Steps of Sand Casting
Sand casting is a widely used manufacturing process, ideal for producing complex shapes and large parts. It involves creating a mold from a sand mixture and then pouring molten metal into this mold to form the final product. Here, we will explore the essential steps involved in the sand casting process.
1. Pattern Making
The first step in sand casting is creating a pattern. A pattern is an exact replica of the final product, slightly oversized to account for shrinkage as the metal cools. Patterns can be made from various materials including wood, metal, or plastic. The complexity of the part dictates whether a solid pattern or a split pattern (two halves) will be used.
2. Preparing the Mold
Once the pattern is ready, the next step is to prepare the mold. This involves mixing sand with a binding agent such as clay and water to create a moldable material. The mixture is packed around the pattern to form a mold cavity. The sand needs to be tightly packed to ensure it can withstand the pressure of the molten metal. After packing, the mold is removed from the pattern, leaving a negative impression.
3. Core Making (if necessary)
For more complex shapes, cores may be used. Cores are additional sand molds placed within the main mold to create internal features or cavities. These are constructed separately and then inserted into the main mold before pouring in the metal.
4
. Melting the MetalIn the next step, the metal is melted in a furnace. This can be various metals, including iron, aluminum, or bronze, depending on the requirements of the final product. The molten metal should be poured at a specific temperature to ensure proper flow and filling of the mold cavity.
steps of sand casting
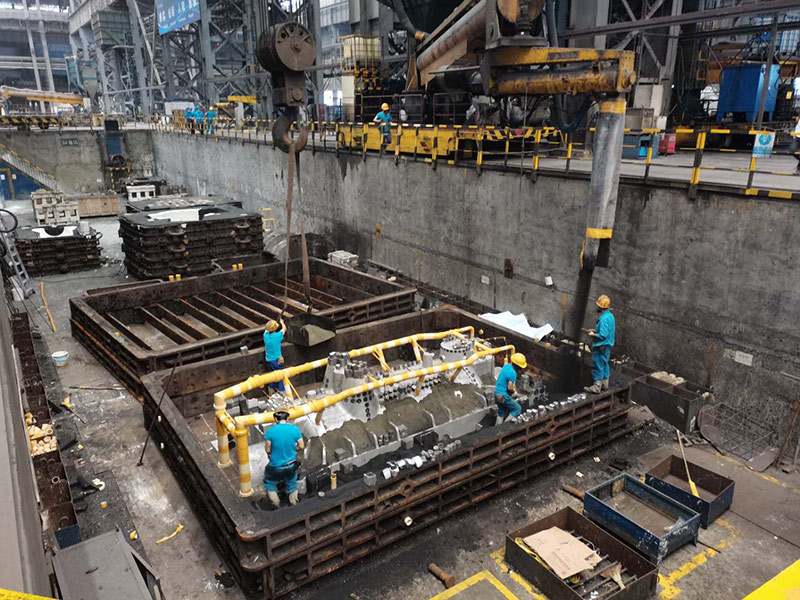
5. Pouring the Metal
Once the metal is molten and at the right temperature, it is poured into the mold. Care must be taken during this step to prevent defects such as porosity or turbulence, which can affect the quality of the final product. Pouring can be done manually or through automated systems for larger operations.
6. Cooling and Solidification
After pouring, the molten metal is left to cool and solidify. This time varies depending on the type of metal and the complexity of the mold. During this phase, the metal will shrink as it cools, hence the need for the initial pattern to be slightly oversized.
7. Removing the Casting
Once the metal has cooled and solidified, the mold is broken apart to reveal the casting. This step may involve shaking the mold or using vibrations to help separate the sand from the metal.
8. Finishing
Lastly, the casting undergoes various finishing processes such as grinding, sanding, or machining, to achieve the desired surface finish and dimensions.
Sand casting is a versatile and cost-effective method for producing metal parts, making it an essential technique in various industries, including automotive, aerospace, and art. The steps outlined above provide an overview of how this traditional process operates, showcasing its significance in manufacturing.
Post time:Septemba . 18, 2024 11:03
Next:모래를 주조하여 재활용하다