The Importance of Foundry Casting Sand in Metalworking
Foundry casting sand plays a critical role in the metalworking industry, serving as an essential material for producing metal components through sand casting processes. This age-old technique has been refined over centuries, and despite advancements in technology, the fundamental principles of using sand remain unchanged. In this article, we will delve into the importance of foundry casting sand, its types, properties, and the pivotal role it plays in the casting process.
Understanding Foundry Casting Sand
Foundry casting sand is a granular material used to create molds for shaping molten metal. Traditional sand casting involves packing sand around a pattern, which is a replica of the final product. Once the pattern is removed, the cavity that remains is filled with molten metal. The sand must possess specific characteristics to ensure the quality and precision of the casted item.
The most commonly used type of sand in foundry operations is silica sand, primarily because of its availability and cost-effectiveness. However, there are various additives and binder materials that can enhance certain properties, such as clay, resin, and water, which contribute to better mold strength and durability.
Properties of Ideal Casting Sand
The effectiveness of foundry casting sand is determined by several key properties
1. Grain Size and Shape The grain size of the sand affects its flowability and compaction. A mixture of fine and coarse granules can yield optimal results, allowing for better mold filling and reducing defects in the final product. The shape of the sand grains also influences how tightly they can pack together, impacting the mold strength.
2. Permeability This refers to the ability of the sand mold to allow gases produced during the melting process to escape. High permeability ensures that gases do not become trapped in the molten metal, which can lead to defects such as porosity and inclusions.
3. Strength The mechanical strength of the sand mold is vital. It must be strong enough to withstand the pressure of the molten metal without collapsing or bleeding sand into the cast.
foundry casting sand
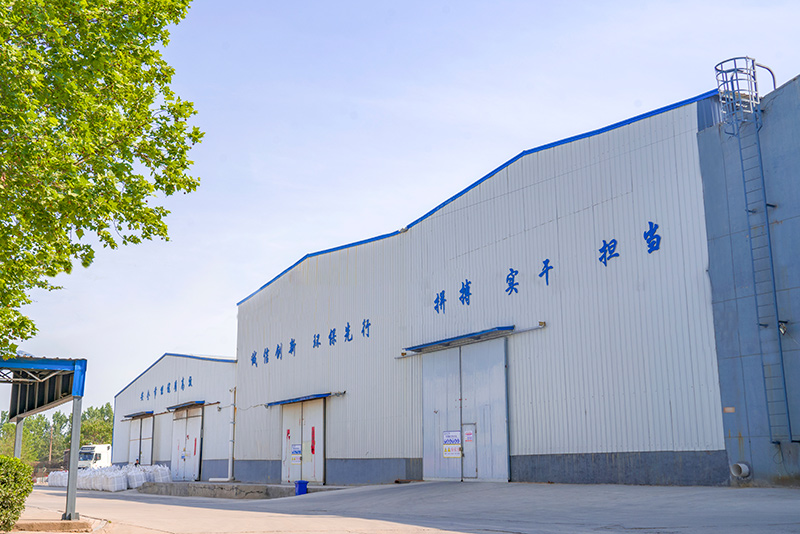
4. Reusability One of the advantages of foundry casting sand is its reusability. After a casting operation, the sand can be reclaimed and treated for reuse, making it a cost-effective choice for foundry operations.
5. Thermal Stability The sand should maintain its integrity at high temperatures. Thermal stability ensures that it does not lose its structural characteristics when in contact with molten metal.
The Role of Foundry Casting Sand in the Casting Process
The casting process in foundries is complex and requires meticulous attention to detail. The quality of the sand directly influences the quality of the cast product. A well-prepared sand mold results in better surface finishes, precise dimensions, and fewer casting defects. The use of high-quality sand minimizes the need for post-casting machining, thus reducing manufacturing costs.
Moreover, advancements in technology have led to the development of engineered sands with specific properties tailored for particular casting applications. For instance, new sands that incorporate synthetic materials can provide enhanced performance, such as improved dimensional accuracy and reduced environmental impact.
Environmental Considerations
The foundry industry is continuously seeking sustainable practices, including the management of casting sand. Foundries are adopting measures to recycle sand and reduce waste, minimizing their environmental footprint. Innovations in sand processing technology also contribute to these efforts, helping to enhance the recyclability of foundry casting sand.
Conclusion
In conclusion, foundry casting sand is a cornerstone of the metalworking industry. Its distinct properties and functionalities make it indispensable for producing high-quality cast products. As foundries continue to evolve with technological advances, the emphasis on using superior casting sand will only increase, ensuring efficient production processes, superior product integrity, and a strong commitment to sustainability. The future of metal casting remains bright, with foundry casting sand at the heart of every innovation and development in this thriving industry.
Post time:Novemba . 17, 2024 12:34
Next:investment casting sand