Materials Used for Sand Casting
Sand casting, one of the oldest and most versatile metal casting processes, involves pouring molten metal into a sand mold to create a desired shape. While the process itself is fascinating, the choice of materials plays a pivotal role in determining the quality and success of the sand casted product. This article explores the various materials commonly used in sand casting, focusing on sand, binders, metal, and additives.
Sand
The primary material in sand casting is, unsurprisingly, sand. The type of sand used is critical, as it influences the mold's ability to withstand the heat of molten metal, the detail of the final cast, and the ease of mold production. The most commonly used sand in sand casting is silica sand, which is favored for its high melting point and availability. Silica sand comes in various grades, with the finest grains offering better surface finishes on the final product.
Another popular type of sand is olivine sand, derived from the mineral olivine. Olivine sand provides excellent thermal stability and resistance to high temperatures, making it suitable for casting iron and steel. However, olivine sand is more expensive than silica sand, which can make it less desirable for certain applications.
Binders
While sand provides the primary structure for the mold, binders are essential for holding the sand grains together
. Two of the most widely used binder materials in sand casting are clay and chemical binders.Clay, particularly sodium bentonite, is traditionally used in green sand casting, which combines moisture and clay to form a mold. The clay binds the sand grains effectively while providing a certain degree of flexibility, which is vital for a clean release of the cast from the mold.
materials used for sand casting
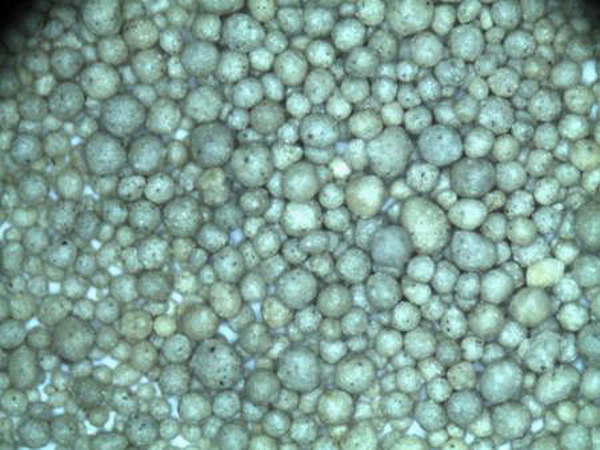
Chemical binders, such as phenolic urethane and epoxy, are increasingly popular, especially in modern sand casting applications. These binders harden quickly and can produce molds with much finer details and better dimensional accuracy compared to traditional green sand casting. However, they can be more costly and may have environmental and health considerations due to the chemicals involved.
Metals
A crucial aspect of materials used in sand casting is the choice of metal itself. The metals selected for sand casting should have suitable properties such as fluidity, thermal conductivity, and solidification characteristics.
Commonly used metals in sand casting include cast iron, aluminum alloys, and bronze. Cast iron is favored for its excellent casting properties and ability to withstand wear, making it perfect for engine blocks and heavy machinery components. Aluminum alloys, on the other hand, are lightweight, corrosion-resistant, and possess good thermal and electrical conductivity, which makes them suitable for automotive and aerospace applications. Bronze, an alloy of copper and tin, is primarily used for artistic applications and marine hardware due to its excellent corrosion resistance.
Additives
In addition to sand, binders, and metals, various additives can enhance the casting process and final product quality. One of the most common additives is coal dust, which is used in green sand to improve its flowability and reduce casting defects. Other additives include rust inhibitors and drying agents that can help in mold preparation and ensure that moisture levels are appropriate for the casting process.
Conclusion
The materials used in sand casting are integral to the success of the casting process and the quality of the final product. Understanding the properties and interactions of these materials—sand, binders, metals, and additives—can significantly enhance the efficiency of the casting operation and the performance of the manufactured components. By tailoring the selection of materials to meet the specific requirements of each casting project, manufacturers can achieve desired characteristics and maintain high standards of quality, ultimately leading to greater satisfaction for both producers and consumers alike. As technology advances and new materials emerge, the sand casting process will continue to evolve, providing even more opportunities for innovation in this age-old manufacturing technique.
Post time:Oct . 15, 2024 06:46
Next:sand casting history