The resin-coated sand process has gained significant traction in the foundry industry, serving as a crucial technology for producing high-quality metal castings. This innovative method involves coating sand grains with a specially formulated resin, which enhances the properties of the sand and improves the overall casting process.
.
The process typically starts with the selection of high-quality silica sand, which is then coated with a thermosetting resin. This resin, often a phenolic or furan type, binds the sand grains together, creating a durable mold that can withstand the rigors of the casting environment. After the sand is coated, it is cured using heat, ensuring that the resin hardens and forms a strong bond between the grains. This curing process significantly enhances the mechanical properties of the sand, making it suitable for various casting applications.
resin coated sand process
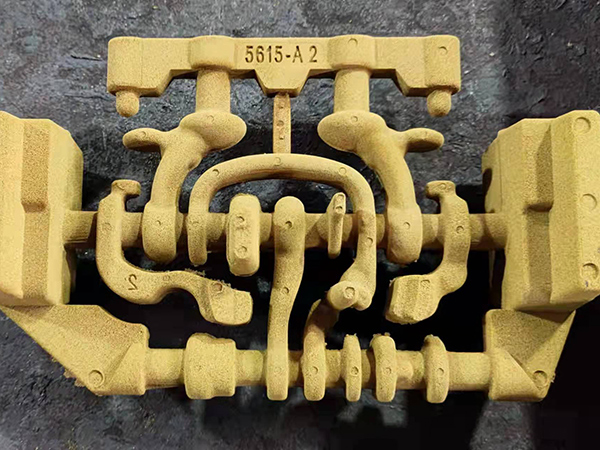
Environmental considerations have also led to increased interest in the resin-coated sand process. Traditional casting methods often involve the use of toxic binders and materials that can harm the environment. In contrast, many resin systems used in this process are designed to be more eco-friendly, reducing the overall environmental impact of casting operations. Additionally, the ability to recycle resin-coated sand after casting further contributes to sustainability in the foundry sector.
The resin-coated sand process is particularly beneficial in industries such as automotive, aerospace, and general manufacturing, where precision and reliability are paramount. As technology continues to advance, innovations in resin formulations and coating techniques promise to enhance the efficiency and effectiveness of this process even further.
In conclusion, the resin-coated sand process is a vital advancement in the field of metal casting, offering improved mold strength, precision, and environmental sustainability. As foundries increasingly adopt this technology, we can expect significant improvements in the quality of castings produced and a reduction in the environmental footprint of the casting industry. The future of this process looks bright, with ongoing research and development paving the way for even better solutions and applications.
Post time:Oct . 13, 2024 04:19
Next:सुपर सैंड जी2 की विशेषताएँ और उपयोग के लाभ