The Role of Sand in Sand Casting An In-Depth Analysis
Sand casting, one of the oldest and most versatile metal casting processes, uses a mixture of sand and other materials to create molds into which molten metal is poured. The quality and properties of the sand used significantly influence the final product, making it essential to understand the different types of sand and their respective roles in the sand casting process.
Types of Sand Used in Sand Casting
The primary material in sand casting is silica sand, which consists mainly of silicon dioxide (SiO2). However, not all sands are created equal. The properties of the sand can vary based on its grain size, shape, and the presence of impurities.
1. Green Sand This is perhaps the most common type of sand used in casting. Green sand is a mixture of silica sand, clay, and moisture. The clay acts as a bonding agent, and the water provides workability. The name green refers to the fact that the sand is used in its moist state, which helps in forming molds. Green sand is flexible and can reproduce fine details, making it suitable for various applications.
2. Dry Sand Unlike green sand, dry sand is baked in an oven to remove moisture. This process provides a more rigid mold that is advantageous in producing dimensionally accurate castings. However, dry sand is less forgiving when it comes to the intricate details of a mold, often requiring precise model making.
3. Sodium Silicate Sand This type of sand uses sodium silicate as a binder. When exposed to carbon dioxide, the sodium silicate hardens, forming a robust mold. Sodium silicate sand is ideal for producing complex shapes and is beneficial for automated processes.
4. Plastic Sand This type includes sands that have been treated with special additives, enhancing their properties for specific casting requirements. Plastic sands exhibit good flowability and excellent surface finishes, making them suitable for high-quality castings.
Properties of Sand for Casting
sand used in sand casting
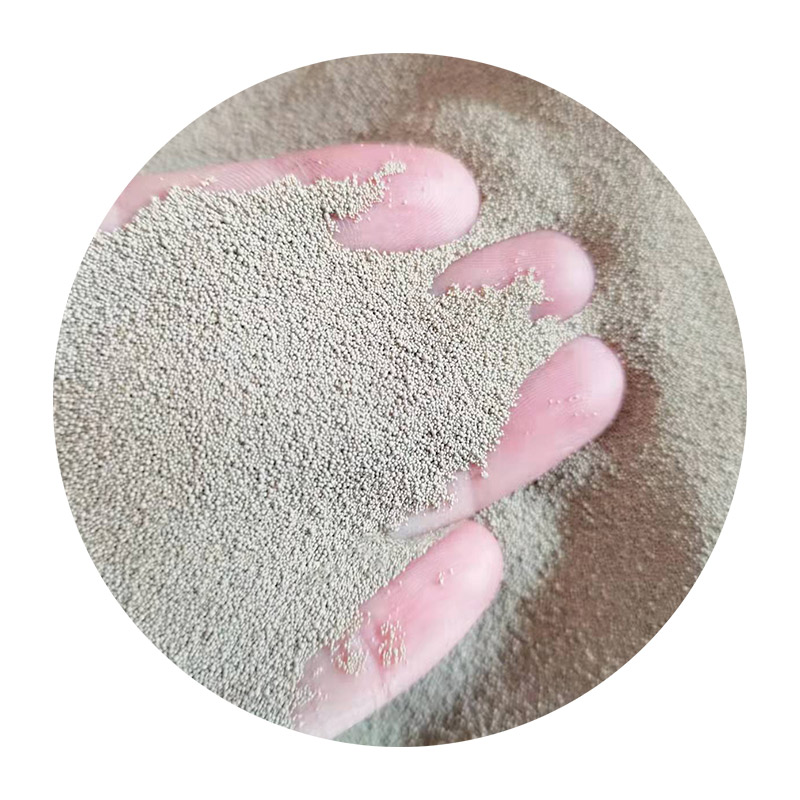
The effectiveness of sand in casting is determined by several key properties
- Grain Size and Shape The grain size of the sand particles affects the surface finish of the cast product. Finer sands can produce a smoother surface, while coarser sands may create a rough finish. The shape of the grains—whether angular, rounded, or sub-angular—also influences packing density and mold strength.
- Permeability This refers to the ability of the sand mold to allow gases to escape during the pouring of molten metal. Adequate permeability is crucial to prevent gas entrapment in the casting, which can lead to defects. A balance must be struck between sufficient permeability and mold strength.
- Bonding Strength This property helps to hold the sand grains together, maintaining the integrity of the mold during the casting process. The type and amount of binder used in the sand mixture play a critical role in determining its bonding strength.
- Thermal Stability Sand must withstand the extreme temperatures of molten metal without breaking down. High thermal stability prevents the mold from deforming and ensures dimensional accuracy in the final product.
Environmental Considerations
In recent years, the industry has become more aware of environmental issues related to sand casting. The extraction of silica sand has raised concerns about sustainability and ecological balance. As a result, researchers are exploring alternative materials, such as recycled foundry sands or organic binders, to reduce the environmental impact associated with traditional sand casting methods.
Conclusion
The type and quality of sand used in sand casting are critical for the success of the casting process. Understanding the properties of different sand types and how they interact with various metals can lead to improved quality and efficiency in manufacturing. With ongoing research into sustainable practices, the future of sand casting may involve innovative materials and techniques, ensuring that this ancient process continues to evolve in a modern context. As we strive for better performance and lower environmental impact, the role of sand in sand casting remains vital and ever-important in the world of metalworking.
Post time:Desemba . 30, 2024 19:21
Next:china sand casting