Types of Sand Used in Sand Casting
Sand casting is a versatile and widely used manufacturing process that involves creating parts by forming sand molds into which molten metal is poured. One of the key aspects of this process is the type of sand used, as it greatly influences the quality of the finished product. There are several types of sand commonly utilized in sand casting, each with distinct properties and applications.
1. Silica Sand Silica sand is the most commonly used type of sand in sand casting due to its availability and high melting point. It consists primarily of quartz, which provides excellent thermal properties and stability. Silica sand can withstand high temperatures, making it ideal for casting metals like iron and aluminum. Its fine texture helps in capturing intricate details of the mold, ensuring a good surface finish.
2. Green Sand Green sand is a mixture of silica sand, clay, and water. This type of sand is called green because it is moist and not hard yet. Green sand molds are easily shaped, reusable, and effective for small to medium-sized castings. The clay content helps bind the sand particles together and provides sufficient strength to maintain the shape during the pouring of molten metal.
types of sand used in sand casting
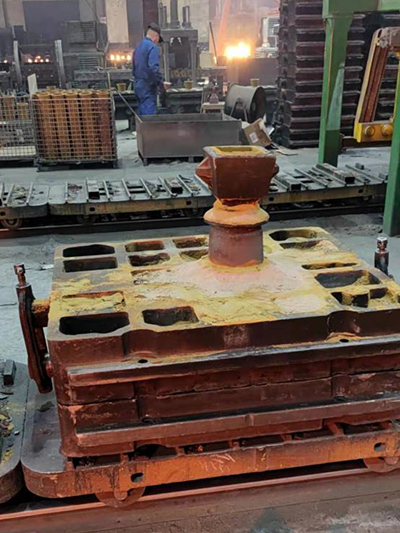
3. Resin Sand Resin sand consists of silica sand mixed with a thermosetting resin and a hardening agent. This type of sand is primarily used for precision casting due to its high strength and excellent dimensional stability. Resin sand molds can withstand higher pouring temperatures and are less prone to sand deformation, making them ideal for complex shapes and fine details.
4. Lost Foam Sand Lost foam sand casting employs a foam pattern made from expanded polystyrene (EPS), which is coated with a thin layer of sand and then vaporized during the pouring process. This technique allows for intricate designs and reduces the need for additional machining. The benefit of lost foam casting is that it produces a smooth surface finish while minimizing mold and core production.
5. Sodium Silicate Sand Sodium silicate sand, also known as water glass sand, utilizes sodium silicate as a binder. This type of sand offers good strength and can be cured quickly. It is often used in applications where moisture control is essential, as the sodium silicate helps in maintaining the integrity of the mold.
In conclusion, the choice of sand in the sand casting process is critical for achieving the desired quality and precision in castings. Each type of sand has unique properties that cater to different casting needs, influencing the efficiency and success of the manufacturing process.
Post time:нов . 14, 2024 11:55
Next:sand castings manufacturer