Understanding Foundry Sand Definition, Types, and Applications
Foundry sand is a crucial material in the metalcasting industry, primarily used in the production of molds and cores for metal casting processes. The quality and composition of foundry sand directly influence the final characteristics of cast products, making its definition and understanding essential for manufacturers.
Definition of Foundry Sand
Foundry sand refers to a specific type of sand that is used in the foundry industry, particularly for casting metals. It is typically composed of silica (SiO2) and has unique properties that allow it to withstand high temperatures and maintain its integrity during the casting process. The essential characteristics that define foundry sand include grain size, shape, refractoriness, and permeability.
Types of Foundry Sand
There are several types of foundry sand, each with distinct properties that cater to different casting processes. The most common types include
1. Silica Sand This is the most widely used type of foundry sand due to its excellent thermal stability and high strength. Silica sand is available in various grain sizes and is typically used in ferrous and non-ferrous metal casting.
2. Zircon Sand Zircon sand is known for its high melting point and chemical stability, making it ideal for producing precision castings and molds that require low expansion.
3. Chromite Sand Used primarily for the production of green sand molds, chromite sand has excellent thermal properties. It is often employed for casting high-alloy steels where dimensional accuracy and surface finish are critical.
4. Nutritional Sand Often used in the manufacturing of industrial and specialty sands, this type is less common but plays a role in specific applications where niche characteristics are needed.
foundry sand definition
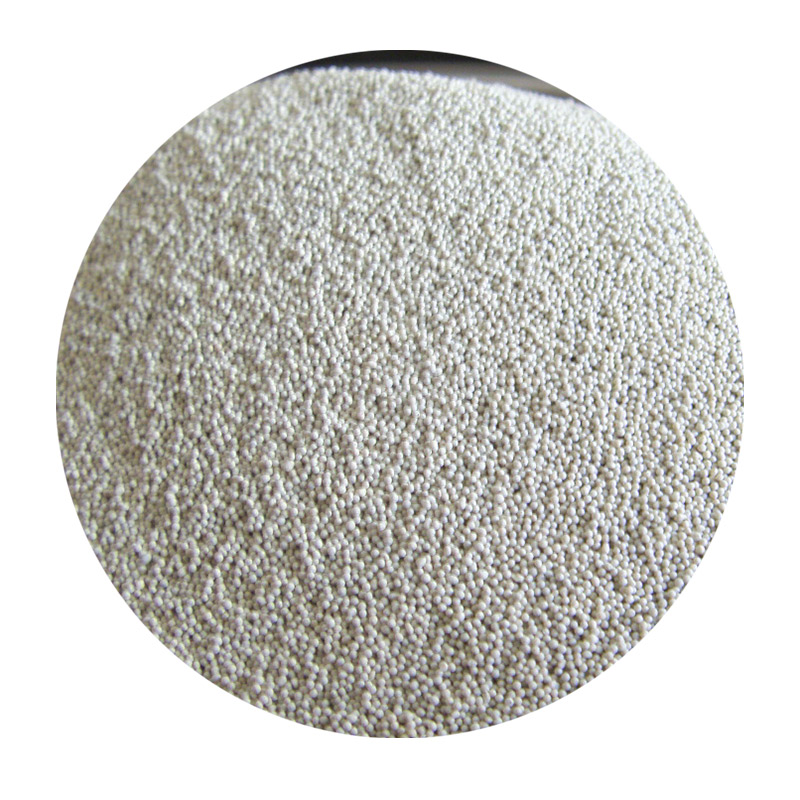
5. Synthetic Sand With advancements in technology, synthetic sands are created using industrial by-products or engineered materials. They often possess enhanced properties like improved mold strength, reduced variability, and better control over molding characteristics.
Applications of Foundry Sand
Foundry sand plays a pivotal role in various applications within the metalcasting industry. Its primary function is to form molds and cores for casting metals, and it is widely utilized in many sectors, including automotive, aerospace, and machinery manufacturing.
1. Metal Casting The primary application of foundry sand is in metal casting processes, where it serves as a mold for shaping molten metal. The sand's ability to retain its shape under heat and pressure allows for the accurate reproduction of intricate designs.
2. Sand Casting This traditional method involves creating a mold from sand and pouring molten metal into it to form a desired shape. The reusable nature of foundry sand makes it a cost-effective option for producing high volumes of castings.
3. Core Production Foundry sand is also essential for making cores—solid parts placed within molds to create internal cavities in cast products. Cores made from foundry sand allow for greater design flexibility and reduced need for machining.
4. Recycling and Sustainability The foundry industry is increasingly focused on sustainable practices. Used foundry sand is often recycled for various applications, including road construction and as a fill substance. This not only minimizes waste but also reduces the need for virgin sand extraction.
Conclusion
In summary, foundry sand is a fundamental material in the metalcasting industry, characterized by its silica content and specific properties that enhance its performance in mold making. Understanding the definition, types, and applications of foundry sand is essential for professionals in the field, as it directly impacts the quality and efficiency of the casting process. As the industry evolves, so does the need for innovative uses and sustainable practices surrounding foundry sand, highlighting its importance in modern manufacturing.
Post time:Novemba . 14, 2024 21:12
Next:cerabeads