which are made using damp sand) and dry sand molds (which are prepared with dried sand).
Furthermore, the mold must include vents and gates to allow for the free flow of molten metal and the escape of gases during the pouring operation. Careful attention to these details can greatly influence the quality of the final product.
3. Melting and Pouring
steps in sand casting
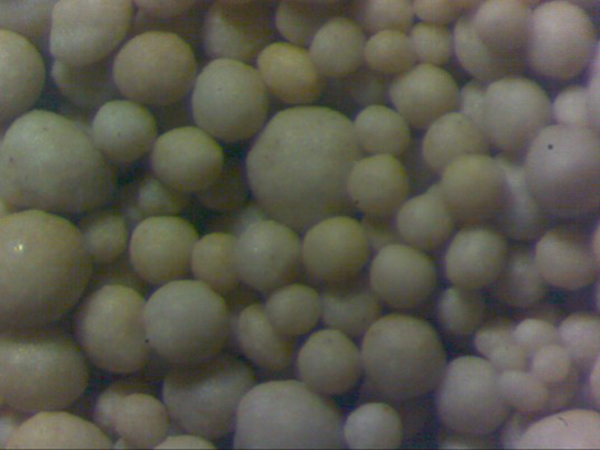
After the mold is prepared, the next step is melting the metal. This process involves heating the metal to its melting point in a furnace. The choice of metal depends on the desired properties of the final product, with common choices including aluminum, iron, and brass.
Once the metal is molten, it must be poured into the mold cavity. This stage requires precision and control, as the pouring temperature and speed can significantly affect the casting's outcome. The molten metal must fill the mold without creating turbulence, which can introduce defects such as air bubbles or inclusions.
4. Cooling and Solidification
After pouring, the molten metal is allowed to cool and solidify within the mold. The cooling rate can significantly impact the structural properties of the cast part. Typically, the metal will contract as it solidifies, and the time required for cooling can vary based on the size and complexity of the casting.
Proper cooling also prevents the formation of defects, such as cracks or warping. Once the metal is completely solidified, the mold can be broken apart to retrieve the cast part.
5. Finishing Processes
The final step in the sand casting process involves finishing the casting. This may include removing any excess material, known as flash, and smoothing out rough edges. Common finishing processes include sandblasting, machining, and polishing. These processes not only improve the appearance of the part but also ensure it meets the precise specifications required for its application.
Conclusion
Sand casting is a time-honored manufacturing technique that remains relevant due to its adaptability and effectiveness. By understanding the steps from pattern making to finishing, manufacturers can produce high-quality castings that meet their needs. Whether used in automotive, aerospace, or artistic applications, mastering the intricacies of sand casting opens doors to a wide array of possibilities in metal fabrication.
Post time:Oktoba . 20, 2024 07:37
Next:resin coated sand manufacturing process