Resin Sand Casting Process A Comprehensive Overview
Resin sand casting is a modern approach to metal casting that combines traditional sand casting techniques with the innovative use of resin as a binder. This method has gained popularity in various industries due to its numerous advantages, including improved surface finish, dimensional accuracy, and the ability to produce intricate shapes. In this article, we will delve into the resin sand casting process, its benefits, applications, and considerations for manufacturers.
The Basics of Resin Sand Casting
At its core, resin sand casting involves creating a mold using sand that is bonded together with a synthetic resin. Unlike traditional sand casting, where clay serves as a binder, resin sand casting utilizes a chemical reaction between the resin and a hardener to achieve a durable mold. This process generally follows a series of steps
1. Preparation of the Sand Mixture The sand used in resin sand casting is typically silica sand, chosen for its high heat resistance and grain characteristics. The sand is mixed with a resin binder and a hardener in a specific ratio, depending on the properties required for the casting.
2. Mold Creation The mixture is then packed around a pattern, which is a replica of the desired part. This could be either a one-piece or two-piece pattern, depending on the complexity of the part. Once the pattern is surrounded by the sand mixture, heat is applied, triggering the resin’s curing process, which solidifies the mold.
3. Mold Removal After the mold has cured, the pattern is removed carefully to avoid damaging the mold. The resulting cavity is now ready for pouring molten metal.
4. Pouring the Metal Molten metal, typically aluminum, iron, or steel, is poured into the mold cavity. The mold design ensures that the metal fills every part of the cavity, capturing even the finest details.
5. Cooling and Finishing Once the metal has cooled and solidified, the mold is broken apart to retrieve the casting. The casting is then subjected to finishing processes, such as grinding or machining, to achieve the desired surface quality and tolerances.
Advantages of Resin Sand Casting
Resin sand casting offers several advantages over traditional casting methods
- High Dimensional Accuracy The chemical bonding of the sand results in a more rigid mold that can maintain tighter tolerances, leading to higher precision in the final product.
- Superior Surface Finish Parts produced via resin sand casting often require less machining and finishing. The smooth surface quality reduces production time and costs.
- Versatility This method is highly versatile and can accommodate a wide range of alloys and part sizes, making it suitable for multiple industries, including automotive, aerospace, and artistic applications
.resin sand casting process
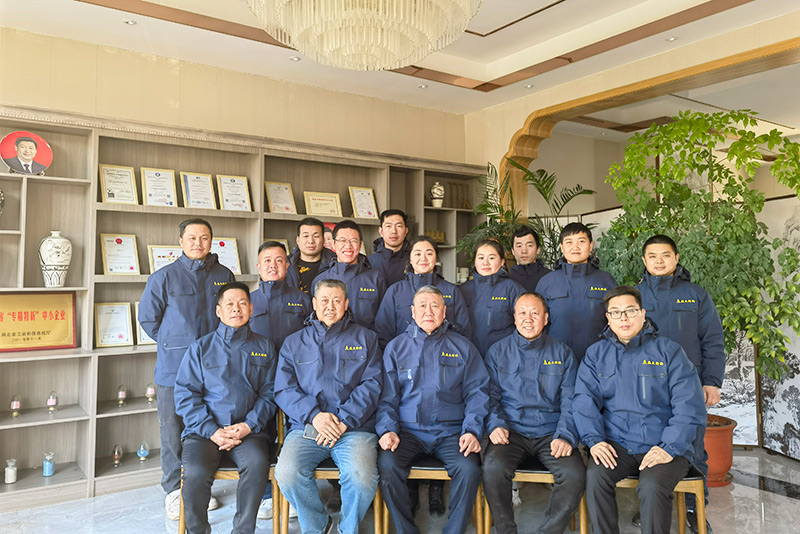
- Enhanced Detail and Complexity The ability to produce intricate designs and complex geometries makes resin sand casting ideal for applications requiring detailed features.
Applications of Resin Sand Casting
The versatility of resin sand casting allows it to be used in various sectors. Common applications include
- Automotive Components Engine blocks, transmission cases, and other critical parts can be produced with high precision and durability.
- Aerospace Components that must withstand extreme conditions benefit from the accuracy and quality that resin sand casting offers.
- Art and Sculpture Artists and designers use resin sand casting to create unique and intricate pieces that require exact detailing.
Considerations for Manufacturers
While resin sand casting presents numerous advantages, manufacturers should consider the following
- Cost Efficiency The initial investment in equipment and materials can be higher than traditional methods; however, the long-term savings in precision and reduced rework may offset these costs.
- Environmental Impact The use of synthetic resins raises environmental concerns, particularly regarding disposal. Manufacturers should seek eco-friendly alternatives and ensure proper handling of materials.
- Process Control Successful resin sand casting requires careful monitoring of the mixing ratios and curing times to achieve optimal results.
Conclusion
Resin sand casting is undoubtedly a game-changing method in the metal casting industry, offering unmatched precision, quality, and versatility. As technology continues to evolve and manufacturers adopt more sustainable practices, the future of resin sand casting looks promising, paving the way for innovative designs and applications across various sectors. Embracing this technique can provide a substantial competitive edge in today's demanding manufacturing landscape.
Post time:Oktoba . 17, 2024 08:50
Next:золаты песок на прадагу