Sand Casting Tolerances Understanding and Implementation
Sand casting is one of the oldest and most versatile manufacturing processes used in the foundry industry. It is particularly favored for its ability to produce complex shapes and intricate designs that would be challenging to achieve with other manufacturing techniques. However, the quality and functionality of sand cast components are highly dependent on the tolerances maintained throughout the casting process. This article will explore the significance of tolerances in sand casting, the factors influencing them, and best practices for achieving optimal results.
What Are Tolerances in Sand Casting?
Tolerances refer to the permissible limits of variation in a physical dimension of a part. In the context of sand casting, tolerances are crucial in ensuring that the final product meets the specified design criteria and functions as intended. The standard tolerances for sand casting typically vary based on the complexity of the part, the size, and the specific metallurgical characteristics required. Generally, sand casting tolerances can range from ±0.25 to ±1.5 mm for most components, with tighter tolerances being achievable through further machining processes after casting.
Factors Influencing Tolerances
1. Pattern Design The design of the pattern used for molding significantly influences the final dimension of the cast. Patterns should account for shrinkage during the cooling process, as metals contract when solidifying.
2. Sand Quality The type and quality of sand used in the mold can impact the precision of the casting. For example, finer sand can produce a smoother surface finish, thus allowing for tighter tolerances.
3. Mold and Core Production The methods employed in mold making, including the use of core prints and the accuracy of mold dimensions, affect the dimensional accuracy of the final product. A well-constructed mold minimizes variations in the casting outcome.
4. Temperature Control Maintaining a consistent pouring temperature and cooling rate is vital. Inconsistent temperatures can lead to defects or irregularities, thus affecting dimensional integrity and tolerances.
5. Metal Type Different alloys and metals have different shrinkage rates, which can affect tolerances. It is essential to conduct thorough research on material properties to anticipate these variations.
sand casting tolerances
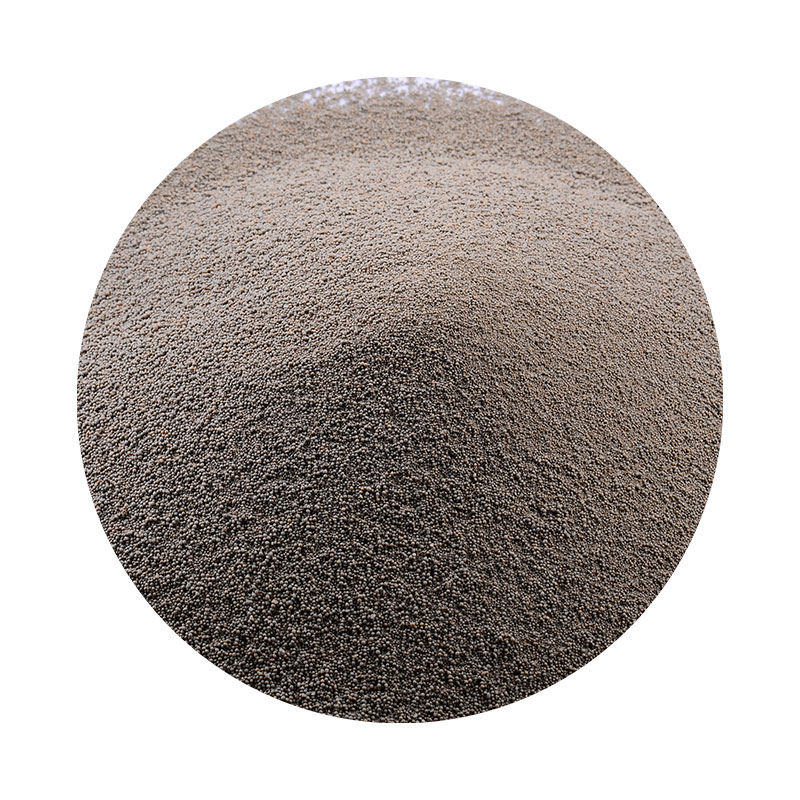
6. Casting Technique The technique employed during the pouring and solidification process can alter tolerances. Techniques like gravity pouring and pressure casting offer different levels of precision.
Achieving Optimal Tolerances
To achieve optimal tolerances in sand casting, several best practices can be followed
1. Design for Manufacturability Engage in design practices that facilitate easier casting. Simple shapes with gradual transitions are generally easier to cast accurately.
2. Precision Pattern Making Utilize high-quality materials in the creation of patterns and ensure they are manufactured to tight tolerances.
3. Control Process Variables Monitor and control variables such as temperature, sand composition, and curing times closely, as these can influence the consistency and quality of the produced parts.
4. Use of CNC Machining After the casting process, employing CNC (Computer Numerical Control) machining can help refine the dimensions of the cast components, allowing for tighter tolerances and enhanced surface finishes.
5. Testing and Inspection Regular quality inspections during and after the casting process are essential. Non-destructive testing methods can identify potential issues without compromising the integrity of the cast parts.
Conclusion
Understanding and implementing proper tolerances in sand casting is essential for producing quality components. By taking into account the various factors that influence tolerances and adopting best practices throughout the casting process, manufacturers can enhance the precision of their output. This ultimately leads to increased efficiency, better product performance, and improved customer satisfaction, positioning sand casting as a reliable solution in modern manufacturing landscapes.
Post time:Desemba . 11, 2024 00:26
Next:Exploring Techniques and Innovations in Sand Casting Processes for Improved Manufacturing Efficiency