Low Pressure Sand Casting A Comprehensive Overview
Low pressure sand casting is a specialized form of sand casting that has gained popularity in the manufacturing sector due to its effectiveness and efficiency. This method combines the traditional sand casting processes with low pressure techniques to create high-quality metal parts. In this article, we will explore the fundamental principles of low pressure sand casting, its advantages, applications, and factors to consider for successful implementation.
At its core, low pressure sand casting involves the use of a sand mold to shape molten metal. The primary difference from conventional sand casting lies in the method of introducing the molten metal into the mold. Instead of relying solely on gravity, low pressure sand casting uses a controlled low-pressure system to push the melted metal into the mold cavities. Typically, this low pressure ranges from 0.5 to 2.5 bars, allowing for more precise filling of the mold and reducing the likelihood of defects such as voids or air pockets.
One of the most significant advantages of low pressure sand casting is its ability to produce high-quality parts with excellent surface finishes. The controlled injection of molten metal allows for a smoother flow that fills the mold more uniformly. Consequently, this results in reduced turbulence and a better overall surface quality. The accuracy of this method also means tighter tolerances can be achieved, which is vital for components that require precise fit and function.
low pressure sand casting
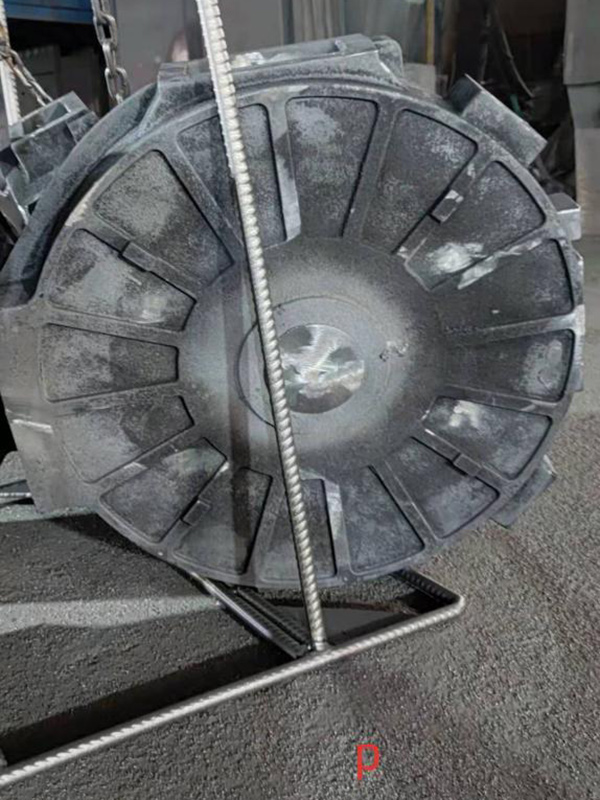
Furthermore, low pressure sand casting is more efficient compared to traditional methods. The cycle times can be significantly reduced, allowing for faster production rates. Manufacturers often find that this method leads to lower material waste, as the controlled pour minimizes excess metal, and scrap rates can be reduced. This is particularly important in today’s competitive manufacturing landscape, where efficiency and sustainability are paramount.
In terms of applications, low pressure sand casting is commonly used in industries that require the production of complex shapes and intricate designs. Automotive components, aerospace parts, and industrial machinery are just a few examples of where this technique excels. The ability to produce parts with varying wall thicknesses also makes it suitable for diverse applications.
However, several factors must be considered when deciding to use low pressure sand casting. The quality of the sand used in the casting process is crucial, as it must possess the right balance of strength and thermal stability. Additionally, the design of the mold and the gating system must be optimized to ensure efficient metal flow and minimize defects. Collaboration with experienced foundry engineers can enhance the success of any casting project.
In conclusion, low pressure sand casting offers a modern solution for producing high-quality metal parts across various industries. With its ability to create precise components with excellent surface finish and reduced cycle times, it stands out as a favorable option for manufacturers seeking efficient production methods. By understanding the principles, advantages, and considerations of this casting technique, businesses can leverage its benefits to meet their manufacturing needs effectively. As the industry continues to evolve, low pressure sand casting may well become an essential part of the metalworking landscape, driving innovation and quality in production.
Post time:Oktoba . 12, 2024 00:03
Next:china sand casting factory