Low Pressure Sand Casting An Innovative Approach to Metal Casting
Low pressure sand casting is a specialized manufacturing process that has gained significant attention in the metalworking industry. As the name suggests, this technique employs low pressure to facilitate the flow of molten metal into sand molds. Unlike traditional sand casting methods, which often use gravitational forces, low pressure sand casting offers several advantages, including improved surface finish, enhanced dimensional accuracy, and reduced defects. This article will explore the principles, advantages, applications, and future prospects of low pressure sand casting.
Principles of Low Pressure Sand Casting
The core concept of low pressure sand casting revolves around the controlled introduction of molten metal into a sand mold. The process begins by creating a mold from a mixture of sand, resin, and hardening agents. Once the mold is prepared, it is heated to a high temperature to strengthen its structure.
In low pressure sand casting, a furnace is used to melt the desired metal, which is then transferred to a holding ladle. Molten metal is introduced into the mold through a pressurized system, typically at pressures ranging from 0.5 to 2 bar (7.25 to 29 psi). This low-pressure technique allows the metal to flow into intricate sections of the mold, filling cavities that might be challenging to achieve with gravity-based casting.
The process allows for more uniform cooling and solidification of the metal, reducing the chances of defects like porosity and shrinkage. After the metal has solidified, the sand mold is removed, and the cast part is trimmed and finished as required.
Advantages of Low Pressure Sand Casting
One of the primary advantages of low pressure sand casting is the superior quality of the castings produced. The method offers a better surface finish compared to traditional sand casting because the pressurized introduction of metal minimizes turbulence and reduces the likelihood of inclusions. This results in a smoother, more consistent surface that often requires less machining.
Another significant benefit is the improved mechanical properties of the final cast product. The controlled solidification process helps achieve a finer microstructure, which can enhance strength and durability.
Additionally, low pressure sand casting is highly versatile and can accommodate a wide range of alloys, including aluminum, magnesium, and zinc
. Its adaptability to different materials makes it suitable for a variety of applications, from automotive components to aerospace parts.low pressure sand casting
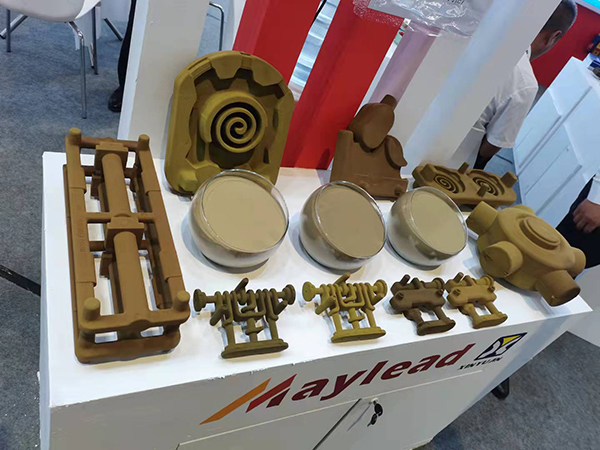
Moreover, the efficiency of this method leads to reduced material waste. The use of sand molds, which can be reused several times, further contributes to a more sustainable manufacturing process.
Applications of Low Pressure Sand Casting
Low pressure sand casting is utilized in various industries due to its versatility and quality. The automotive industry is one of the largest consumers of this casting method, producing engine blocks, transmission cases, and other critical components. The aerospace sector also benefits from low pressure sand casting for producing lightweight and complex parts, where precision and mechanical strength are paramount.
Moreover, industries such as HVAC, marine, and agricultural equipment use this casting technique for creating robust components. The ability to produce large quantities of parts with high accuracy makes low pressure sand casting an attractive option in mass production settings.
Future Prospects
As technology advances, the future of low pressure sand casting appears promising. With the increasing demand for lightweight materials and complex geometries, this method is likely to evolve, incorporating innovations in automation and digital manufacturing. The integration of computer-aided design (CAD) and computer-aided manufacturing (CAM) can streamline the production process, minimizing lead times and enhancing overall efficiency.
Furthermore, ongoing research into new materials and molding techniques may open the door to the production of even more intricate and robust components. As sustainability continues to be a priority for manufacturers worldwide, low pressure sand casting's efficient use of materials and energy will support its relevance in the coming years.
Conclusion
Low pressure sand casting represents a significant advancement in the field of foundry manufacturing. By leveraging controlled low-pressure techniques, it produces high-quality castings with excellent dimensional accuracy and surface finish. As industries continue to seek innovative solutions for complex manufacturing challenges, low pressure sand casting is poised to play a crucial role in the future of metal casting. Whether it’s for automotive, aerospace, or other applications, this method is set to leave a lasting impact on the manufacturing landscape.
Post time:Nov . 08, 2024 00:56
Next:Ceramic Sanding Discs for Superior Finishing and Surface Preparation Techniques