The Role of Sand in Sand Casting Types and Characteristics
Sand casting, one of the oldest and most versatile manufacturing processes, serves as a reliable method for producing metal parts. It involves pouring molten metal into a mold made from a mixture of sand and a bonding agent, which then solidifies to form the desired part. The type of sand used in this process is crucial, as it directly affects the quality of the casting. In this article, we will explore the various types of sand used in sand casting, their properties, and how they contribute to the overall quality of the castings produced.
1. Silica Sand
Silica sand, primarily composed of silicon dioxide (SiO2), is the most commonly used sand in casting processes. This sand is highly plentiful and has excellent thermal properties, allowing it to withstand the heat of molten metal. Silica sand grains are typically rounded, which helps in creating a smooth surface for the casting. The grain size can vary, generally ranging from fine to coarse, depending on the specific requirements of the casting. Fine silica sand provides better detail in intricate designs, while coarser sand is suitable for larger, simpler shapes.
2. Green Sand
Green sand, a mixture of silica sand, clay, water, and other additives, is another widely used type of sand in sand casting. This mixture gets its name from its moist condition before molding, which helps the sand particles stick together. The clay in green sand acts as a binding agent, ensuring good cohesion and providing the necessary plasticity to create a mold that holds its shape under pressure. The water content enhances the molds’ ability to capture fine details during the casting process. Green sand is particularly popular in foundries due to its low cost and effective performance, especially for iron and aluminum castings.
what type of sand is used for sand casting
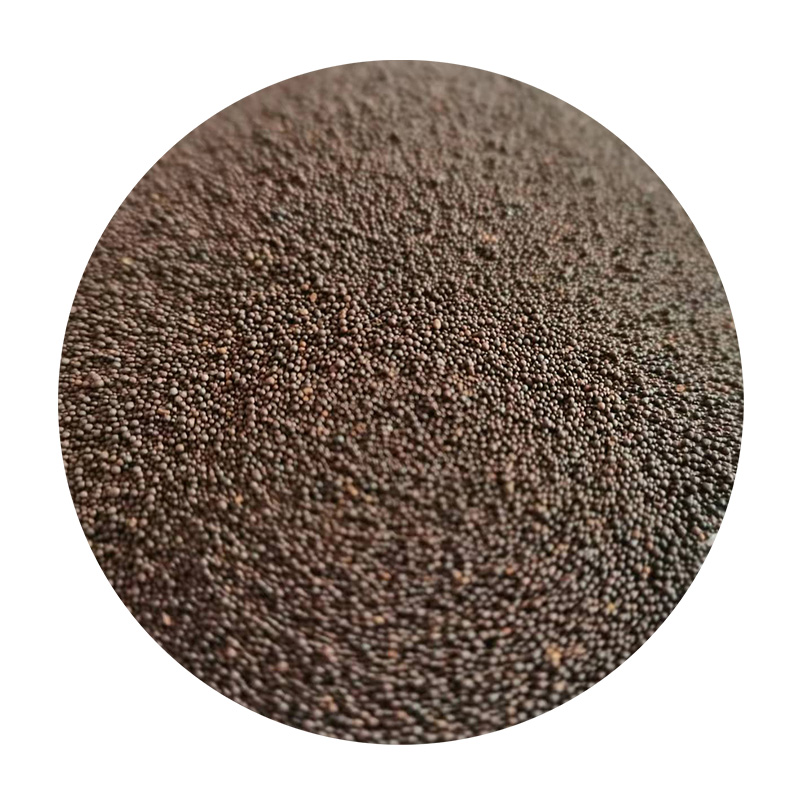
In situations where higher precision and surface quality are needed, resin-bonded sands are often utilized. This type of sand uses synthetic resins as a bonding agent, which allows for stronger mold and core production. The most common types of resin-bonded sand include phenolic resin and furan resin sands. These sands can withstand higher temperatures and provide finer surface finishes than traditional green sands. However, they can be more expensive and require additional curing processes, often involving heat or chemical hardeners.
4. Shell Sand
Shell sand is another advanced material used in sand casting, particularly for complex geometries and high-quality surface finishes. It consists of a fine silica sand coated with a thermosetting resin. The coating process typically involves heating the sand mixture so that the resin bonds to the sand particles, forming a thin shell. This results in molds that are durable and provide excellent dimensional accuracy. Shell sand casting is particularly beneficial in producing small to medium-sized components for aerospace, automotive, and intricate art pieces.
5. Other Specialized Sands
Besides the commonly used sands mentioned above, there are also specialized sands designed for specific applications. Zircon sand and chromite sand, for instance, are used when casting materials that require high refractoriness or specific chemical properties. These sands have unique mineral compositions that offer advantages in particular casting environments, such as resistance to high temperatures and lower thermal expansion rates.
Conclusion
The choice of sand in the sand casting process has a significant influence on the final outcome of the products. Silica sand, green sand, resin-bonded sand, and shell sand each possess unique properties that cater to different requirements, from cost-effectiveness and versatility to high precision and surface finish quality. Understanding the characteristics and applications of these sands is essential for foundries and manufacturers aiming to optimize their casting processes and produce high-quality metal parts. In the ever-evolving landscape of manufacturing, the right type of sand remains a cornerstone of successful sand casting.
Post time:dec . 19, 2024 17:26
Next:Techniques and Innovations in Sintering Processes for Sand Materials in Industrial Applications