Components of Sand Casting
Sand casting is one of the oldest and most widely used metal casting processes. This technique involves creating metal parts by pouring molten metal into a mold formed from sand. Understanding the components involved in sand casting is crucial for engineers and manufacturers seeking to optimize the casting process.
1. Mold
The mold is the core component of sand casting. It is typically made from a mixture of sand, clay, and water, which gives it the necessary properties to withstand the heat of molten metal. The sand used in molds can be either green sand or dry sand. Green sand, which contains moisture, is commonly used for its excellent flowability and ability to conform to the shape of the pattern. The mold is created in two halves, known as the cope (upper part) and drag (lower part), which are joined together to form the cavity where the molten metal is poured.
2. Pattern
The pattern is a replica of the final product and is crucial for creating the mold cavity. Patterns can be made from various materials, including wood, metal, or plastic, depending on the complexity and the required production volume. The pattern must be slightly larger than the final part to account for shrinkage that occurs as the metal cools and solidifies. Patterns can be classified into solid, split, or matchplate types, depending on the design of the required part.
3. Core
components of sand casting
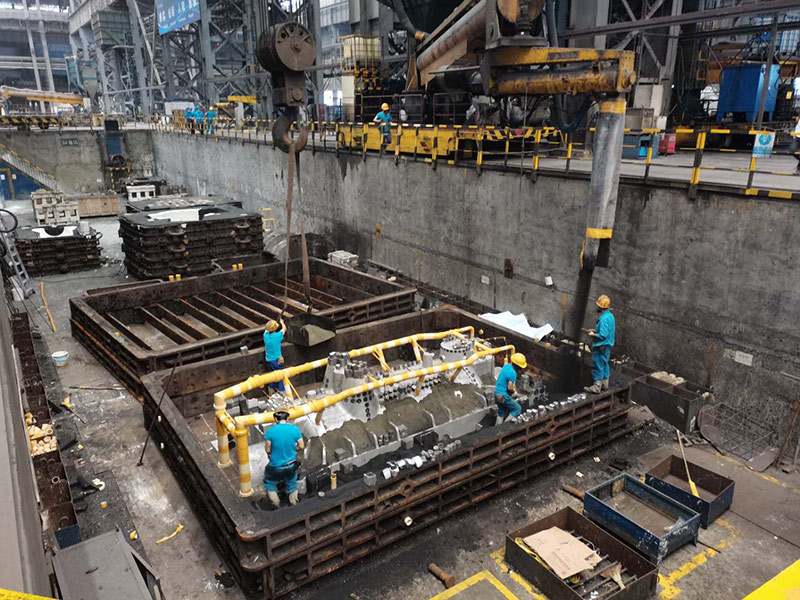
In many sand casting applications, cores are used to create internal cavities or complex features within the cast part. Cores are typically made from sand and are placed in the mold before pouring the metal. They must be crafted with precision to ensure they fit comfortably within the mold cavity, as they can significantly influence the final dimensions of the casting.
4. Melting Furnace
The melting furnace is where the metal is heated to its liquid form before being poured into the mold. Different types of furnaces such as induction, cupola, or electric arc furnaces can be used, depending on the type of metal being cast and the required production scale.
5. Gating System
The gating system consists of channels through which molten metal flows from the pouring cup into the mold cavity. An efficient gating system is crucial for minimizing turbulence and ensuring that the mold fills completely, thereby reducing defects in the final product.
Conclusion
In summary, the components of sand casting—mold, pattern, core, melting furnace, and gating system—play distinct yet interconnected roles in the casting process. Mastering these components allows for improved quality, efficiency, and precision in metal casting, making sand casting a preferred method in various industries, from automotive to aerospace. Understanding and optimizing each component can lead to advancements in manufacturing practices and the production of superior metal parts.
Post time:Oktoba . 04, 2024 19:16
Next:resin coated sand process