Steel Sand Casting An Overview
Steel sand casting is a widely used method in the manufacturing industry for producing intricate metal parts with high precision. This technique utilizes a mixture of sand and other materials as a mold, enabling the creation of complex shapes that might be difficult or costly to achieve through other means of production. The versatility and cost-effectiveness of steel sand casting make it an attractive option for various applications, ranging from automotive components to industrial machinery.
The Process of Steel Sand Casting
The process of sand casting involves several critical steps that ensure high-quality output. It begins with the creation of a pattern, a model of the desired part, which is typically made from a durable material such as metal, wood, or plastic. This pattern is used to form the mold cavity in the sand mixture, which consists primarily of silica sand, clay, and water. The sand's composition is crucial, as it must maintain sufficient strength to hold its shape yet be easily collapsible to allow for part removal.
Once the pattern is placed in the sand mixture, it is compacted to form the mold. After the mold is prepared, the pattern is removed, leaving a cavity that mirrors the shape of the desired part. The next step involves the melting of steel in a furnace, achieving temperatures typically exceeding 1,500 degrees Celsius (2,732 degrees Fahrenheit). The molten steel is then carefully poured into the mold cavity, allowing it to fill the space and take on the shape of the part.
After the molten steel has cooled and solidified, the mold is broken apart, and the casting is retrieved. The final steps of the process include trimming any excess material (known as flash) and performing additional finishing operations. These may involve machining, polishing, or applying surface treatments to achieve the desired dimensional accuracy and surface quality.
Advantages of Steel Sand Casting
Steel sand casting offers several advantages that contribute to its continued popularity in manufacturing. One of the most significant benefits is its ability to produce large and complex components that would be challenging to create with other processes like forging or machining. Because sand molds can easily be modified, manufacturers can quickly adapt to produce different parts without the need for expensive tooling changes.
steel sand casting
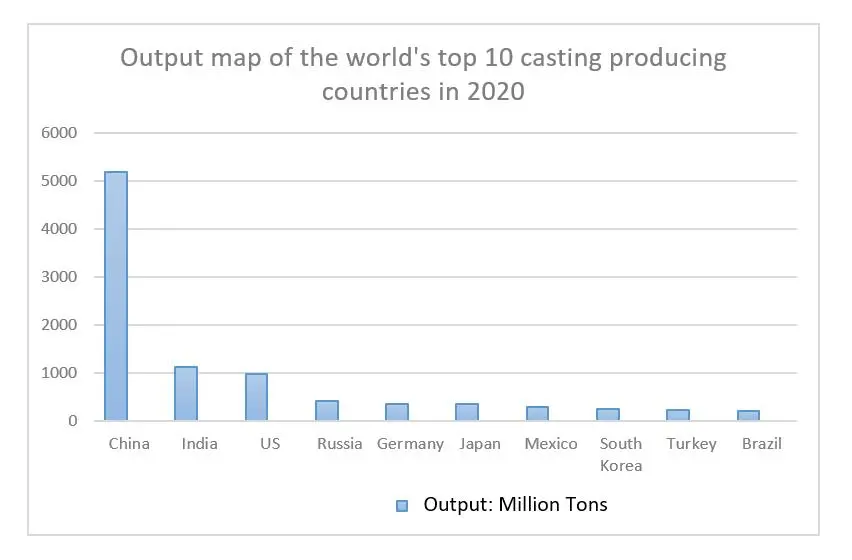
Moreover, steel sand casting is cost-effective for both short and long production runs. The materials required are relatively inexpensive, and the process allows for efficient production cycles. Additionally, sand casting is well-suited for producing parts with varying wall thicknesses, enabling the creation of lightweight yet durable components.
Another advantage of this method is its environmental sustainability. Sand molds can be reused multiple times, reducing waste. Advanced recycling techniques also allow for the recovery of spent sand, which can be reprocessed and used again, minimizing the environmental footprint of the casting operation.
Applications of Steel Sand Casting
The applications of steel sand casting are vast and diverse. In the automotive industry, components such as engine blocks, transmission housings, and suspension parts are frequently produced using this method. These parts require high-strength properties and precision, which steel sand casting provides effectively. Additionally, heavy machinery manufacturers utilize this method for creating parts like gears, frames, and other structural components.
Beyond automotive and machinery, steel sand casting is also employed in the construction industry for producing items such as scaffolding brackets and other load-bearing supports. The marine industry benefits from sand casting due to its ability to produce high-performance components that resist corrosion and provide durability in harsh environments.
Conclusion
In summary, steel sand casting is a critical manufacturing process that combines efficiency, versatility, and cost-effectiveness. Its ability to produce complex shapes and high-quality metal components makes it an essential technique across various industries. As technology and materials continue to evolve, the future of steel sand casting looks promising, offering potential advancements that may further enhance its application and efficiency. Manufacturers are likely to keep exploring this age-old yet highly reliable method to meet the demands of increasingly complex engineering challenges.
Post time:Desemba . 31, 2024 21:47
Next:Mật độ cát đúc và vai trò của nó trong quy trình sản xuất chế tạo.