Molding Sand for Metal Casting An Essential Component in Foundry Operations
Molding sand plays a pivotal role in the metal casting process, serving as the primary medium through which molten metal is shaped into various components and products. This sand, specifically designed for forming molds, must exhibit several crucial properties to ensure the successful production of high-quality castings. The choice of molding sand directly impacts the outcomes of metal casting operations, including the final product’s detail, strength, and surface finish.
Types of Molding Sand
There are several types of molding sand used in foundries, but the most common include green sand, dry sand, and skin-dried sand. Green sand, a mixture of sand, clay, and moisture, is the most prevalent due to its excellent pliability and ability to retain moisture. This combination allows for the creation of intricate designs and fine details, making it ideal for both ferrous and non-ferrous metal casting. Its ability to reclaim and reuse makes it an economical option for many foundries.
Dry sand, on the other hand, is used in applications where a more robust mold is necessary. It is made by drying the sand after a mixture of clay and water is added, resulting in a mold that is more durable but less flexible than green sand. Skin-dried sand is a hybrid, where the exterior of the mold is dried while keeping the interior green. This method provides benefits from both techniques, offering improved surface finish and strength.
Properties of Molding Sand
molding sand for metal casting
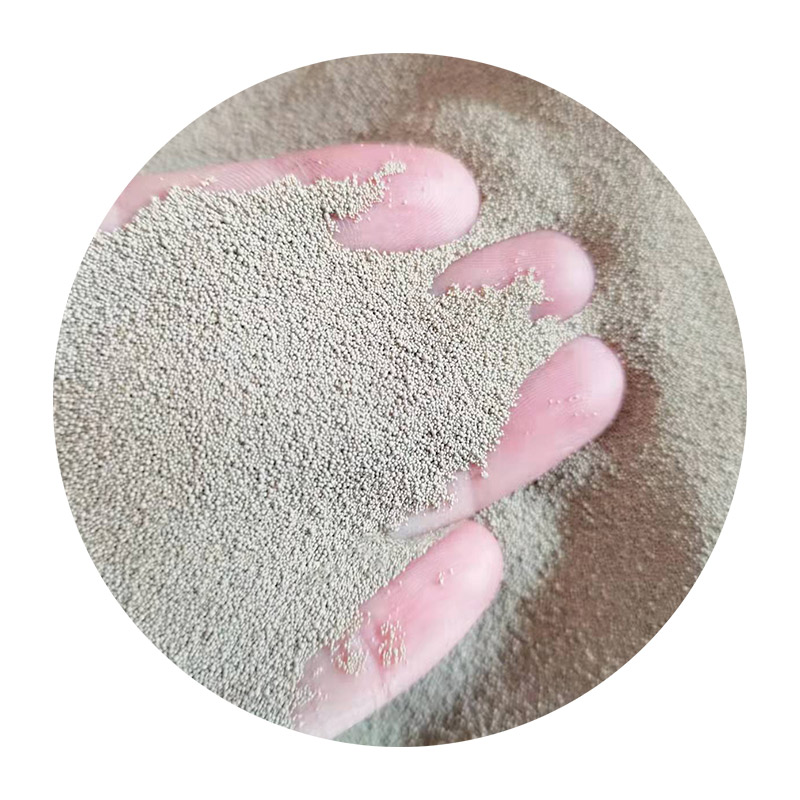
The effectiveness of molding sand in casting processes primarily depends on its properties. Key properties include grain size, shape, and distribution, which influence the mold's ability to hold detail and withstand the pressure from molten metal. Furthermore, the bonding strength provided by clay content is critical, as it affects the mold's stability during pouring. The permeability of the sand also plays a vital role; it must allow gases to escape during the pouring process to prevent defects such as blowholes in the final casting.
Another essential property is the thermal stability of the molding sand. The sand must withstand high temperatures without breaking down, which can compromise the mold integrity and affect the quality of the casting. In this regard, the addition of additives, such as graphite or other materials, can enhance the thermal resilience of the sand.
Applications in Industry
Molding sand is extensively used across various industries, including automotive, aerospace, and general manufacturing. It forms the backbone of casting operations for components such as engine blocks, turbine housings, and numerous intricate parts that require precision. Given the growing demand for high-performance materials and components in these sectors, the advancements in molding sand formulations and technologies continue to shape the future of the foundry industry.
Conclusion
In summary, molding sand is an indispensable material in the metal casting process, influencing both the efficiency of the casting operation and the quality of the final products. Understanding the different types of molding sand, their properties, and their applications allows foundry professionals to make informed choices that enhance productivity and optimize casting results. With ongoing advancements in material science, the evolution of molding sand will continue to drive innovation in manufacturing processes, leading to the production of increasingly complex and high-quality cast components. As industries evolve, the importance of understanding and utilizing the right types of molding sand will remain a cornerstone of successful metal casting operations.
Post time:Desemba . 13, 2024 06:20
Next:Enhancing Casting Quality with Premium Foundry Sand Solutions for Your Manufacturing Needs