The Steps of Sand Casting A Comprehensive Overview
Sand casting, one of the oldest and most versatile methods of metal casting, is widely used in various industries due to its cost-effectiveness and ability to produce complex shapes. This process involves creating molds from sand to hold molten metal until it cools and solidifies. Understanding the steps involved in sand casting is essential for anyone interested in manufacturing processes or metallurgical engineering. In this article, we will explore the critical stages of the sand casting process.
1. Pattern Making
The first step in sand casting is the creation of a pattern, which is a replica of the final product to be cast. Patterns can be made from various materials such as wood, metal, or plastic, and they are usually slightly larger than the intended final product to account for the shrinkage that occurs during cooling. There are two main types of patterns solid patterns, which are single pieces, and split patterns, which are divided into two or more sections to facilitate easy removal from the mold.
2. Mold Preparation
Once the pattern is created, the next step is to prepare the mold. This involves placing the pattern into a mixture of sand and a bonding agent, typically clay, that holds the sand grains together. The sand is compacted around the pattern to create a mold cavity shaped like the pattern. The mold is created in two halves, usually referred to as the cope (top half) and the drag (bottom half). After the sand has been compacted, the two halves of the mold are carefully separated and the pattern removed, leaving a hollow cavity in the shape of the desired object.
3
. Core Making (if required)Some castings may require internal features that cannot be achieved through the mold alone. In such cases, cores made from sand or metal are created and inserted into the mold. Cores are additional pieces that form internal channels or cavities, like holes or hollow sections. They are made separately and are carefully placed in the mold cavity before pouring the molten metal.
4. Melting the Metal
Once the mold is ready, the next step is to melt the metal to be cast. The metal, typically aluminum, iron, or bronze, is heated in a furnace until it reaches a molten state. The choice of metal depends on the desired properties of the final product. Precise temperature control is critical, as different metals have different melting points and properties.
steps of sand casting
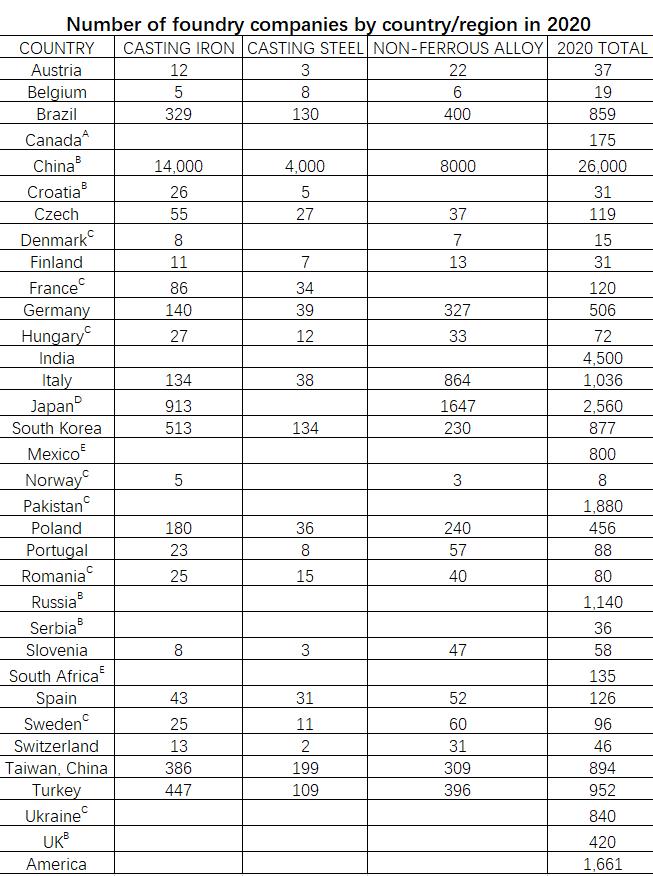
5. Pouring the Molten Metal
After the metal is melted and appropriately heated, it is then poured into the prepared mold. This step must be performed carefully to avoid introducing defects, such as air pockets or inclusions. The pouring process can be done manually or using automated systems, depending on the scale of production. It is essential to ensure that the molten metal fills the mold cavity completely.
6. Cooling and Solidification
Once the molten metal is poured into the mold, it begins to cool and solidify. The cooling time varies depending on the type of metal, the size of the casting, and the mold material. During this phase, the molten metal transitions to a solid state, taking on the shape of the mold cavity. It is crucial not to rush this process, as uneven cooling can lead to warping or cracks in the final product.
7. Mold Removal
After sufficient cooling time has passed, the mold is carefully broken apart to remove the casting. This step may involve knocking the sand away or using vibrations to dislodge the casting. The casting is then inspected for any defects or imperfections that may have occurred during the casting process.
8. Finishing Processes
The final step in the sand casting process is finishing. This may involve removing excess material, smoothing the surface, and performing any additional machining or treatment necessary to achieve the desired specifications. Techniques such as grinding, polishing, and sandblasting may be used to enhance the surface quality of the casting.
Conclusion
The sand casting process is a time-honored method that remains relevant in modern manufacturing. By understanding each step involved, from pattern making to finishing, engineers and manufacturing professionals can optimize the casting process to produce high-quality metal components efficiently. Whether for small-scale applications or large industrial productions, sand casting continues to be a vital manufacturing process across various industries.
Post time:nov . 24, 2024 17:44
Next:Utilizing Foundry Sand in Concrete Mixes for Enhanced Performance and Sustainability