Casting Sand An Integral Part of Metalwork
Casting sand is a crucial component in the metal casting industry, where metal objects are formed by pouring molten metal into a mold made from sand. This age-old technique is not only efficient but also cost-effective, allowing for the production of complex shapes and structures. The role of casting sand extends beyond mere support for the molten metal; it contributes significantly to the quality of the final product, influencing various aspects from surface finish to dimensional accuracy.
The primary type of sand used in casting is silica sand, due to its high melting point and ability to withstand the intense heat generated during the casting process. Silica, being abundant and relatively inexpensive, makes it an ideal choice for foundries. However, casting sand isn't just regular sand; it must possess certain properties to be effective. Key characteristics include grain size, shape, and the ability to retain moisture, which together determine how well the sand can form molds and withstand the heat of molten metal.
One of the most notable advantages of using sand for casting is its versatility. Foundries often employ various types of sand mixtures, sometimes adding clay or other materials to enhance the properties of the sand. For instance, clay provides binding capabilities, preventing the sand grains from shifting or deforming when the molten metal is poured into the mold. This combination of sand and clay creates a resilient mold that can accurately replicate the intricate details of the original design.
casting sand
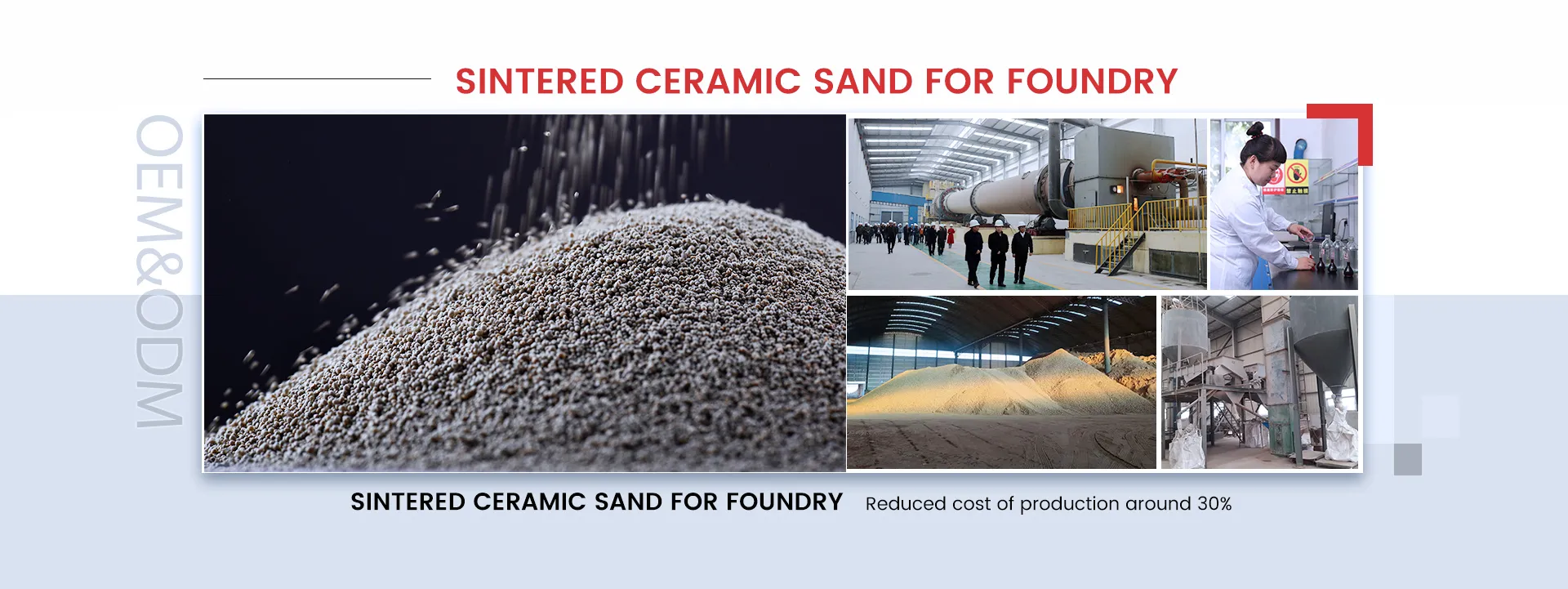
Moreover, the ability to reuse casting sand makes it both economical and environmentally friendly. After a cast is completed, the sand can be reclaimed, cleaned, and reused for new molds. This recyclability not only reduces waste but also lowers the overall material costs for foundries. The advancements in sand reclamation technologies have further improved the efficiency of this process, ensuring that the sand can be reused multiple times without losing its vital properties.
However, the use of casting sand does come with challenges. One of the main issues is the potential for sand-related defects in the final casting. These defects can arise from issues such as sand contamination, inadequate mold strength, or poor sand preparation. To mitigate these risks, foundries invest in rigorous quality control measures and maintain precise environmental conditions during the casting process. Additionally, continuous research and development in materials science seek to enhance the performance of casting sand, leading to innovations that can improve casting quality and reduce defects.
Another key consideration in the use of casting sand is its interaction with the molten metal. During the casting process, the sand must not react chemically with the metal to prevent undesirable reactions that could compromise the integrity of the final product. Foundries often conduct extensive testing to ensure that the specific type of sand being used is compatible with the alloys being cast.
In conclusion, casting sand plays a fundamental role in the metal casting industry, offering a cost-effective and flexible solution for producing intricate metal parts. Its properties, recyclability, and versatility make it an indispensable resource for foundries. As technology continues to evolve, the methods and materials used in sand casting are likely to advance, enhancing the efficiency and quality of metal production. The future of casting sand promises exciting developments, maintaining its vital place in the world of manufacturing.
Post time:Desemba . 16, 2024 12:19
Next:Affordable Options for 3D Sand Printer Pricing and Features