Sand for Casting An Essential Element in Foundry Operations
Casting is one of the oldest manufacturing processes known to humanity. It involves pouring molten material, typically metal, into a mold to create complex shapes that would be challenging and expensive to produce using other methods. Among the various materials used in casting, sand plays a pivotal role, especially in the foundry industry. The versatility, availability, and unique properties of sand make it a preferred choice for many casting applications.
Types of Sand Used in Casting
The primary type of sand used in casting applications is silica sand, primarily composed of silicon dioxide. This type of sand is preferred due to its high melting point, durability, and ability to withstand the thermal shock produced during the casting process. However, not all silica sand is created equal. Foundries often select specific grades of sand depending on the requirements of the casting operation, which may include grain size, shape, and surface texture.
Another popular type of sand used in casting is resin-bonded sand. This type of sand features a mixture of silica sand and a polymer resin, which enhances its binding properties. Resin-bonded sands enable the production of more detailed and precise molds compared to traditional greensand, which is a mixture of silica sand, clay, and water. Each of these sand types presents unique advantages and can be selected based on the specific needs of a project.
Properties of Casting Sand
sand for casting
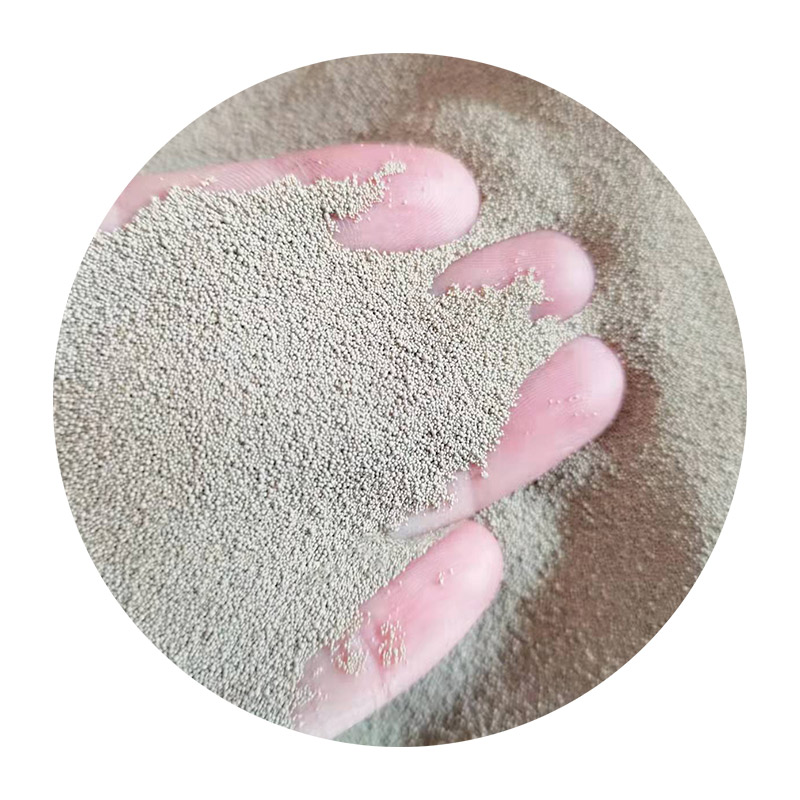
The effectiveness of sand in casting is attributed to several crucial properties. First and foremost is its flowability, allowing the sand to fill the intricacies of a mold accurately. Additionally, the sand needs to possess good collapsibility so that it can easily separate from the finished casting without damaging it. The thermal stability of the sand also plays an essential role, as it must withstand high temperatures without deteriorating or fusing together.
Another important characteristic is the bonding capability of the sand. In the case of greensand, the clay within the mixture serves as a binder, which helps maintain the mold’s integrity during the casting process. In contrast, resin-bonded sands rely on the chemical properties of the resin to create a rigid mold that holds its shape under the added pressure of molten metal.
Environmental Considerations
As the demand for sustainable practices grows, the foundry industry is adapting by exploring environmentally friendly alternatives to traditional casting sands. Innovations such as ceramic sand and reclaimed sands are gaining traction. Ceramic sand can withstand even higher temperatures than silica sand, making it an excellent choice for high-performance castings. Reclaimed sands, which are recycled and reused, not only reduce waste but also minimize the demand for new sand, addressing environmental concerns associated with mining.
Conclusion
In summary, sand remains an indispensable component in the casting process. Its unique properties, combined with various types tailored to specific applications, ensure that it continues to be the material of choice for foundries worldwide. As industries evolve and embrace sustainability, the future of casting sand will likely see innovative practices and materials that further enhance its utility while minimizing environmental impacts. As we move forward, the adaptability of sand and the ingenuity of foundry practices will continue to shape the landscape of manufacturing.
Post time:sep . 07, 2024 10:26
Next:Sand Casting Technology - Comprehensive Guide to the Casting Process