Lost Foam Castings A Comprehensive Overview
Lost foam casting (LFC) is an innovative and efficient metal casting process that has gained popularity in various industries due to its unique advantages over traditional casting methods. This technique involves the use of a foam pattern that is coated with a refractory material, creating a mold into which molten metal is poured. As the metal fills the mold, the foam pattern evaporates, leaving a precise and intricate metal part. This article explores the principles, advantages, applications, and future trends of lost foam castings.
The Process of Lost Foam Casting
The lost foam casting process begins with the creation of a foam pattern, typically made from polystyrene or a similar material. This pattern is designed to reflect the exact dimensions and details of the final casting, ensuring high accuracy. Once the foam pattern is produced, it is coated with a mixture of sand and a binding agent, forming a shell around the foam. After the coating has hardened, the shell is heated to evaporate the foam pattern, leaving a cavity in the shape of the desired part.
Next, molten metal is poured into the cavity. One of the key advantages of this method is that the metal flows into the mold while the foam is evaporating, which minimizes defects such as gas porosity and shrinkage. Once the metal cools and solidifies, the shell is broken away to reveal the finished casting.
Advantages of Lost Foam Castings
The lost foam casting technique offers several significant advantages
1. Complex Geometries LFC enables the production of intricate shapes and designs that would be difficult or impossible to achieve with traditional casting methods. This is particularly beneficial for industries that require detailed components, such as aerospace and automotive.
2. Material Efficiency The method is highly efficient in terms of material usage. The foam pattern is lightweight and requires less energy to produce compared to solid metal patterns. Moreover, there is minimal waste, as the foam evaporates entirely during the process.
3. Improved Surface Finish Parts produced through lost foam casting often exhibit superior surface finishes, reducing the need for extensive machining and post-processing. This can significantly lower production costs and lead times.
4. Rapid Prototyping The ability to quickly create foam patterns allows for rapid prototyping, enabling engineers and designers to test and iterate designs more efficiently.
lost foam castings
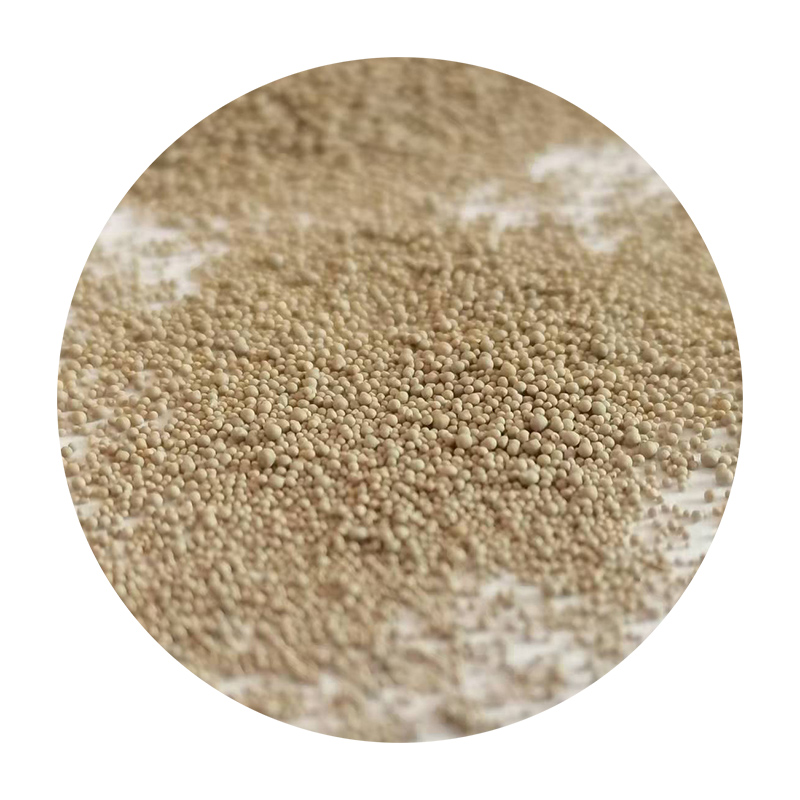
Applications of Lost Foam Castings
Lost foam casting is employed in a wide range of industries, including
- Automotive Components such as engine blocks, cylinder heads, and transmission housings benefit from the precision and complexity achievable through lost foam casting.
- Aerospace Aerospace manufacturers utilize LFC for producing lightweight and complex components that meet stringent regulations.
- Heavy Machinery Parts for construction and mining equipment often take advantage of the durability and design flexibility offered by lost foam castings.
- Art and Design Artists and designers utilize LFC for creating sculptures and custom pieces that require unique shapes and high detail.
Future Trends
As industries continue to push for innovation and efficiency, the future of lost foam casting looks promising. Advancements in materials for foam patterns and coating techniques are likely to enhance the process further. Additionally, the integration of automation and digital technologies in manufacturing may streamline the lost foam casting process, making it even more accessible and affordable.
In conclusion, lost foam casting is a versatile and effective casting method that addresses many challenges faced in conventional casting processes. Its benefits, including design flexibility, material efficiency, and reduced defect rates, make it a valuable technique in today’s manufacturing landscape. As technology continues to evolve, lost foam casting is poised to play an increasingly significant role in producing high-quality components for various industries.
Post time:Novemba . 14, 2024 14:58
Next:sand and polish resin