The Iron Sand Casting Process An Overview
Iron sand casting is a process that transforms iron-rich sand into functional metal components through various stages of creation, shaping, and solidification. This traditional method of metal casting is gaining attention due to its efficiency, environmental benefits, and ability to produce high-quality castings. This article explores the intricacies of the iron sand casting process, including its benefits, methods, applications, and challenges.
Understanding the Iron Sand Casting Process
Iron sand casting involves several critical steps. First, iron sand, which consists largely of iron oxide, is sourced from beaches or riverbeds. The sand is characterized by its fine grain and magnetic properties, making it an ideal candidate for metal casting. The process begins with creating a mold, typically made from a mixture of iron sand and a bonding agent such as clay or resin.
Molding
The molding process is crucial, as it defines the shape and quality of the final product. Mold patterns are created using various techniques, including wood, metal, or 3D printing. The iron sand is then packed around the pattern, compacted to ensure stability, and cured if necessary. Once set, the mold halves are carefully separated to allow for the placement of the molten iron.
Melting and Pouring
The next step involves melting the iron. This is typically done in a furnace capable of reaching high temperatures required to liquefy the metal. Modern techniques often use electric arc furnaces or induction furnaces, which provide better temperature control and energy efficiency. Once molten, the iron is poured into the prepared molds, filling them precisely to create the desired components.
Cooling and Finishing
iron sand casting process
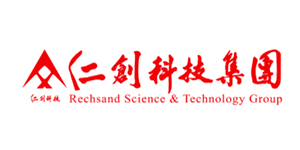
After pouring, the molten iron is allowed to cool and solidify within the molds. This cooling phase is essential as it affects the material's microstructure and, therefore, its properties. Once solidification is complete, the molds are opened, and the casting is removed. The excess sand is shaken off, and the new casting may undergo additional finishing processes, such as sandblasting or machining, to achieve the required surface quality and dimensional accuracy.
Benefits of Iron Sand Casting
Iron sand casting offers several advantages. Firstly, it is a cost-effective method; the raw materials are often inexpensive and widely available compared to other casting methods. The process is also relatively quick, which can lead to lower production times. Furthermore, iron sand casting is environmentally friendly as it recycles industrial by-products, reducing waste and promoting a circular economy.
Applications
The versatility of iron sand casting means that it can be used in various industries, including automotive, aerospace, and construction. Components such as engine blocks, pump housings, and agricultural machinery parts are commonly produced using this method. Additionally, as the demand for high-quality and durable castings increases, iron sand casting is becoming the go-to process for many manufacturers.
Challenges in Iron Sand Casting
Despite its many benefits, the iron sand casting process is not without challenges. One of the major concerns is the consistency of the casting quality, which can be affected by the quality of the iron sand and the precision of the mold-making process. Proper handling of the molten iron is also critical, as any contamination or temperature fluctuation can lead to defects in the final product.
In conclusion, the iron sand casting process is a sophisticated and efficient method of producing high-quality metal components. Its ability to produce durable castings at a lower cost and its minimal environmental impact make it an attractive option for various industries. While there are challenges to address, advancements in technology and processes continue to enhance the effectiveness and reliability of iron sand casting. As the industry evolves, it will likely play an increasingly vital role in meeting the manufacturing needs of tomorrow.
Post time:Septemba . 28, 2024 22:26
Next:Achieve Perfectly Smooth 3D Prints with No Sanding Required