How Does Sand Casting Work?
Sand casting is one of the oldest and most widely used methods for metal casting. This technique allows the reproduction of complex shapes and designs, making it a favored choice in various industries, from automotive to aerospace. Understanding how sand casting works not only provides insights into its applications but also highlights its advantages and limitations.
The process begins with the preparation of a pattern, which is a precise replica of the final product. Patterns are typically made from materials such as wood, metal, or plastic, and they can vary in size and complexity. The pattern is used to create a mold, which is essential for shaping the molten metal. The mold consists of two halves the cope (the top half) and the drag (the bottom half).
How Does Sand Casting Work?
Next, the two halves of the mold are reassembled, and openings are created for pouring the molten metal—these are called gates. A venting system is also established to allow gases to escape during the pouring process, preventing defects in the final casting.
how does sand casting work
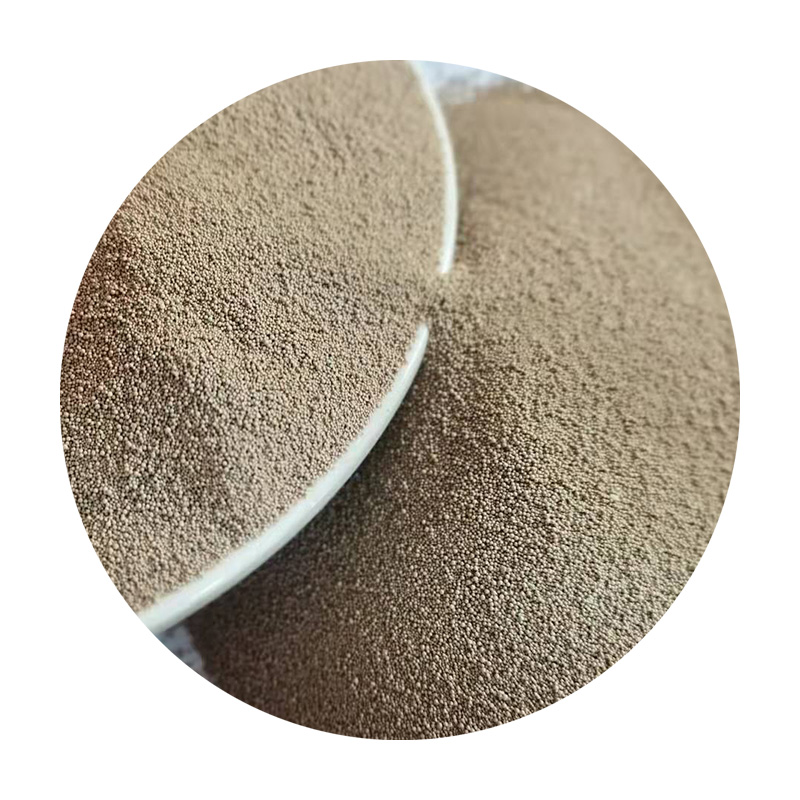
At this point, it is time to prepare the molten metal. This involves heating the metal to its melting point, which varies depending on the metal used. Common metals for sand casting include aluminum, iron, and bronze. Once the metal is sufficiently molten, it is poured into the mold through the gates. The liquid metal flows into the cavity, taking the shape of the pattern as it cools and solidifies.
After the metal has cooled and hardened, the mold is broken apart, and the solidified casting is removed. The casting will often require some post-processing work, including trimming excess material, cleaning, and machining to achieve the desired finish and precision. Sand casting can produce complex shapes but often requires additional finishing steps due to the inherent roughness of the sand mold surface.
One of the significant advantages of sand casting is its versatility. Because it can accommodate various metals and is suitable for producing both small and large quantities, it is an ideal choice for custom and prototype work. The process is also relatively inexpensive compared to other casting methods. However, sand casting does have its limitations. The surface finish is not as smooth as other techniques like investment casting, and the tolerance levels may not be as stringent.
In summary, sand casting is a straightforward yet highly effective method for producing metal components. By employing a pattern to form a mold, pouring molten metal, and allowing it to cool, manufacturers can create intricate parts used in a wide range of applications. Despite its limitations, sand casting remains a vital process in the metalworking industry, demonstrating the enduring importance of this age-old technique.
Post time:Septemba . 30, 2024 23:34
Next:Vorteile des Sandgießverfahrens in der Industrie und Fertigung