The Evolution of 3D Sand Printing in Casting
In recent years, 3D sand printing has emerged as a transformative technology within the casting industry. This innovative process involves using 3D printing techniques to produce sand molds and cores that are subsequently used to cast metal parts. This article delves into the advantages, applications, and future prospects of 3D sand printing in casting.
The Evolution of 3D Sand Printing in Casting
One of the outstanding benefits of 3D sand printing is its ability to create highly intricate designs that would be impossible or prohibitively expensive to achieve with traditional molding techniques. The layer-by-layer approach of 3D printing allows for the creation of complex geometries, such as internal cooling channels or lightweight structures, which enhance the performance of the final cast product. This capability is particularly valuable in industries such as aerospace, automotive, and energy, where performance and weight savings are critical.
3d sand printing casting
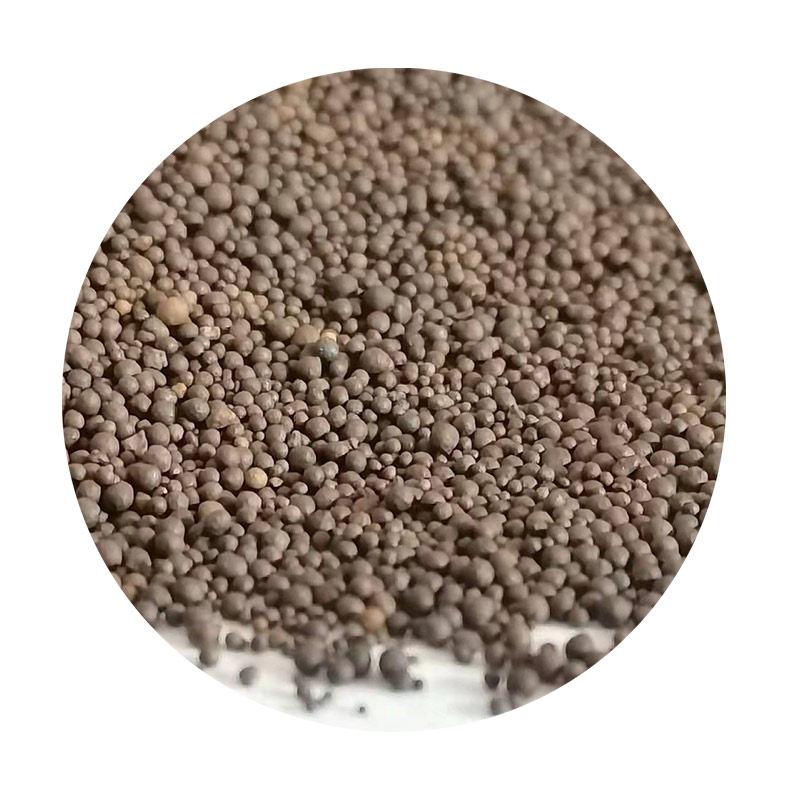
Furthermore, 3D sand printing promotes a more sustainable production process. Because the molds are printed directly from computer-aided design (CAD) files, there is minimal waste generated during the production process. Traditional molding methods often result in excess material that must be disposed of, contributing to environmental concerns. In contrast, 3D printing allows for a more efficient use of resources, as sand can be reused multiple times for different prints.
Another significant advantage of 3D sand printing is its flexibility in production. Designers and engineers can rapidly prototype and iterate on their designs without the need for extensive retooling or the creation of new patterns. This agility enables manufacturers to respond quickly to market demands, making it easier to customize products for specific applications or clients.
As for the future of 3D sand printing in casting, the technology is still evolving. With advancements in material science and printing techniques, we can expect to see improvements in the mechanical properties of printed molds, broadening the applications of 3D sand printing even further. Additionally, as the costs associated with 3D printing continue to decrease, we may witness wider adoption across industries that have traditionally relied on conventional casting methods.
In conclusion, 3D sand printing is charting a new course for the casting industry by introducing efficiency, creativity, and sustainability into the mold-making process. As the technology matures, its integration into mainstream manufacturing will likely pave the way for innovative designs and production techniques, ultimately changing the landscape of how metallic components are produced. With ongoing research and development, the future of 3D sand printing in casting holds great promise, setting the foundation for the next generation of manufacturing excellence.
Post time:Septemba . 23, 2024 06:32
Next:rapid sand casting