Understanding Sand Casting Prices An In-Depth Look
Sand casting is one of the oldest and most widely used manufacturing processes in the metalworking industry. It involves creating a mold from sand to form metal parts. This method is favored for its ability to produce complex shapes, its cost-effectiveness for small to large production runs, and the wide range of materials that can be used. However, one significant aspect that often concerns manufacturers and customers alike is the price associated with sand casting. This article aims to provide an in-depth analysis of the factors affecting sand casting prices, its benefits, and considerations for businesses looking to utilize this valuable manufacturing process.
Key Factors Influencing Sand Casting Prices
1. Material Costs The type of metal used significantly impacts the overall price. Common materials for sand casting include aluminum, iron, steel, and bronze. Each material has its own market price that fluctuates based on supply and demand, alloying elements required, and even global market conditions. For instance, aluminum may be cost-effective but can vary based on the purity and specific alloys utilized for the casting process.
2. Mold Complexity The complexity of the mold directly affects the price of sand casting. More intricate designs typically require more time and resources to create, leading to higher costs. Features such as undercuts, consistent wall thickness, and fine detail estimates influence the amount of sand and other materials needed, plus the overall labor involved in the molding process.
3. Production Volume The scale of production plays a vital role in determining pricing. Generally, the cost per unit decreases as the volume increases due to economies of scale. A one-time, custom casting will have a significantly higher per-unit cost compared to mass production runs. Businesses often seek to negotiate better prices for larger orders, capitalizing on their need for consistent and repeatable parts.
4. Lead Time The urgency of the project can impact pricing. Rush orders often incur higher costs due to prioritized labor and resource allocation. Manufacturers juggle multiple orders at different stages, so hastening production times can lead to increased prices.
5. Post-Processing and Finishing After the initial casting, parts may require additional machining, finishing processes like sandblasting, painting, or plating, which incur further costs. The complexity and extent of the finishing work will add to the final pricing of the product.
Benefits of Sand Casting
sand casting price
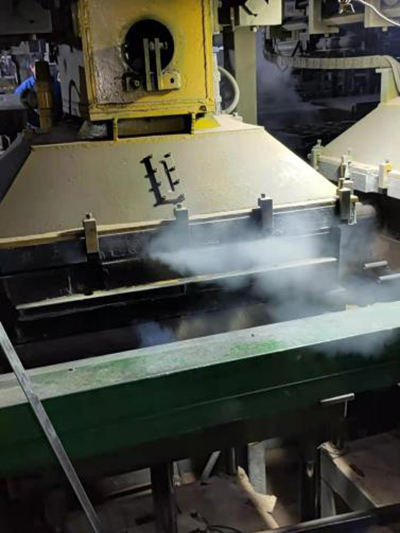
Despite the influences on pricing, sand casting offers numerous advantages that make it a preferred choice for manufacturers.
- Versatility Sand casting is capable of producing a variety of shapes and sizes, making it suitable for a range of industries including automotive, aerospace, and construction. - Cost-Efficiency For low to medium production volumes, sand casting remains one of the most cost-effective methods, as the mold can be reused and the materials are generally inexpensive.
- Material Flexibility Sand casting can accommodate a wide array of metals and alloys, allowing manufacturers to choose the best material for the job without significantly raising costs.
Considerations for Potential Customers
When evaluating sand casting for their needs, businesses should consider the total cost implications carefully. It is advisable to obtain quotes from multiple foundries to compare not only base prices but also lead times, quality assurance processes, and customer service options.
Additionally, companies should also assess the total lifespan and durability of the parts being created, juxtaposed against initial costs. Sometimes, a slightly higher upfront investment can lead to long-term savings if the parts offer better performance or require less maintenance.
Conclusion
Understanding sand casting prices requires a holistic view of the casting process and its many variables. From material costs and mold complexity to production volume and post-processing needs, the final cost visible on a quoted invoice represents a multitude of factors at play. For manufacturers and consumers alike, a detailed analysis and understanding of these elements can lead to informed decisions, potentially resulting in successful casting projects that meet both budgetary constraints and quality expectations. As the industry evolves, it remains vital to stay informed about market trends and pricing structures to effectively navigate the world of sand casting.
Post time:Dec . 16, 2024 23:05
Next:what is sand casting process