Metal Sand Casting An Essential Manufacturing Process
Metal sand casting is a significant manufacturing technique that has been employed for centuries, providing a versatile and efficient method to produce metal components. This process involves creating a mold from sand, which is then filled with molten metal to form various parts and products. Due to its adaptability and cost-effectiveness, sand casting remains popular in many industries, including automotive, aerospace, and machinery.
The Sand Casting Process
The sand casting process begins with constructing a mold. The primary material used for the mold is sand, typically mixed with a binding agent such as clay. The quality of the sand is crucial as it determines the mold's ability to hold shape and withstand the temperatures of molten metal. Once the sand mixture is prepared, it is packed around a pattern, which is a replica of the final product. After compacting the sand, the pattern is removed, leaving a cavity in the shape of the desired piece.
Next comes the pouring of the molten metal. The metal, heated to its melting point, is carefully poured into the mold cavity. This step requires precision, as any irregularities can lead to defects in the final product. Once the metal cools and solidifies, the mold is broken away, revealing the cast metal part. The final step involves cleaning, inspecting, and, if necessary, machining the component to achieve the desired specifications.
Advantages of Sand Casting
One of the most significant advantages of sand casting is its flexibility. It can accommodate a wide range of metal types, including iron, aluminum, and bronze. This versatility makes it suitable for various applications, from small components to large structural parts. Additionally, sand casting can produce intricate shapes and designs that may be challenging to achieve with other manufacturing methods.
Cost-effectiveness is another significant benefit. Sand casting does not require extensive machinery or tooling, making it an ideal choice for small production runs or one-off parts. The materials used in sand casting are relatively inexpensive, and the process can be executed with minimal labor, further reducing costs.
metal sand casting
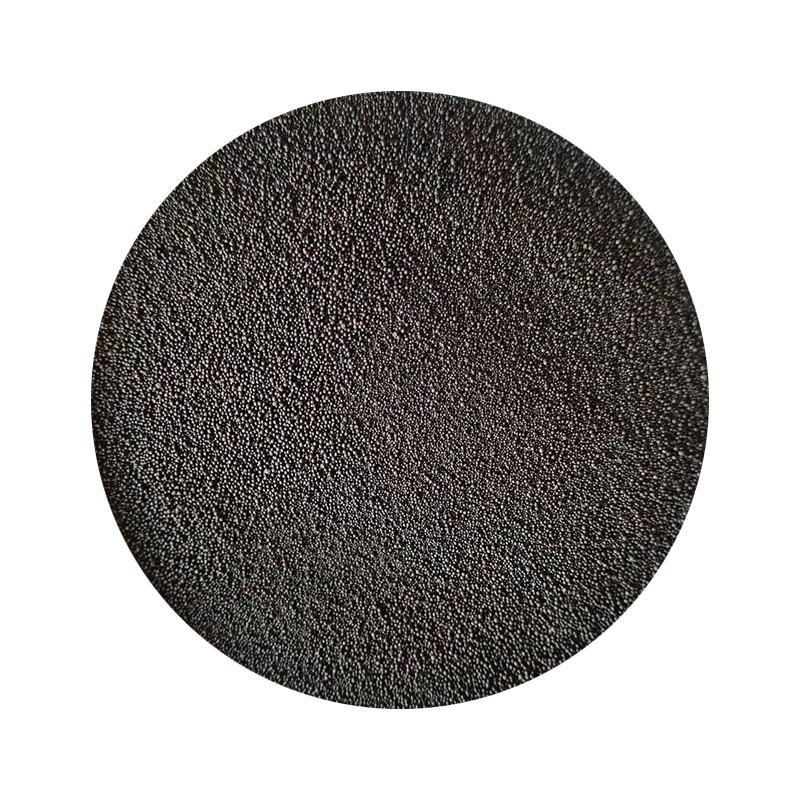
Moreover, sand casting allows for the recycling of materials. Used sand can be reclaimed and reused, minimizing waste and contributing to more sustainable manufacturing practices. This is becoming increasingly important in an era where environmental concerns are driving industries to seek sustainable solutions.
Challenges and Solutions
Despite its advantages, metal sand casting is not without its challenges. The process can lead to various casting defects, such as porosity, inclusions, or surface roughness. These defects can impact the mechanical properties and aesthetics of the final product. Engineers and manufacturers continuously work on improving methods to minimize these issues, employing computer simulation software to predict potential defects before production. Additionally, advancements in sand mold materials and coating technologies have improved the surface finish and overall quality of cast components.
Applications of Metal Sand Casting
Metal sand casting has a wide array of applications across different industries. In the automotive sector, it is commonly used to manufacture engine blocks, transmission cases, and various other components. In the aerospace industry, sand casting is utilized for producing parts that require high strength-to-weight ratios, such as housings and brackets.
The versatility of sand casting also extends to the arts and sculpture. Artists often use this technique to create intricate metal sculptures, showcasing the adaptability of sand casting beyond industrial applications.
Conclusion
In summary, metal sand casting is a vital manufacturing process that has stood the test of time. Its combination of versatility, cost-effectiveness, and adaptability makes it an essential technique for producing a wide array of metal components across various industries. While challenges exist, continuous advancements in technology and materials promise to improve the quality and efficiency of sand casting, ensuring its relevance in modern manufacturing for years to come.
Post time:Nov . 27, 2024 05:35
Next:Innovative Materials for Lost Foam Casting Processes in Metal Fabrication