Understanding the Factors Influencing Sand Casting Prices
Sand casting is one of the most widely used metal casting processes due to its versatility, cost-effectiveness, and ability to produce complex shapes. Industries ranging from automotive to aerospace rely on this technique for manufacturing parts. However, one of the most pressing concerns for manufacturers and businesses alike is the price associated with sand casting. Understanding the factors that influence sand casting prices is essential for making informed decisions in procurement and production.
1. Material Costs
The primary factor affecting sand casting prices is the cost of raw materials. The type of metal being cast plays a significant role in determining the overall expense. Common materials used in sand casting include aluminum, iron, and steel. Prices for these metals fluctuate based on market demand, availability, and global economic conditions. For instance, during a surge in construction or automotive manufacturing, the demand for specific alloys may skyrocket, leading to higher prices. Additionally, the quality of sand used for casting can also impact costs, as finer sand generally leads to better surface finish but may be more expensive.
2. Mold and Core Costs
The complexity of the design and the size of the mold significantly influence the price of sand casting. Producing intricate designs requires more advanced molds, which can be time-consuming and costly. The creation of cores made from sand is also essential for parts with hollow sections, and the design and manufacturing of these cores can add to the overall cost. If a project demands a high volume of parts, manufacturers may opt for higher initial setup costs in exchange for a reduced price per unit in large-scale production.
3. Labor and Manufacturing Processes
Labor costs are another critical component of sand casting prices. The casting process involves several stages, including pattern making, mold preparation, pouring, and finishing. Skilled labor is necessary for each step, particularly in ensuring the precision of molds and cores, as well as in finalizing the cast products. Labor cost variations can also depend on the geographical location of the foundry and the expertise of the workforce. In regions where labor is more expensive, the cost of sand casting will likely be higher.
sand casting price
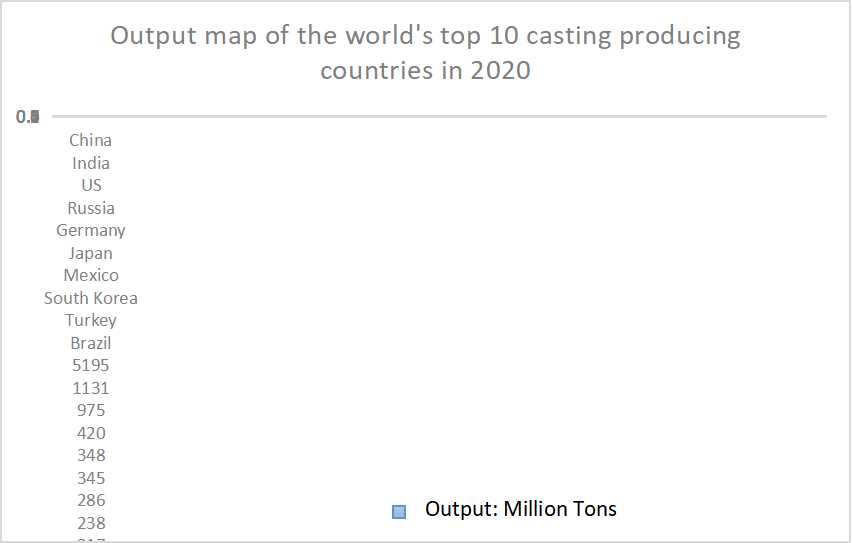
4. Production Volume and Lead Time
The volume of the order can greatly influence the price per unit. Generally, the more units produced, the lower the cost per unit, thanks to economies of scale. However, if a client needs a small volume of parts or requires expedited production due to tight deadlines, prices may increase to cover the added labor and machine running time. Manufacturers often balance the cost of production against the urgency of the order, leading to variations in pricing depending on the client’s needs.
5. Quality and Finishing Requirements
The desired quality and finishing of the final product also play a significant role in determining sand casting prices. Higher quality standards, such as those required in aerospace or medical applications, necessitate stricter quality control measures and additional finishing processes. Components may require additional machining, polishing, or coatings to meet specific requirements, which adds to the overall cost. Manufacturers will often provide a range of pricing options based on the client’s quality expectations.
6. Environmental Considerations
In recent years, environmental regulations have also impacted sand casting prices. Foundries are increasingly required to implement measures to reduce emissions and manage waste, which can lead to higher operating costs. Compliance with these regulations may necessitate investments in new technologies or processes, costs that are ultimately passed on to the consumer.
Conclusion
Evaluating the cost of sand casting involves understanding the interplay of various factors, including material costs, labor, complexity of designs, volume, quality requirements, and environmental regulations. Companies looking to utilize sand casting in their production lines should engage in thorough research and communicate effectively with suppliers to obtain the best prices. By considering these influential factors, businesses can make strategic decisions that align their production needs with budgetary constraints, ensuring a successful outcome in their casting projects.
Post time:Nov . 06, 2024 18:32
Next:Inspired by golden sanda, discover your perfect blend of style and comfort today