Understanding Sand Casting Prices A Comprehensive Overview
Sand casting is a widely used metal casting process that involves creating a mold from a sand mixture to produce metal components. This technique is favored for its versatility and cost-effectiveness in producing complex shapes. However, the price of sand casting can vary significantly based on several factors. Understanding these factors can help both manufacturers and clients make informed decisions about budget and production.
Key Factors Influencing Sand Casting Prices
1. Material Costs The type of metal being cast is one of the primary determinants of cost. Common materials used in sand casting include aluminum, iron, and magnesium. Each metal has a different price point due to raw material availability and market demand. For example, aluminum is often cheaper and more accessible than bronze or stainless steel, which can drive down overall costs.
2. Mold Complexity The complexity of the mold significantly impacts the price. A simple mold can be produced quickly and at lower costs, while intricate designs may require more detailed work, leading to higher expenses. Advanced mold designs usually necessitate more time for both the initial creation and subsequent sand preparation, contributing to increased labor costs.
3. Production Volume Economies of scale play a crucial role in determining the price of sand casting. For instance, the per-unit cost decreases with higher production volumes. This is because the fixed costs associated with mold creation are spread over a larger number of parts. Therefore, manufacturers often provide better pricing structures for bulk orders, making it essential for clients to assess their production needs.
4. Labor Costs The geographic location of the foundry can influence labor costs, which will also impact the overall price of sand casting. Regions with higher wages or stricter labor regulations will typically see increased production costs. Conversely, countries with lower labor costs might offer more attractive pricing, though this often comes at the expense of quality or turnaround times.
sand casting price
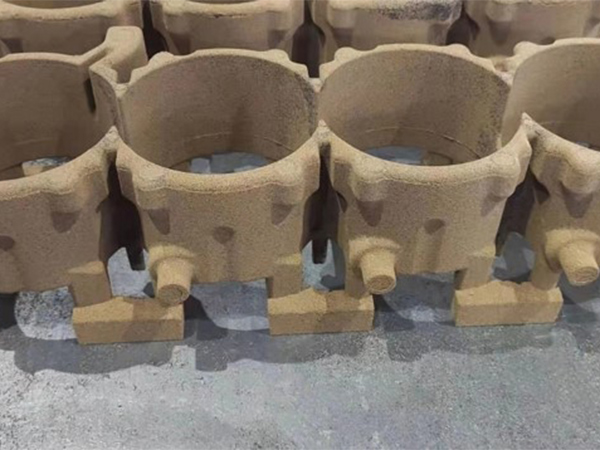
5. Turnaround Time The urgency of a project can also affect pricing. For clients requiring rapid delivery, foundries may charge a premium for expedited services. This can be especially relevant in industries such as automotive or aerospace, where time-to-market is critical. Planning production schedules in advance can help mitigate these costs.
6. Surface Finish and Post-Processing The finish required on the final product can add to the costs, as many applications necessitate additional treatment after casting. Processes like sandblasting, machining, or coating can enhance the appearance and performance of the cast parts but will result in higher overall pricing.
Comparing Sand Casting Providers
When evaluating different sand casting service providers, it's essential to consider not only pricing but also quality assurance, turnaround times, and previous client reviews. A slightly higher price from a reputable foundry that delivers consistent quality and maintains high standards may be more beneficial in the long run than opting for the lowest bidder.
Conclusion
In conclusion, while sand casting is often an economical choice for producing metal parts, understanding the various factors that drive pricing is critical for both manufacturers and clients. By carefully considering materials, mold complexity, production volume, labor costs, turnaround time, and post-processing needs, informed decisions can be made to optimize both cost and quality in sand casting projects. As the market evolves, staying informed on these factors will aid in navigating the complexities of sand casting pricing effectively.
Post time:Oktoba . 16, 2024 14:08
Next:resin coated sand price