Sand Preparation in Foundry An Essential Process for Quality Casting
The foundry industry plays a vital role in manufacturing components across various sectors, from automotive to aerospace. One of the most crucial processes within this domain is sand preparation. High-quality sand preparation is fundamental to ensure the production of castings that meet stringent specifications and performance standards. This article discusses the significance of sand preparation, the processes involved, and its impact on the overall quality of castings.
Importance of Sand in Foundry Operations
Sand is the primary mold material in the foundry industry. It possesses excellent thermal properties and is readily available, making it the ideal choice for creating molds and cores. The performance of the sand directly influences the casting's surface finish, dimensional accuracy, and strength. Therefore, proper sand preparation is essential to enhance the foundry's production efficiency and the quality of the final product.
Sand Types and Their Characteristics
Different types of sand are used in foundries, each with specific properties that make them suitable for various applications. The most commonly used sand types include silica sand, green sand, and resin-coated sand.
1. Silica Sand Known for its high melting point and excellent flow characteristics, silica sand is often used in high-temperature applications. 2. Green Sand A mixture of sand, clay, and water, green sand is widely used due to its ease of use and ability to produce intricate shapes. It is reusable, making it cost-effective. 3. Resin-Coated Sand This type of sand is coated with a phenolic resin which binds the grains together when heated, offering superior surface finish and reducing the need for extensive post-casting cleaning.
The Sand Preparation Process
The sand preparation process involves several stages to ensure that the sand is in optimal condition for molding. These stages include
sand preparation in foundry
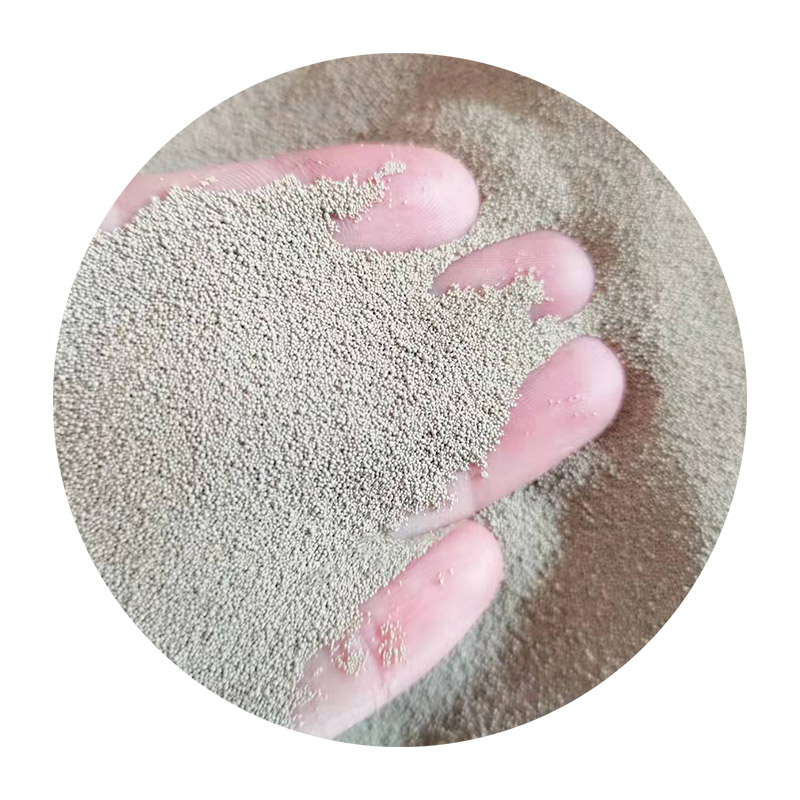
1. Sand Mixing The first step involves mixing the sand with additives, such as clay and water, to achieve the desired consistency and bonding properties. This process may vary based on the type of sand being used and the specific requirements of the casting.
2. Sand Conditioning This process is critical for enhancing the quality of the sand mixture. Sand conditioning may involve mechanical processes, such as milling and screening, to remove impurities and ensure uniform distribution of grain sizes.
3. Moisture Control Accurate moisture content is crucial for the molding process. Excess moisture can lead to defects in castings, such as porosity, while insufficient moisture can result in poor mold strength. Foundries often employ sophisticated moisture control systems to maintain the optimum level.
4. Reclamation After casting, used sand is usually reclaimed for reuse. Reclamation processes involve separating the sand from the metal and crushing any lumps. This practice is environmentally friendly and economically advantageous as it reduces the need for new sand.
5. Quality Testing Before the sand is used for casting, it undergoes rigorous quality testing. Parameters such as grain size distribution, moisture content, and strength are assessed to ensure the sand meets industry standards.
Impact on Casting Quality
Effective sand preparation has a significant impact on the quality of the final casting. Properly prepared sand leads to better moldability and reduces defects such as shrinkage, inclusions, and surface roughness. Consequently, this enhances the overall reliability and performance of the cast components.
In conclusion, sand preparation is a critical process in the foundry industry. The careful selection, mixing, conditioning, and testing of sand ensure the production of high-quality castings. As technology advances, the foundry industry continues to innovate in sand preparation techniques, leading to improved casting quality and efficiency. The importance of this process cannot be overstated, as it lays the foundation for successful foundry operations and contributes to the overall excellence of manufactured products.
Post time:Novemba . 06, 2024 17:19
Next:Exploring the Artistry and Techniques of Sand Casting in Modern Manufacturing