What is Sand Casting Used For?
Sand casting, also known as sand mold casting, is one of the oldest and most widely used metal casting processes. This traditional method involves creating a mold from sand in which molten metal is poured to create various shapes and objects. Sand casting is favored in many industries due to its adaptability, cost-effectiveness, and ability to produce intricate shapes.
Applications of Sand Casting
1. Automotive Industry Sand casting is extensively used in the automotive sector for manufacturing engine blocks, cylinder heads, and transmission cases. Given the complexity and size of these components, sand casting allows for production on a large scale while maintaining precision and reducing costs.
2. Aerospace Components The aerospace industry employs sand casting to produce lightweight and durable parts such as brackets, housings, and components that meet stringent safety standards. The ability to cast complex shapes minimizes the need for additional machining processes, which is crucial in aerospace manufacturing.
3. Art and Sculpture Artists and sculptors utilize sand casting to create intricate designs and sculptures. This technique allows them to produce unique pieces that can capture fine details and complex geometry, often regarded as a blend of art and technology.
4. Industrial Equipment Many industrial components, such as pumps, valves, and gears, are produced using sand casting. The process enables manufacturers to create large, heavy parts with excellent mechanical properties, essential for the durability and reliability of industrial machinery.
5. Marine Industry Sand casting plays a significant role in the marine industry, particularly in the production of components for ships and boats. Parts such as propellers, engine mounts, and housing for various machinery are often cast using this method due to the corrosion-resistant alloys that can be produced.
what is sand casting used for
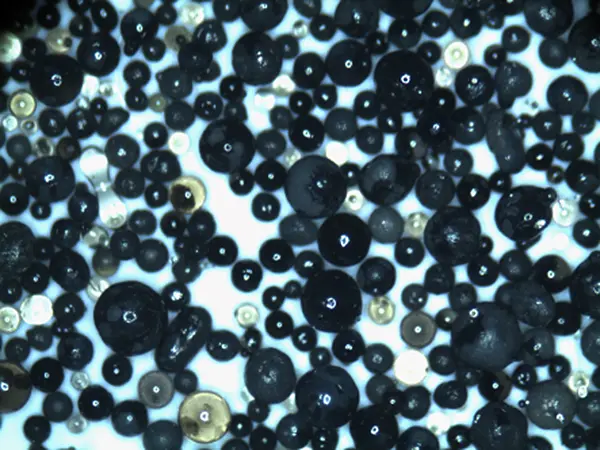
6. Construction Sector The construction industry also benefits from sand casting when producing fittings, brackets, and other structural components. The versatility of sand molds allows for the production of items tailored to specific project requirements.
Advantages of Sand Casting
- Cost-Effectiveness One of the primary advantages of sand casting is its lower cost compared to other casting methods, such as investment casting or die casting. The materials and equipment involved are relatively inexpensive, making it an attractive option for low to medium-volume production.
- Flexibility Sand casting offers great flexibility as it can accommodate a wide range of materials, including aluminum, bronze, brass, and iron. This versatility allows manufacturers to choose the best metal for their specific application.
- Ability to Cast Complex Shapes The sand mold can be easily shaped and modified, allowing for the production of intricate designs that would be challenging with other casting methods. The process can also handle large parts and complex internal geometries.
- Simplicity of the Process Sand casting is relatively straightforward and does not require specialized machinery, making it easier for smaller manufacturers to implement. The basic principle of making a mold from sand followed by pouring molten metal remains consistent, allowing for scalability and ease of training.
Conclusion
Sand casting remains a vital technique in modern manufacturing, transcending various industries, from automotive to aerospace and beyond. Its unique blend of cost-effectiveness, versatility, and capability to produce complex geometries ensures that it will continue to play a significant role in the creation of components for years to come. As technology advances, innovations in sand casting processes are expected to enhance efficiency, reduce waste, and further expand its applications, making it an essential method in the world of manufacturing.
Post time:Oct . 16, 2024 18:39
Next:Understanding the Characteristics and Applications of Foundry Sand in Metal Casting