Properties of Foundry Sand
Foundry sand is a crucial component in the metal casting industry, where it is used to create molds and cores for casting metals into various shapes and forms. The properties of foundry sand significantly influence the quality of the final product, making it essential to understand its characteristics. This article delves into the various properties of foundry sand, including its composition, grain characteristics, permeability, moisture content, and thermal stability.
Composition
Foundry sand is primarily composed of silica (SiO2), accounting for about 85-95% of its composition. Other components may include alumina, iron oxides, and various minerals. The purity and grain size of the silica play a critical role in determining the sand's performance in the casting process. Silica sands are favored for their high melting point and resistance to thermal shock, which are vital for withstanding the high temperatures during metal casting.
Grain Characteristics
The grain shape, size, and distribution of foundry sand are of utmost importance. The ideal sand for foundry applications should possess round grains, as they enable better flowability and compaction. Angular grains, on the other hand, may lead to higher friction during the compaction process, which could affect the mold's integrity. The grain size typically ranges from 0.1 mm to 0.5 mm, with finer sands being used for intricate designs and coarser sands for larger applications. The distribution of grain sizes also contributes to mold strength, with a well-graded sand mix providing better packing density.
Permeability
properties of foundry sand
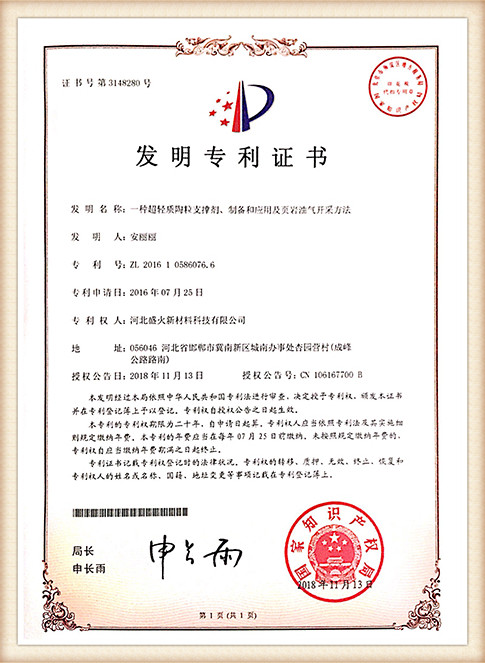
Another key property of foundry sand is its permeability, which refers to the ability of air and gases to pass through the sand mold. Adequate permeability is vital to allow gases generated during the casting process to escape; otherwise, trapped gases can cause defects in the final product, such as blowholes or surface imperfections. The permeability of foundry sand is influenced by its grain size, shape, and moisture content. A balance must be struck between permeability and mold strength, as overly permeable sands may lack the necessary structural integrity to hold their shape under the weight of molten metal.
Moisture Content
Moisture content is a critical attribute that affects the bonding and strength of the sand mold. The optimal moisture content for foundry sand typically ranges from 2% to 5%. Higher moisture levels can lead to clumping and decreased flowability, while too little moisture can result in a dry mold that doesn't hold its shape. The ability to control moisture content is significant, as it directly affects the molding process and the quality of the cast product. Water is also used to activate bonding agents during the molding process, further emphasizing the importance of managing moisture levels.
Thermal Stability
Thermal stability is essential for foundry sand, as it must withstand high temperatures without deforming or melting. The thermal expansion characteristics of the sand should be compatible with the metals being cast; otherwise, thermal shock can cause cracking or other defects. Foundry sands must maintain their structural integrity when exposed to molten metal, which can reach temperatures of up to 1500°C (2732°F). The thermal stability of sands is influenced by their mineral composition, with certain additives being introduced to enhance their heat resistance.
Conclusion
In summary, the properties of foundry sand—composition, grain characteristics, permeability, moisture content, and thermal stability—are critical in determining the success of the metal casting process. Understanding these properties allows foundry operators to select the appropriate type of sand for specific applications, ensuring the production of high-quality castings. As the industry continues to evolve, innovations in foundry sand formulations and processing will likely improve performance and sustainability, making it a vital area of focus for manufacturers in the metalworking sector. By optimizing these properties, foundries can enhance efficiency, reduce defects, and ultimately produce superior cast products that meet the demands of modern industries.
Post time:Dec . 03, 2024 10:26
Next:how to sand small 3d prints