Metal Sand Casting An Overview
Metal sand casting is a time-honored manufacturing process that plays a crucial role in producing complex metal parts with high precision and durability. This technique has been used for centuries and remains vital in various industries, including automotive, aerospace, and machinery engineering. In this article, we will explore the fundamentals of metal sand casting, its advantages, the process itself, and its applications in today's manufacturing landscape.
What is Metal Sand Casting?
Metal sand casting involves pouring molten metal into a mold made of sand. The sand mold is created from a mixture of sand, clay, and water, which binds the sand grains together. Once the mold is formed, molten metal is poured into it, filling the cavity created by the mold. After the metal cools and solidifies, the sand mold is removed, leaving behind a metal casting that accurately reflects the shape of the mold.
The Sand Casting Process
The sand casting process can be broken down into several key steps
1. Pattern Making The first step involves creating a pattern that mirrors the desired shape of the final product. Patterns can be made from various materials, including wood, metal, or plastic. They are typically slightly larger than the final product to account for shrinkage during cooling.
2. Mold Creation Once the pattern is ready, it is used to create a mold. The pattern is pressed into sand, creating a cavity. In many cases, a two-part mold is formed, allowing for easy removal of the pattern.
3. Core Making For castings featuring internal cavities or complex shapes, cores made of sand are produced and inserted into the mold. These cores are held in place until the molten metal is poured.
4. Melting Metal The chosen metal, often aluminum or iron, is melted in a furnace. The temperature and composition of the metal are carefully controlled to ensure optimal casting properties.
5. Pouring The molten metal is poured into the mold, filling the cavity and surrounding the cores if applicable. This step requires precision to prevent defects such as air pockets or inclusions.
6. Cooling After pouring, the metal is allowed to cool and solidify. Cooling time depends on the thickness of the casting and the type of metal used.
metal sand casting
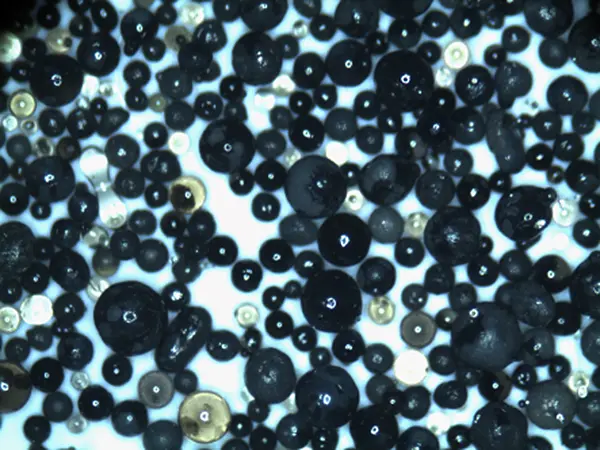
7. Mold Removal Once the metal has cooled, the sand mold is broken away to reveal the casting. This is typically done manually or with mechanical tools.
8. Finishing The final cast may require cleaning and finishing processes, including grinding, machining, or surface treatment, to achieve the desired specifications.
Benefits of Metal Sand Casting
One of the primary advantages of metal sand casting is its flexibility in producing intricate shapes and large parts. This method is particularly beneficial for low to medium production volumes as it has a lower initial tooling cost compared to other methods like die casting.
Additionally, sand casting allows for the use of a wide variety of metals and alloys, making it suitable for diverse applications. The process also has a high tolerance for dimensional accuracy, enabling the production of parts that fit together effectively in complex assemblies.
Finally, sand casting is relatively environmentally friendly compared to some other casting methods, as the sand used can be recycled and reused multiple times.
Applications of Metal Sand Casting
Metal sand casting is used in various industries, including
- Automotive Components such as engine blocks, transmission cases, and individual engine parts are commonly produced using sand casting. - Aerospace Critical parts such as turbine components and structural frames are manufactured with high precision to meet stringent safety standards. - Industrial Machinery Large machine bases, housings, and gears often use sand casting to deliver durability and reliability under heavy loads.
Conclusion
Metal sand casting remains a vital and versatile method of manufacturing, providing an economical solution for producing complex metal parts. Its ability to handle a wide range of materials and produce large, detailed shapes makes it an essential process across various industries. As technology advances, metal sand casting continues to adapt, ensuring its relevance in a rapidly evolving manufacturing landscape. Whether for historical significance, continuous improvement, or future innovations, metal sand casting represents an enduring pillar of modern engineering and manufacturing.
Post time:Desemba . 03, 2024 19:38
Next:Understanding the Sand Casting Process for Effective Metal Fabrication Techniques