Sand Casting Iron
Sand casting is one of the oldest and most versatile metal casting techniques, primarily used for producing iron components. This process involves the use of sand as a mold material, accommodating a variety of shapes and sizes, making it an ideal choice for both large-scale industrial and smaller commercial applications. The properties of sand, combined with iron's characteristics, create a reliable method for manufacturing metal parts with intricate designs and a high level of precision.
The Process of Sand Casting
The sand casting process begins with the creation of a mold. This involves forming a mixture of sand, clay, and water to create a sand mold. The first step is molding, where the necessary pattern, often made from metal or plastic, is pressed into the sand to create the cavity that will form the final product. Once the pattern is removed, the mold is assembled, making sure that the two halves fit snugly together.
Next, molten iron is poured into the mold. Iron is preferred in many casting operations due to its excellent fluidity, which allows it to fill small and intricate mold sections. The pouring temperature is carefully controlled to ensure that the iron flows smoothly into the mold without creating defects such as cold shuts or sand inclusions. As the molten iron cools and solidifies, it takes the shape of the cavity provided by the mold.
After the casting has cooled sufficiently, the mold is broken apart to reveal the finished metal part. This phase involves removing any excess sand and performing finishing operations such as grinding or machining to achieve the desired surface quality and dimensional tolerance. The whole process can take anywhere from a few hours to several days, depending on the size of the cast and the specific requirements of the project.
Advantages of Sand Casting Iron
One of the primary advantages of sand casting is its versatility. It can accommodate almost any design complexity and produce parts of varying sizes, from small components to large engine blocks. Sand casting also allows for the use of different types of iron, including gray iron, ductile iron, and malleable iron, each offering distinct mechanical properties suitable for different applications.
sand casting iron
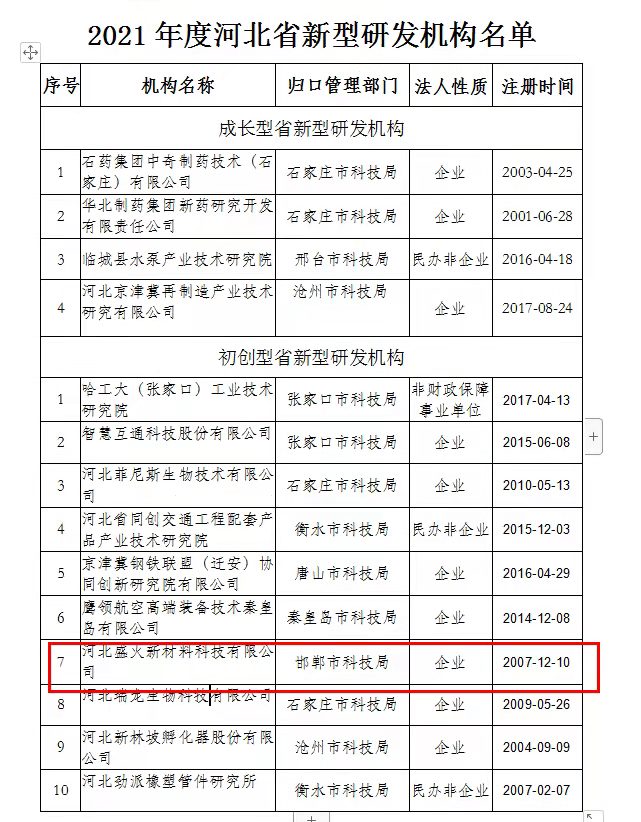
Another significant advantage is the relatively low cost associated with the materials and equipment involved in sand casting. Sand is abundant and inexpensive, and the setup for sand casting does not require extensive tooling or expensive machinery. This cost-effectiveness, combined with the capability to produce high-quality metal parts, makes sand casting a popular choice for many industries, including automotive, aerospace, and construction.
Moreover, sand casting allows for a high degree of recycling. Used sand can often be reclaimed and reused for future casts, minimizing waste and contributing to sustainable manufacturing practices. This eco-friendly aspect is increasingly important as industries look for ways to reduce their environmental footprint.
Challenges and Innovations
Despite its many advantages, sand casting does have its challenges. The process can be labor-intensive, and ensuring a consistent quality of the cast parts can sometimes be difficult. Issues such as sand erosion or layout complications can lead to defects.
However, innovation within the field is constantly evolving. The integration of computer-aided design (CAD) and computer-aided manufacturing (CAM) technologies has enhanced the precision and efficiency of the sand casting process. These advancements allow for better simulation, modeling, and analysis of the casting process, thus minimizing errors and improving the overall quality of cast products.
Conclusion
In conclusion, sand casting iron remains a fundamental technique in metalworking, admired for its versatility, economy, and ability to produce complex shapes. As technology advances, so does the potential for sand casting to meet the demands of modern manufacturing while embracing environmentally friendly practices. Whether for large-scale industrial applications or bespoke components, sand casting will continue to play a vital role in the production of iron parts for years to come.
Post time:dec . 02, 2024 04:24
Next:foundry sand definition