The Steel Sand Casting Process An Overview
The steel sand casting process is a time-honored manufacturing technique that has evolved over the years to meet the demands of various industries. This method, which uses sand as a mold material, allows for the production of complex shapes and sizes, making it a popular choice in sectors such as automotive, aerospace, and machinery.
What is Steel Sand Casting?
Steel sand casting involves creating a mold out of sand, typically mixed with clay and water, to hold molten steel. The process begins with crafting a pattern, usually made of metal or wood, that represents the desired final shape of the casting. Once the pattern is complete, it is placed in a sand mixture, which is compacted around it to form the mold. After the sand has hardened, the pattern is removed, leaving a cavity in the shape of the desired object.
The Step-by-Step Process
1. Pattern Preparation The first step in the sand casting process is creating a precise pattern of the part to be cast. This pattern should account for factors such as shrinkage and should have allowances for machining afterward.
2. Mold Making The prepared pattern is then used to create a mold. The pattern is pressed into a mixture of sand, clay, and water to form the sand mold. Two halves of the mold are typically created, known as the cope (top) and the drag (bottom).
3. Core Making (if necessary) For parts that require internal cavities, cores made of sand are produced and placed within the mold. These cores provide the necessary internal features of the final casting.
4. Mold Assembly Once the individual mold halves are prepared, they are assembled, ensuring proper alignment and sealing to prevent molten steel from leaking.
steel sand casting process
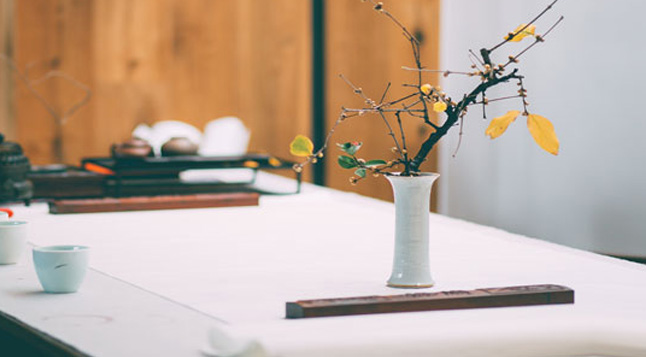
5. Melting the Steel The steel to be cast is melted in a furnace, reaching a temperature of around 1,500 degrees Celsius. It’s crucial to control the temperature precisely to ensure the quality of the molten steel.
6. Pouring The molten steel is carefully poured into the mold through a gating system. This must be done quickly to avoid premature solidification of the steel.
7. Cooling and Solidification After pouring, the steel begins to cool and solidify, taking on the shape of the mold. Cooling time varies depending on the thickness and complexity of the casting.
8. Mold Removal Once the steel has completely cooled, the sand mold is broken apart to reveal the cast part. This step can involve mechanical shaking or vibration to separate the mold without damaging the casting.
9. Finishing The final step involves cleaning, trimming, and machining the casting to achieve the desired specifications. This may include grinding, sanding, or milling to remove any excess material or imperfections.
Advantages of Steel Sand Casting
The steel sand casting process offers numerous advantages. It is cost-effective for producing large parts and allows for high levels of design flexibility. The sand molds can be reused multiple times, reducing waste and operational costs. Additionally, this method accommodates a wide variety of steel grades and alloys, making it suitable for diverse applications.
Conclusion
In conclusion, the steel sand casting process is an integral part of modern manufacturing, providing the means to create robust and complex components for a myriad of industries. Understanding this process not only highlights its importance but also opens the door to innovations in design and improvements in efficiency. As technology continues to advance, the steel sand casting process will undoubtedly keep evolving, remaining a reliable choice in the manufacturing realm.
Post time:Novemba . 10, 2024 18:06
Next:Exploring the Possibilities of Using Sand with Resin for Creative Projects