The Sand Casting Process An Overview
Sand casting is one of the oldest and most versatile manufacturing processes, widely used to produce intricate metal parts and components. This method is characterized by its adaptability, cost-effectiveness, and ability to create complex shapes, making it popular in various industries, including automotive, aerospace, and construction.
What is Sand Casting?
Sand casting involves creating a mold for metal parts using sand. The process begins with the preparation of a sand mixture, which typically includes silica sand, a binding agent (usually clay), and water. This mixture provides the flexibility and strength necessary for molding. The sand is compacted around a pattern, which represents the final shape of the desired part. The pattern can be made from various materials such as metal, wood, or plastic.
The Sand Casting Process Steps
1. Pattern Creation The first step is to create a pattern that reflects the exact dimensions of the desired part. Patterns can be produced in different configurations, either as a single piece (solid pattern) or as multiple pieces (split pattern) to facilitate the removal of the cast after it solidifies.
2. Mold Preparation The next step involves preparing the mold. The pattern is placed in a mold box and surrounded by the sand mixture. The sand is compacted firmly around the pattern to form a mold cavity. Once the mold is set, the areas forming the shape of the pattern are removed, leaving the cavity that will later receive the molten metal.
3. Core Making (if necessary) If the part requires internal features or hollow sections, cores made of sand or other materials are inserted into the mold before pouring the metal. Cores are essential for creating complex geometries that cannot be formed by the mold alone.
4. Metal Pouring After the mold is prepared, molten metal is poured into the cavity. The temperature and composition of the molten metal depend on the type of metal being used, such as aluminum, iron, or bronze. As the metal fills the mold, it takes on the shape of the cavity, including any intricate details.
sand casting process
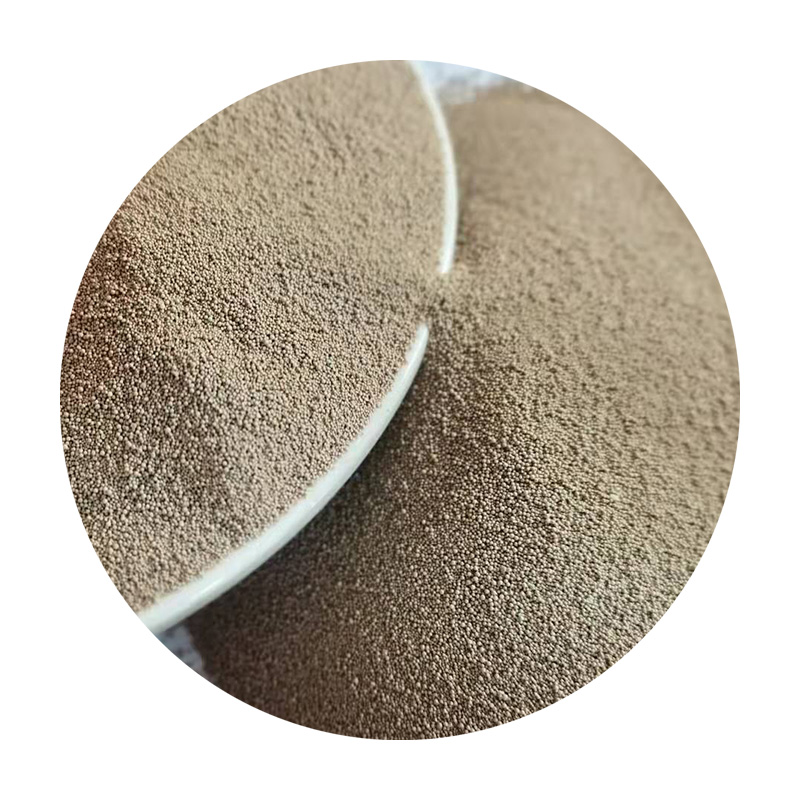
5. Cooling and Solidification The molten metal is allowed to cool and solidify. The cooling time varies depending on the size and thickness of the casting. Once cooled, the mold is broken apart, and the cast part is removed.
6. Finishing After the part is extracted, it often requires finishing processes to remove any rough edges, clean the surface, and improve dimensional accuracy. Common finishing methods include sandblasting, machining, and polishing.
Advantages of Sand Casting
One of the primary advantages of sand casting is its ability to produce large and complex parts without requiring expensive molds. The flexibility of the sand allows for easy adjustments in design, making it ideal for prototype development and low-volume production runs. Additionally, the materials used in sand casting are readily available and inexpensive compared to other casting methods.
The process also allows for the casting of a wide range of metals, with minimal setup time, further enhancing its versatility.
Applications of Sand Casting
Sand casting is employed in various industries to produce components such as engine blocks, housings, machine parts, and decorative items. Its ability to create detailed and robust structures enables manufacturers to meet the demanding requirements of modern engineering and design.
Conclusion
In summary, sand casting remains a fundamental and highly efficient method in the manufacturing industry. Its combination of affordability, adaptability, and extensive application makes it an essential process for producing a diverse array of metal parts. As technology advances, sand casting continues to evolve, incorporating new techniques and materials that enhance its effectiveness while preserving its age-old charm.
Post time:Desemba . 16, 2024 10:27
Next:Exploring the Future of 3D Printing with Innovative Sand Materials and Techniques