Parts of Sand Casting Understanding the Fundamental Components
Sand casting is a widely used manufacturing process that involves the creation of metal castings through the use of sand molds. This method is cherished for its versatility, cost-effectiveness, and ability to produce complex shapes. To grasp the intricacies of sand casting, one must understand the various components involved in the process. This article delves into the essential parts of sand casting, their functions, and their significance.
1. Pattern The pattern is a crucial component of the sand casting process. It is a replica of the final product, usually made from materials like wood, metal, or plastic. Patterns can be simple or highly complex, depending on the geometry of the desired casting. They are created larger than the final product to account for shrinkage during cooling. Patterns can be classified into different types, including solid, split, or core patterns, depending on the requirements of the casting.
Parts of Sand Casting Understanding the Fundamental Components
3. Cores Cores are used to create internal cavities or shapes within the casting. Made from similar sand mixtures, cores are placed in the mold before the molten metal is poured in. This allows manufacturers to define complex internal geometries that would be impossible to achieve with a simple mold. Cores can be secured using core prints, which are features on the pattern that help to hold them in place during the pouring process.
parts of sand casting
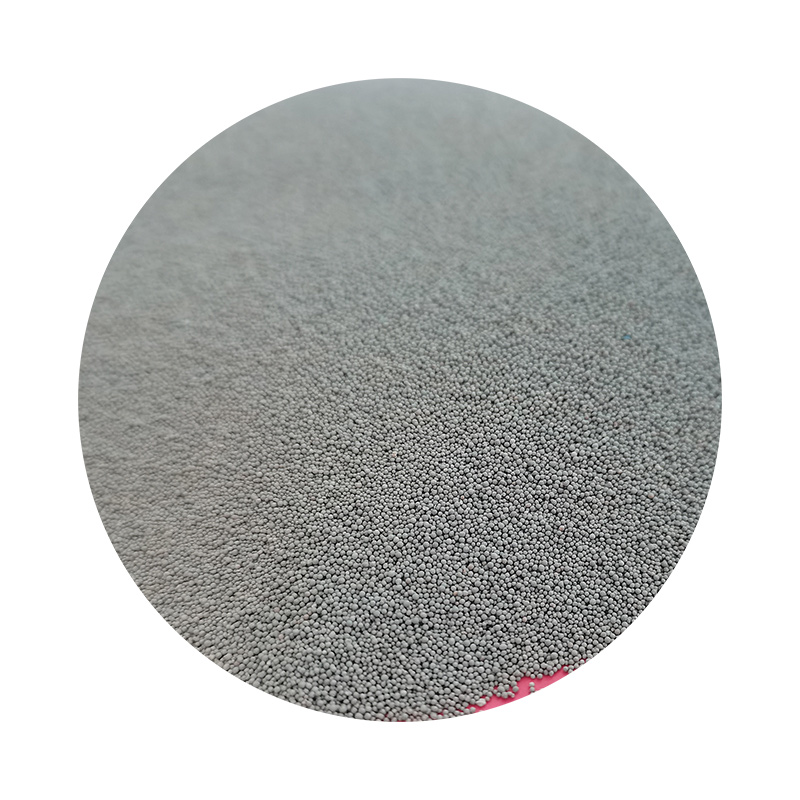
4. Melting Furnace The melting furnace is where the metal is converted from solid form to liquid. Depending on the type of metal being cast, different types of furnaces are used, such as electric arc furnaces, induction furnaces, or crucible furnaces. The choice of furnace depends on the metal’s melting point, the required precision, and efficiency. The molten metal is then ladled from the furnace and poured into the prepared mold.
5. Pouring System The pouring system is critical for the successful transfer of molten metal into the mold. This system comprises pouring cups, gates, and runners, which help guide the metal from the ladle to the mold cavity. Proper design of the pouring system is essential to minimize turbulence and ensure a smooth flow, thus reducing the risk of defects in the final casting.
6. Cooling and Solidification After pouring, the metal must cool and solidify to take on the shape of the mold. The cooling process is influenced by factors such as wall thickness, ambient temperature, and the thermal conductivity of the material. It is essential to control cooling rates to minimize defects like warping or cracking in the final product.
7. Finishing Process Once the metal has cooled and solidified, the mold is broken apart to retrieve the casting. The casting often requires several finishing processes, including sanding, grinding, and machining, to achieve the desired surface finish and dimensional accuracy. This step may also involve removing any excess material known as flash, which can occur where the mold halves meet.
Conclusion Understanding the various parts of the sand casting process is essential for anyone involved in manufacturing or engineering. From the creation of the pattern to the final finishing touches, each component plays a vital role in producing high-quality castings. The flexibility and adaptability of sand casting make it an enduring and popular choice in various industries, including automotive, aerospace, and machinery manufacturing. As technology advances, the sand casting process continues to evolve, integrating modern techniques to enhance efficiency and precision.
Post time:Oct . 19, 2024 05:05
Next:sand casting tolerances